Download PDF
Schlumberger Owings Mills Improves Processes, Efficiencies with STATISTICA Enterprise-wide SPC System (SEWSS)
Technology Category
- Analytics & Modeling - Predictive Analytics
- Analytics & Modeling - Real Time Analytics
- Functional Applications - Manufacturing Execution Systems (MES)
Applicable Functions
- Process Manufacturing
- Quality Assurance
Use Cases
- Machine Condition Monitoring
- Predictive Maintenance
- Process Control & Optimization
Services
- System Integration
- Training
The Challenge
In 2001, Schlumberger Owings Mills Advanced Card Center Management faced the challenge of reducing costs from a product line experiencing a reduction in average selling price. Management decided to use Lean Sigma, a methodology for improvements through waste reduction and variation removal, to address this need.
About The Customer
Schlumberger Owings Mills Advanced Card Center is a manufacturing center for smart cards and magnetic stripe cards in the United States. A smart card is a plastic card, the same size as a banking card, with a silicon chip embedded in it. A microprocessor smart card’s chip contains a miniature computer that can perform calculations and store data in its memory. The card is 'smart' because it is 'active', in that it can receive information, process it and then 'make a decision.'
The Solution
The implementation of an SPC Program was performed in three major steps: altering the layout of the production process, organizational changes, and empowering employees with information and SPC tools. The first step was to change the layout of the plant to incorporate Manufacturing Cells, Inventory Kanbans, and 5S. The next step was to establish high-performance Teams, including Total Productive Maintenance (TPM) and Setup Reduction, and a problem-solving process. These teams wanted more information from the process. STATISTICA Enterprise-wide SPC System (SEWSS) is a software tool used to provide process information and facilitate the approach to chronic problems. SEWSS is used for data collection from each manufacturing cell, real-time Quality Control charting, and ad hoc analyses for needs such as Design of Experiments (DOE). With SEWSS, teams are easily trained in 1-2 hours to create and interpret control charts for quality control and supporting continuous improvement efforts of their manufacturing cell. Data summaries and analyses are easily and automatically aggregated into HTML reports for problem-solving presentations to the Steering Committee and Customers (both Internal and External). To improve insights into the status of key processes, Schlumberger Owings Mills uses SEWSS to automate the generation of key reports in HTML for daily review by the management team every morning.
Operational Impact
Quantitative Benefit
Related Case Studies.
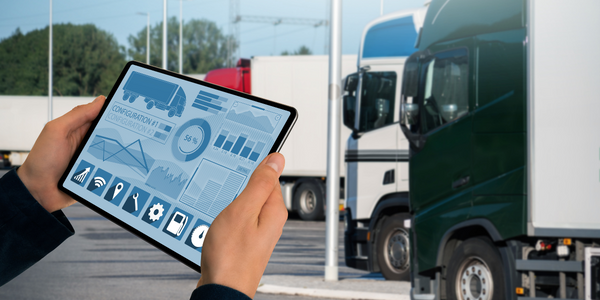
Case Study
IoT enabled Fleet Management with MindSphere
In view of growing competition, Gämmerler had a strong need to remain competitive via process optimization, reliability and gentle handling of printed products, even at highest press speeds. In addition, a digitalization initiative also included developing a key differentiation via data-driven services offers.
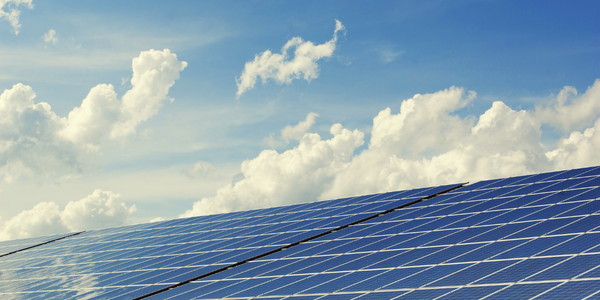
Case Study
Remote Monitoring & Predictive Maintenance App for a Solar Energy System
The maintenance & tracking of various modules was an overhead for the customer due to the huge labor costs involved. Being an advanced solar solutions provider, they wanted to ensure early detection of issues and provide the best-in-class customer experience. Hence they wanted to automate the whole process.
