Download PDF
Silgan PFC Enhances Quality and Efficiency with Parsable
Technology Category
- Functional Applications - Computerized Maintenance Management Systems (CMMS)
Applicable Industries
- Packaging
- Paper & Pulp
Applicable Functions
- Maintenance
- Quality Assurance
Use Cases
- Supply Chain Visibility
- Visual Quality Detection
Services
- System Integration
- Testing & Certification
The Challenge
Silgan Plastic Food Containers (PFC), a global leader in high-barrier plastic packaging, faced several operational challenges. Despite being an industry leader, the company struggled with issues related to transparency and management of tasks. The documentation process was entirely paper-based, leading to a lack of clarity about who was responsible for what tasks and when they were completed. This lack of transparency affected operational results. Handing over responsibilities was also a challenge, especially when team members were absent. Missed tasks were difficult to address due to these issues. Additionally, Silgan was required to conduct one major audit and several smaller ones each year. However, the paper-based filing system made locating necessary documentation a time-consuming and difficult process.
About The Customer
Silgan Plastic Food Containers (PFC) is a global leader in the production of high-barrier plastic packaging for long shelf-life, ambient, microwaveable, convenience foods. The company supplies high-quality, innovative products to some of the world's most recognizable brands. Despite being an industry leader, Silgan PFC faced challenges related to transparency and management of tasks due to its paper-based documentation process. The company was also required to conduct several audits each year, a process made difficult by the opaque paper filing system.
The Solution
To address these challenges, Silgan PFC partnered with Parsable, a digital transformation service. The company aimed to standardize operations, keep pace with competitors, and ensure optimal product quality. Silgan implemented Parsable across various functional areas, including quality, production, safety, and maintenance, to address inefficiencies in routine processes. The partnership with Parsable allowed Silgan to consolidate all information into a single-source-of-truth system, enabling faster, higher-quality handoffs of information between departments. It also streamlined reporting by simplifying audits and provided digital traceability and new levels of accountability for employees and managers. The system also provided new data points for monitoring equipment trends, allowing for necessary corrections, and increased collaboration and visibility across various departments.
Operational Impact
Quantitative Benefit
Related Case Studies.
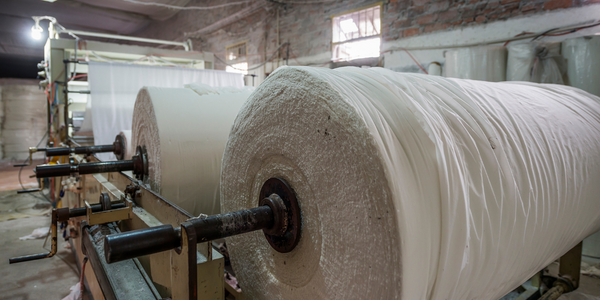
Case Study
Wireless Improves Efficiency in Compressed Air Systems
Hollingsworth and Vose wanted to improve the efficiency of their compressed air system, lower the electricity expense component of manufacturing cost in their commodity industry, and conserve energy leading to lowered greenhouse gas emissions. Compressed air systems degrade over time and become leaky and inefficient. Hollingsworth and Vose wanted to increase the frequency of system inspections without paying the high cost of manual labor.
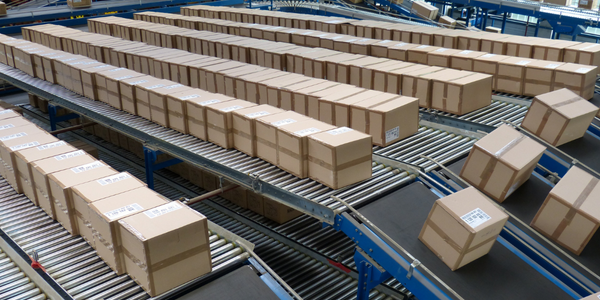
Case Study
IoT Data Analytics Case Study - Packaging Films Manufacturer
The company manufactures packaging films on made to order or configure to order basis. Every order has a different set of requirements from the product characteristics perspective and hence requires machine’s settings to be adjusted accordingly. If the film quality does not meet the required standards, the degraded quality impacts customer delivery causes customer dissatisfaction and results in lower margins. The biggest challenge was to identify the real root cause and devise a remedy for that.
