Download PDF
Standardizing Operational Knowledge for Barilla through IoT
Technology Category
- Functional Applications - Manufacturing Execution Systems (MES)
Applicable Industries
- Education
- Paper & Pulp
Applicable Functions
- Facility Management
- Quality Assurance
Use Cases
- Virtual Training
- Visual Quality Detection
Services
- Testing & Certification
- Training
The Challenge
Barilla, the world's largest pasta manufacturer, was facing challenges in capturing and distributing operational knowledge on the factory floor. The majority of their production facilities were still relying on paper work instructions, which were easy to damage, time-consuming to replace, and difficult to update. This traditional method of instruction also made it difficult to standardize procedures across different production sites, leading to inconsistencies in operations. Additionally, the company was losing valuable knowledge resources as experienced employees retired. The feedback process was complex, with frontline workers leaving notes on paper instructions to content creators. The need for a more efficient, digital solution was evident.
About The Customer
Barilla is the world's largest pasta manufacturer, known for its exceptional standards in production. The company operates numerous production facilities worldwide, each with its own set of operational procedures. Barilla's frontline workforce is actively involved in the creation of its standards, and they are often the subject matter experts. However, the company was facing challenges in capturing and distributing this operational knowledge, particularly as experienced employees retired. The need for a more efficient, digital solution to capture and distribute operational knowledge was evident.
The Solution
Barilla partnered with SwipeGuide to implement digital work instructions, revolutionizing the way they capture and distribute operational knowledge. This digital framework allowed for the distribution and improvement of operational knowledge with a bottom-up approach. The most up-to-date and approved version of each work instruction was made available on smartphones, tablets, and wearables within the production facility. Frontline teams were able to deliver critical feedback, process improvements, and other key insights directly into the SwipeGuide platform, empowering continuous improvement. The digital instructions also improved product quality by ensuring tasks were done more quickly and accurately. The solution also facilitated more efficient onboarding, training, and retraining, improving knowledge retention. SwipeGuide's mobile delivery and intuitive, visual design ensured successful adoption and retention among users of all ages.
Operational Impact
Quantitative Benefit
Related Case Studies.
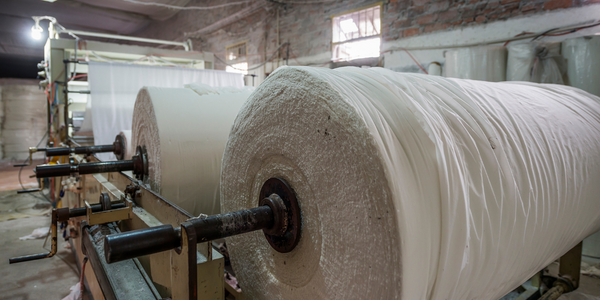
Case Study
Wireless Improves Efficiency in Compressed Air Systems
Hollingsworth and Vose wanted to improve the efficiency of their compressed air system, lower the electricity expense component of manufacturing cost in their commodity industry, and conserve energy leading to lowered greenhouse gas emissions. Compressed air systems degrade over time and become leaky and inefficient. Hollingsworth and Vose wanted to increase the frequency of system inspections without paying the high cost of manual labor.
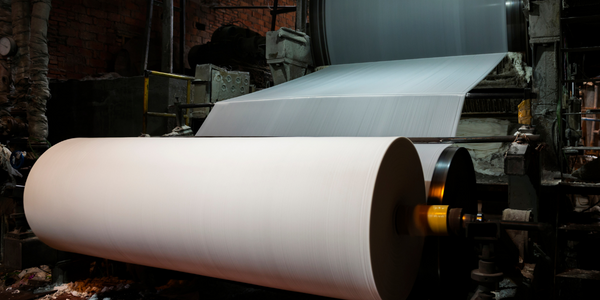
Case Study
Process Predictive Analysis in Pulp and Paper Mill
Common paper breaks consequently lead up to 60 minutes of downtime, delaying a potential $10K per hour of production value process. Thus, defective products cause financial and damage company's reputation. Improving quality and reducing defect rates can generate millions of dollars of revenue per year for your company.
