Download PDF
SYSPRO Case Study: Tom Barrow Company Streamlines Operations and Enhances Efficiencies with SYSPRO ERP
Technology Category
- Functional Applications - Enterprise Resource Planning Systems (ERP)
- Functional Applications - Manufacturing Execution Systems (MES)
Applicable Functions
- Business Operation
- Warehouse & Inventory Management
Use Cases
- Inventory Management
- Predictive Replenishment
- Process Control & Optimization
Services
- System Integration
- Training
The Challenge
The company was conducting all work via the processing of paper. Approximately 6,000 orders per month were manually converted into invoices, an extremely time-consuming and error-prone process. To facilitate order processing and inventory management as well as enhance customer service, the Tom Barrow Company deemed it advisable to computerize its operations in 1996. The company faced several challenges including no manufacturing system in place, lack of visibility into inventory, manual reporting resulting in duplication of work and errors, and managing multiple locations.
About The Customer
Tom Barrow Company was founded in Atlanta, Georgia in 1955. Initially, the company had only a few product lines but quickly earned a reputation for service and integrity. Over the years, the company expanded its product offerings and added more sales and support staff. By 1965, the company had expanded to a new territory with an office in Jacksonville, Florida, and continued to add several branch offices over the next four decades. By the 1990s, the company began representing applied equipment products, including custom air handling units and a variety of specialty products. Today, Tom Barrow Company is the largest commercial HVAC rep in the Southeast, with offices in Tennessee, Georgia, and Florida, serving customers from 10 offices.
The Solution
After an extensive software search, the company selected SYSPRO software based on its ability to tailor the solution to meet desired functionalities, as well as the availability of extensive training and support. Each of the company’s locations was brought online, giving management instant access to the status of jobs at each site and inventory levels at each location. SYSPRO ERP enabled the company to automate operations, including the processing of forms and the mailing of invoices. Management could get an immediate and updated picture of the location and status of every job, with data available with just a few clicks. The SYSPRO MRP and Forecasting modules significantly reduced inventory holdings. The ability to tailor functions within SYSPRO, including the customization of screens, simplified complex order processing and eliminated errors in producing invoices. The accessibility of SYSPRO support and the ease of implementing software upgrades were also highly appreciated.
Operational Impact
Quantitative Benefit
Related Case Studies.
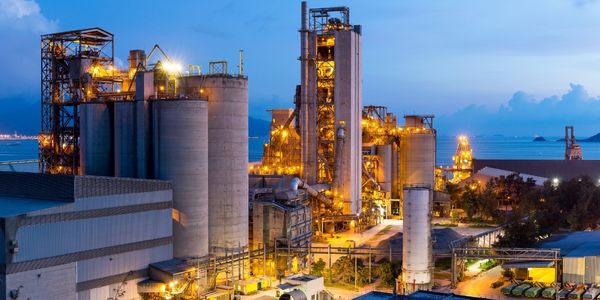
Case Study
System 800xA at Indian Cement Plants
Chettinad Cement recognized that further efficiencies could be achieved in its cement manufacturing process. It looked to investing in comprehensive operational and control technologies to manage and derive productivity and energy efficiency gains from the assets on Line 2, their second plant in India.
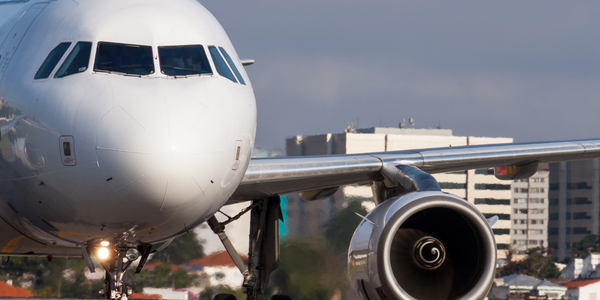
Case Study
Airbus Soars with Wearable Technology
Building an Airbus aircraft involves complex manufacturing processes consisting of thousands of moving parts. Speed and accuracy are critical to business and competitive advantage. Improvements in both would have high impact on Airbus’ bottom line. Airbus wanted to help operators reduce the complexity of assembling cabin seats and decrease the time required to complete this task.
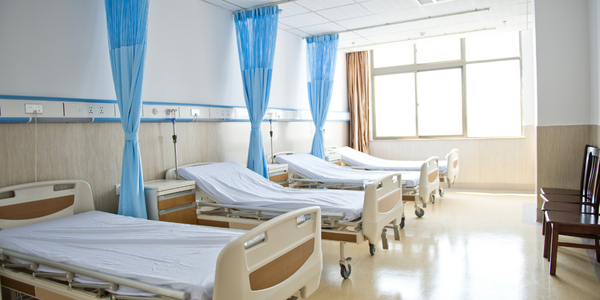
Case Study
Hospital Inventory Management
The hospital supply chain team is responsible for ensuring that the right medical supplies are readily available to clinicians when and where needed, and to do so in the most efficient manner possible. However, many of the systems and processes in use at the cancer center for supply chain management were not best suited to support these goals. Barcoding technology, a commonly used method for inventory management of medical supplies, is labor intensive, time consuming, does not provide real-time visibility into inventory levels and can be prone to error. Consequently, the lack of accurate and real-time visibility into inventory levels across multiple supply rooms in multiple hospital facilities creates additional inefficiency in the system causing over-ordering, hoarding, and wasted supplies. Other sources of waste and cost were also identified as candidates for improvement. Existing systems and processes did not provide adequate security for high-cost inventory within the hospital, which was another driver of cost. A lack of visibility into expiration dates for supplies resulted in supplies being wasted due to past expiry dates. Storage of supplies was also a key consideration given the location of the cancer center’s facilities in a dense urban setting, where space is always at a premium. In order to address the challenges outlined above, the hospital sought a solution that would provide real-time inventory information with high levels of accuracy, reduce the level of manual effort required and enable data driven decision making to ensure that the right supplies were readily available to clinicians in the right location at the right time.
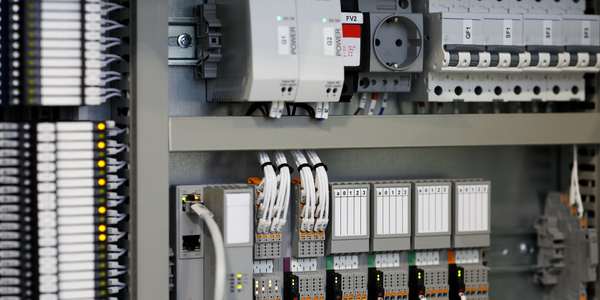
Case Study
Improving Production Line Efficiency with Ethernet Micro RTU Controller
Moxa was asked to provide a connectivity solution for one of the world's leading cosmetics companies. This multinational corporation, with retail presence in 130 countries, 23 global braches, and over 66,000 employees, sought to improve the efficiency of their production process by migrating from manual monitoring to an automatic productivity monitoring system. The production line was being monitored by ABB Real-TPI, a factory information system that offers data collection and analysis to improve plant efficiency. Due to software limitations, the customer needed an OPC server and a corresponding I/O solution to collect data from additional sensor devices for the Real-TPI system. The goal is to enable the factory information system to more thoroughly collect data from every corner of the production line. This will improve its ability to measure Overall Equipment Effectiveness (OEE) and translate into increased production efficiencies. System Requirements • Instant status updates while still consuming minimal bandwidth to relieve strain on limited factory networks • Interoperable with ABB Real-TPI • Small form factor appropriate for deployment where space is scarce • Remote software management and configuration to simplify operations