Download PDF
Streamlined Design for Improved Engine Performance by KTM Technologies GmbH
Technology Category
- Analytics & Modeling - Digital Twin / Simulation
- Functional Applications - Manufacturing Execution Systems (MES)
Applicable Industries
- Automotive
- Electronics
Applicable Functions
- Product Research & Development
Use Cases
- Manufacturing Process Simulation
- Transportation Simulation
The Challenge
KTM Technologies GmbH, a division of PIERER Mobility AG, was tasked with the challenge of improving the engine performance of the KTM 450 Factory Edition motorcycle. The specific goal was to expand the rpm range of the engine by designing a new type of rocker arm with lower inertia while maintaining or improving stiffness and deformation level. The challenge was to reduce the mass inertias of the moving masses to a minimum while meeting the component’s stiffness targets. This would allow the rpm to be maximized without leading to higher forces on the component, ensuring the part's durability performance. The structure and optimization group at KTM Technologies, which focuses on structural optimization of parts for various manufacturing methods, was given the responsibility of redesigning the rocker arm.
About The Customer
KTM Technologies GmbH is a division of PIERER Mobility AG. The company has its main competences in the field of automotive, sports, general machinery, medical, and smart consumer applications. KTM Technologies focuses on concept and product development in lightweight design, composites, and electrics and electronics. Their simulation division employs static and dynamic structure simulation, computational fluid dynamics (CFD), manufacturing simulation, e-motor, and operating range simulation along with optimization. The structure and optimization group is primarily focused on structural optimization of parts for various manufacturing methods such as composite, forging or casting components, durability analysis, and multi-scale modeling of additively manufactured lattice structures.
The Solution
KTM Technologies used Altair HyperWorks™ to structurally optimize the design of the rocker arm while taking manufacturing constraints into account. They used Altair HyperMesh™ for preprocessing tasks, Altair OptiStruct™ for topology optimization and nonlinear finite element analysis, and Altair HyperView™ for postprocessing tasks. The team first defined the design space for the new geometry, applied forces on the component, and included other boundary conditions. They also added manufacturing constraints for forging to the model. Using OptiStruct, they conducted a topology optimization to define the ideal geometry of the redesigned part. The engineers then evaluated the deformation, contact pressure, static stress, durability, and the new mass in comparison to the existing design. The newly defined optimized geometry of the component led to a much more compact and more mass centering design, where the lower section became stronger.
Operational Impact
Quantitative Benefit
Related Case Studies.
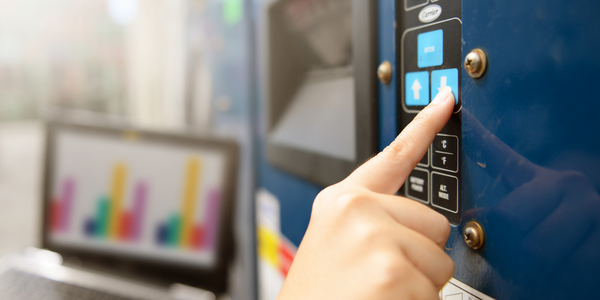
Case Study
Remote Temperature Monitoring of Perishable Goods Saves Money
RMONI was facing temperature monitoring challenges in a cold chain business. A cold chain must be established and maintained to ensure goods have been properly refrigerated during every step of the process, making temperature monitoring a critical business function. Manual registration practice can be very costly, labor intensive and prone to mistakes.
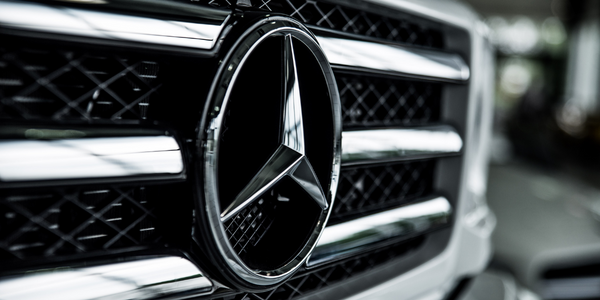
Case Study
Integral Plant Maintenance
Mercedes-Benz and his partner GAZ chose Siemens to be its maintenance partner at a new engine plant in Yaroslavl, Russia. The new plant offers a capacity to manufacture diesel engines for the Russian market, for locally produced Sprinter Classic. In addition to engines for the local market, the Yaroslavl plant will also produce spare parts. Mercedes-Benz Russia and his partner needed a service partner in order to ensure the operation of these lines in a maintenance partnership arrangement. The challenges included coordinating the entire maintenance management operation, in particular inspections, corrective and predictive maintenance activities, and the optimizing spare parts management. Siemens developed a customized maintenance solution that includes all electronic and mechanical maintenance activities (Integral Plant Maintenance).