Download PDF
Steelcase Inc. Reduces Paint Millage Variation with STATISTICA Enterprise-wide SPC System (SEWSS)
Technology Category
- Analytics & Modeling - Predictive Analytics
- Analytics & Modeling - Real Time Analytics
- Functional Applications - Manufacturing Execution Systems (MES)
Applicable Functions
- Process Manufacturing
- Quality Assurance
Use Cases
- Manufacturing System Automation
- Predictive Quality Analytics
- Process Control & Optimization
Services
- Software Design & Engineering Services
- System Integration
- Training
The Challenge
This project began by evaluating the state of three existing paint lines, two powder coat operations and a liquid line, which are used to apply paint from a widely varying palette of colors to the Office Systems. Steelcase customers require that millage be enough to provide sufficient coverage of the systems. Traditionally, reports on the paint millage had summarized the performance of these lines with the average of the paint thickness, and the variation in this process was not largely considered. As such, using the prior SPC and monitoring tools, the average millage was consistently within customer specifications. However, commonly more paint was applied than necessary to satisfy customer requirements, at significant material expense to Steelcase.
About The Customer
Steelcase Inc. helps individuals and organizations around the world work more effectively by providing knowledge, products, and services that enable customers and their consultants to create work environments that harmoniously integrate architecture, furniture, and technology. Founded in Grand Rapids, Michigan, in 1912, the company has led the office furniture industry in sales every year since 1974. Its product portfolio includes interior architectural products, furniture systems, technology products, seating, lighting, storage, and related products and services. Steelcase engineers and quality professionals are charged with designing and maintaining processes, with the objective of producing consistently conforming equipment that meets customer requirements, while at the same time minimizing the associated costs. Since 1999, Steelcase Inc. plants have been introducing new technology to their production facilities, with dramatic success stories, both in the short-term and the long-term, and to the benefit of both Steelcase Inc., from a business perspective, and their customers, from a product quality perspective. Steelcase currently implements Lean Manufacturing, also called the Steelcase Production System (SPS), where a flow-manufacturing environment.
The Solution
A team was created for the purpose of improving the paint process across these three lines. Specifically, the objective was to lower the average millage, and more importantly, to reduce the variation in the application of paint for the five most commonly used paint colors. The team consisted of the paint superintendent, finishing tech engineer, and quality assurance. They used a technique called Process Qualification, a standardized method developed by Steelcase, to evaluate their processes and products and to “qualify” their processes. The team used the Data Collection and Database Management tools provided by SEWSS to collect and store the data; they then used the Statistical and Graphical Data Analysis tools of STATISTICA to learn from the data that they collected, and to better understand the sources of variation in their process. Specifically, analysis tools such as Analysis of Variance and Box-and-Whisker Plots were used to identify sources of variation caused by inconsistencies in the process, and the team was able to use this information to introduce major process improvements.
Operational Impact
Quantitative Benefit
Related Case Studies.
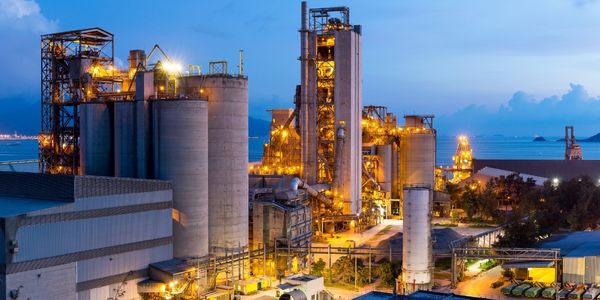
Case Study
System 800xA at Indian Cement Plants
Chettinad Cement recognized that further efficiencies could be achieved in its cement manufacturing process. It looked to investing in comprehensive operational and control technologies to manage and derive productivity and energy efficiency gains from the assets on Line 2, their second plant in India.
