Download PDF
SuperFrio Optimizes Its Cold Chain Logistics with Blue Yonder
Technology Category
- Functional Applications - Warehouse Management Systems (WMS)
Applicable Functions
- Warehouse & Inventory Management
Use Cases
- Inventory Management
- Warehouse Automation
Services
- Cloud Planning, Design & Implementation Services
- System Integration
The Challenge
SuperFrio, South America’s leader in refrigerated logistics, operates 22 distribution centers across Brazil and has five more under construction. To support its ambitious growth plans, the company decided to replace its legacy warehouse software and manual processes with a new level of speed and automation. The aim was to standardize processes and improve quality, accuracy, efficiency, and customer responsiveness. SuperFrio's warehouse operations are complex, with 10,000 stored SKUs, 300,000 pallet positions, and 15,000 vehicles dispatched monthly across 22 distribution centers.
About The Customer
SuperFrio is South America’s leader in refrigerated logistics. The company operates 22 distribution centers across Brazil and has five more under construction. SuperFrio's warehouse operations are complex, with 10,000 stored SKUs, 300,000 pallet positions, and 15,000 vehicles dispatched monthly across 22 distribution centers. The company has ambitious growth plans and aims to standardize processes and improve quality, accuracy, efficiency, and customer responsiveness.
The Solution
SuperFrio began implementing Blue Yonder’s warehouse management solution in select distribution centers in 2018. The solution is a comprehensive, highly scalable, real-time software-as-a-service (SaaS) solution that comprehensively optimizes SuperFrio’s task management, labor productivity, and inventory movements. The warehouse management capabilities from Blue Yonder enable a digital environment and optimize every operations step to ensure accuracy, efficiency, compliance, and desired customer service levels. Blue Yonder supports faster time-to-value with implementation templates, simplified process changes, better onboarding, and quick implementations. SuperFrio’s business needs are continuously met, without the customizations that make software upgrades painful and costly.
Operational Impact
Quantitative Benefit
Related Case Studies.
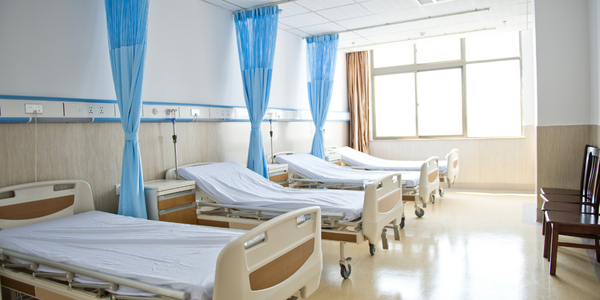
Case Study
Hospital Inventory Management
The hospital supply chain team is responsible for ensuring that the right medical supplies are readily available to clinicians when and where needed, and to do so in the most efficient manner possible. However, many of the systems and processes in use at the cancer center for supply chain management were not best suited to support these goals. Barcoding technology, a commonly used method for inventory management of medical supplies, is labor intensive, time consuming, does not provide real-time visibility into inventory levels and can be prone to error. Consequently, the lack of accurate and real-time visibility into inventory levels across multiple supply rooms in multiple hospital facilities creates additional inefficiency in the system causing over-ordering, hoarding, and wasted supplies. Other sources of waste and cost were also identified as candidates for improvement. Existing systems and processes did not provide adequate security for high-cost inventory within the hospital, which was another driver of cost. A lack of visibility into expiration dates for supplies resulted in supplies being wasted due to past expiry dates. Storage of supplies was also a key consideration given the location of the cancer center’s facilities in a dense urban setting, where space is always at a premium. In order to address the challenges outlined above, the hospital sought a solution that would provide real-time inventory information with high levels of accuracy, reduce the level of manual effort required and enable data driven decision making to ensure that the right supplies were readily available to clinicians in the right location at the right time.

Case Study
IoT Solution for Cold Chain
Most of the customer's warehouses run on utility and generator power. Since these warehouses are in remote locations, power outages are a very common scenario. Diesel fuel, thereby, becomes a significant cost for these warehouses. Energy consumption was also very high due to the lack of a consistent temperature throughout the facility. This lack of a consistent temperature in all areas and no way to control it, resulted in the customer losing a significant amount of their temperature sensitive goods due to spoilage.
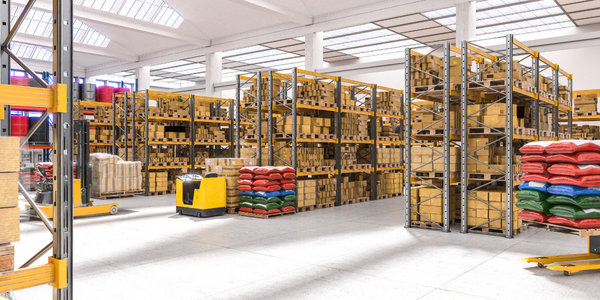
Case Study
Hardware Retailer Uses Data Warehouse to Track Inventory
Ace tracked which products retailers ordered, when they were ordered and shipped. However, the company could not track or forecast actual sales. Data used for reporting was up to a one-week old, owing to performance and data cleansing issues. Requirement to integrate wholesale and inventory data with POS data to help drive key business decisions, improve category management, lower inventory costs and optimize pricing. Reliance on custom coding to integrate POS data was excessively resource intensive and led to major performance constraints.
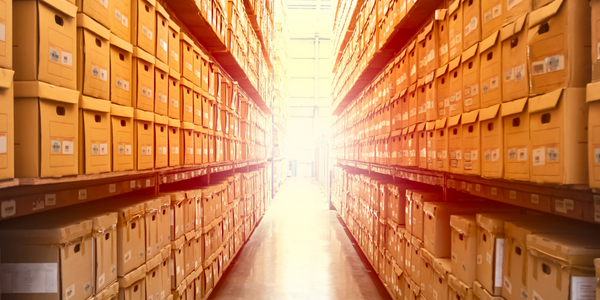
Case Study
DSV Road levels their workflow and decreases stress thanks to 4 BT Autopilots
During peaks in the workflow employeescan experience stress which makes them prone to causing damage. Avoiding these peaks also eliminates the need to hire temporary workers that require extra time and costs for education.