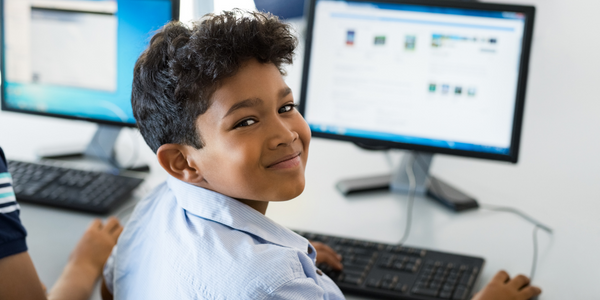
Case Study
IoT platform Enables Safety Solutions for U.S. School Districts
Designed to alert drivers when schoolchildren are present, especially in low-visibility conditions, school-zone flasher signals are typically updated manually at each school. The switching is based on the school calendar and manually changed when an unexpected early dismissal occurs, as in the case of a weather-event altering the normal schedule. The process to reprogram the flashers requires a significant effort by school district personnel to implement due to the large number of warning flashers installed across an entire school district.
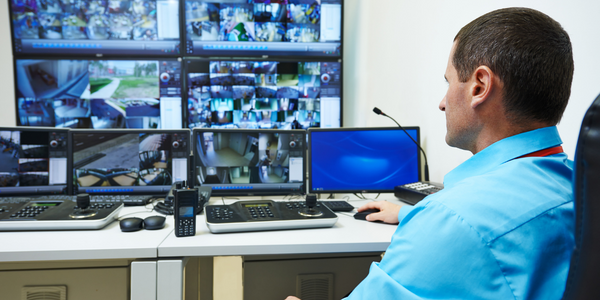
Case Study
Industrial Video Monitoring for Security and Regulatory Compliance
Because of the Stevenson mill’s proximity to the Tennessee River, WestRock was required by the USCG to comply with the Maritime Security 33CFR (MARSEC) regulations. WestRock needed a video security system but wanted to add other applications not required by the government, such as video process monitoring, condition monitoring, and wireless network management. WestRock needed a reliable video solution to avoid the compliance fines and possible security risks – but the solution needed to be implemented in the most cost-effective manner possible.
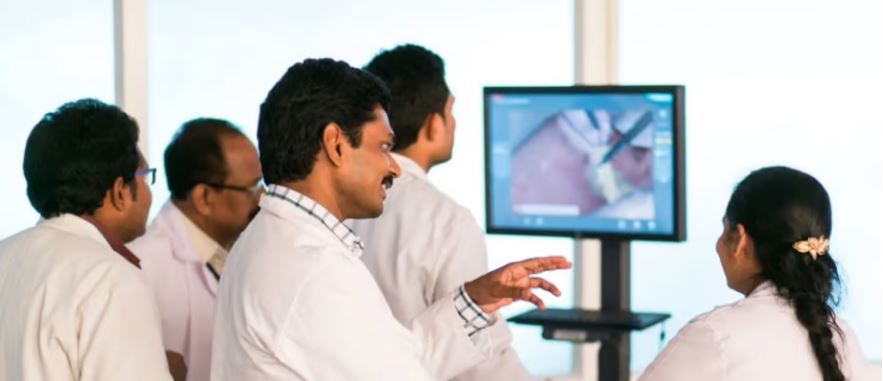
Case Study
Revolutionizing Medical Training in India: GSL Smart Lab and the LAP Mentor
The GSL SMART Lab, a collective effort of the GSL College of Medicine and the GSL College of Nursing and Health Science, was facing a challenge in providing superior training to healthcare professionals. As clinical medicine was becoming more focused on patient safety and quality of care, the need for medical simulation to bridge the educational gap between the classroom and the clinical environment was becoming increasingly apparent. Dr. Sandeep Ganni, the director of the GSL SMART Lab, envisioned a world-class surgical and medical training center where physicians and healthcare professionals could learn skills through simulation training. He was looking for different simulators for different specialties to provide both basic and advanced simulation training. For laparoscopic surgery, he was interested in a high fidelity simulator that could provide basic surgical and suturing skills training for international accreditation as well as specific hands-on training in complex laparoscopic procedures for practicing physicians in India.