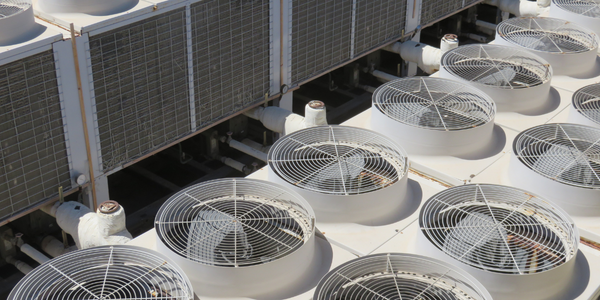
Case Study
Predictive Maintenance for Industrial Chillers
For global leaders in the industrial chiller manufacturing, reliability of the entire production process is of the utmost importance. Chillers are refrigeration systems that produce ice water to provide cooling for a process or industrial application. One of those leaders sought a way to respond to asset performance issues, even before they occur. The intelligence to guarantee maximum reliability of cooling devices is embedded (pre-alarming). A pre-alarming phase means that the cooling device still works, but symptoms may appear, telling manufacturers that a failure is likely to occur in the near future. Chillers who are not internet connected at that moment, provide little insight in this pre-alarming phase.
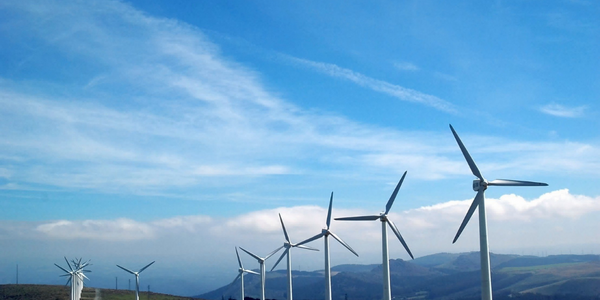
Case Study
Siemens Wind Power
Wind provides clean, renewable energy. The core concept is simple: wind turbines spin blades to generate power. However, today's systems are anything but simple. Modern wind turbines have blades that sweep a 120 meter circle, cost more than 1 million dollars and generate multiple megawatts of power. Each turbine may include up to 1,000 sensors and actuators – integrating strain gages, bearing monitors and power conditioning technology. The turbine can control blade speed and power generation by altering the blade pitch and power extraction. Controlling the turbine is a sophisticated job requiring many cooperating processors closing high-speed loops and implementing intelligent monitoring and optimization algorithms. But the real challenge is integrating these turbines so that they work together. A wind farm may include hundreds of turbines. They are often installed in difficult-to-access locations at sea. The farm must implement a fundamentally and truly distributed control system. Like all power systems, the goal of the farm is to match generation to load. A farm with hundreds of turbines must optimize that load by balancing the loading and generation across a wide geography. Wind, of course, is dynamic. Almost every picture of a wind farm shows a calm sea and a setting sun. But things get challenging when a storm goes through the wind farm. In a storm, the control system must decide how to take energy out of gusts to generate constant power. It must intelligently balance load across many turbines. And a critical consideration is the loading and potential damage to a half-billion-dollar installed asset. This is no environment for a slow or undependable control system. Reliability and performance are crucial.
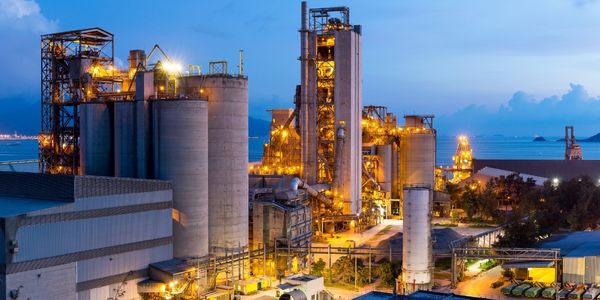
Case Study
System 800xA at Indian Cement Plants
Chettinad Cement recognized that further efficiencies could be achieved in its cement manufacturing process. It looked to investing in comprehensive operational and control technologies to manage and derive productivity and energy efficiency gains from the assets on Line 2, their second plant in India.
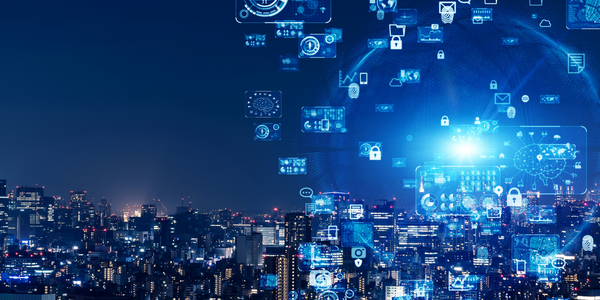
Case Study
Integration of PLC with IoT for Bosch Rexroth
The application arises from the need to monitor and anticipate the problems of one or more machines managed by a PLC. These problems, often resulting from the accumulation over time of small discrepancies, require, when they occur, ex post technical operations maintenance.