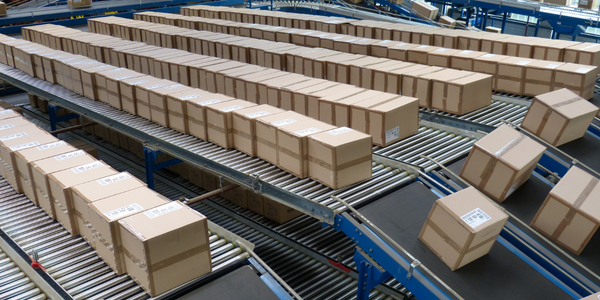
Case Study
Zenon the Ideal Basis for An Ergonomic HMI
KHS develops and produces machines and equipment for filling and packaging in the drinks industry. Because drinks manufacturing, filling and packaging consist of a number of highly complex processes, the user-friendly and intuitive operation of equipment is increasingly gaining in significance. In order to design these processes as simple as possible for the user, KHS decided to introduce a uniform, transparent and standardized solution to the company. The HMI interface should meet the requirement for people with different qualifications and enable them to work on a standard platform.
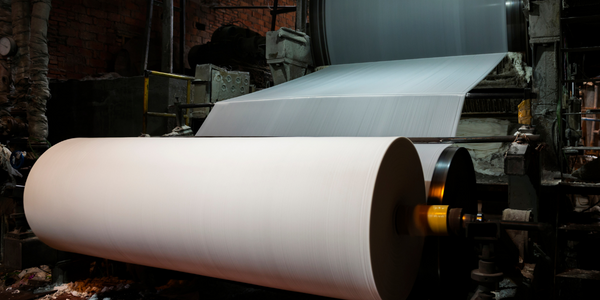
Case Study
Process Predictive Analysis in Pulp and Paper Mill
Common paper breaks consequently lead up to 60 minutes of downtime, delaying a potential $10K per hour of production value process. Thus, defective products cause financial and damage company's reputation. Improving quality and reducing defect rates can generate millions of dollars of revenue per year for your company.
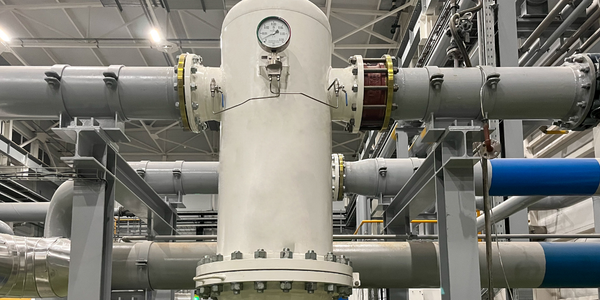
Case Study
Sparks Dynamics Assists Atlas Container Secure a $15,000 BGE Energy Rebate
The ReMASTER Compressed Air Monitoring system was installed in 2015. This system is capable of monitoring compressed air system parameters on a continuous basis and transferring that information to a cloud server which can be accessed by Atlas Container personnel, Industrial Diagnostics and Sparks Dynamics. This information was collected into a database which can be exported to an Excel spreadsheet or displayed graphically using Sparks Dynamics ViewMaster Software. The average annual compressed air electricity expense was estimated to be approximately $116,000. This is based on an incremental $/KWh electric rate of $.091 per KWh and an estimated compressed air energy consumption of 1,279,200 KWH. The implementation phase of Energy Conservation Measures (ECMs) for the Compressed Air System included: • Identification and repair of compressed air leaks • Understanding of compressed air usage per manufacturing machine and installation of shut off valves when the machines are no longer in production mode • Identification of misapplications of compressed air to include blow offs, venturis, and cooling scenarios • Understand system pressure requirements and potential installation of point of use pressure regulation.