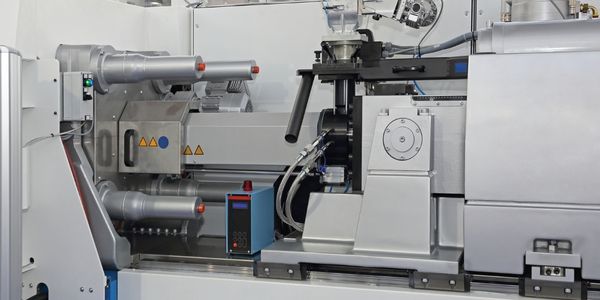
Case Study
Plastic Spoons Case study: Injection Moulding
In order to meet customer expectations by supplying a wide variety of packaging units, from 36 to 1000 spoons per package, a new production and packaging line needed to be built. DeSter wanted to achieve higher production capacity, lower cycle time and a high degree of operator friendliness with this new production line.
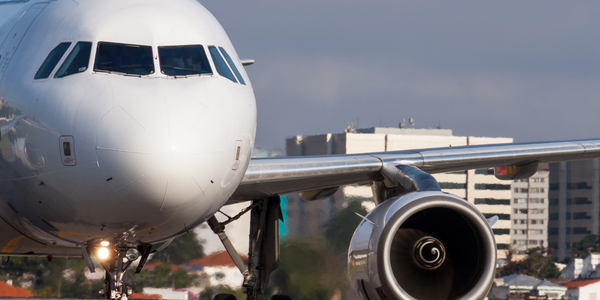
Case Study
Airbus Soars with Wearable Technology
Building an Airbus aircraft involves complex manufacturing processes consisting of thousands of moving parts. Speed and accuracy are critical to business and competitive advantage. Improvements in both would have high impact on Airbus’ bottom line. Airbus wanted to help operators reduce the complexity of assembling cabin seats and decrease the time required to complete this task.
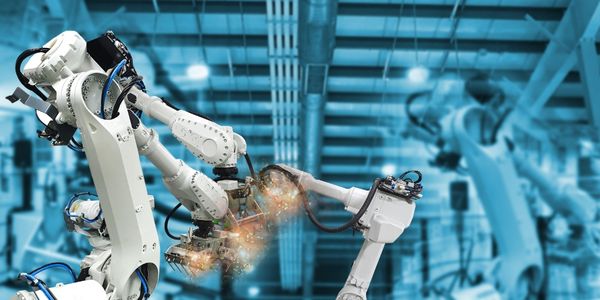
Case Study
Robot Saves Money and Time for US Custom Molding Company
Injection Technology (Itech) is a custom molder for a variety of clients that require precision plastic parts for such products as electric meter covers, dental appliance cases and spools. With 95 employees operating 23 molding machines in a 30,000 square foot plant, Itech wanted to reduce man hours and increase efficiency.
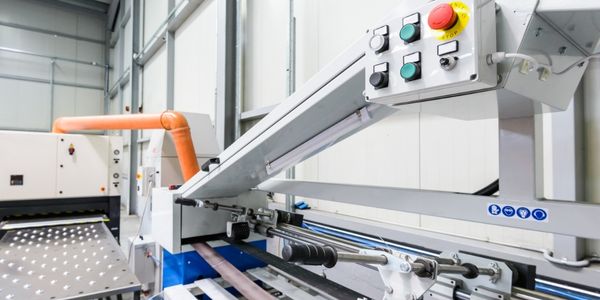
Case Study
Fully Automated Visual Inspection System
Tofflon has developed a fully automatic machine that uses light to inspect vials, medicine bottles, or infusion containers for glass fragments, aluminum particles, rubber grains, hairs, fibers, or other contaminants. It also detects damaged containers with cracks or inclusions (microscopic imperfections), automatically removing faulty or contaminated products. In order to cover all production processes for freeze-dried pharmaceuticals, Tofflon needed to create an open, consistent, and module-based automation concept.