Download PDF
SYSPRO Case Study
Technology Category
- Functional Applications - Computerized Maintenance Management Systems (CMMS)
- Functional Applications - Enterprise Resource Planning Systems (ERP)
- Functional Applications - Product Lifecycle Management Systems (PLM)
Applicable Industries
- Consumer Goods
- Pharmaceuticals
Applicable Functions
- Business Operation
- Quality Assurance
- Warehouse & Inventory Management
Use Cases
- Inventory Management
- Predictive Maintenance
- Process Control & Optimization
- Regulatory Compliance Monitoring
Services
- Software Design & Engineering Services
- System Integration
- Training
The Challenge
When Pharma Tech bought the Royston plant from Johnson & Johnson, the decision was quickly made to look for new software. Since historically the Royston plant was a J&J facility, it had been utilizing the current J&J software. However, the change in ownership prompted the need for a replacement ERP system, one that could accommodate the needs of a smaller, tighter business while helping the company achieve compliance with strict FDA requirements. Time was not a luxury Pharma Tech could afford during such a major transition. Pharma Tech is registered with the FDA for the production of Food, Drug and Medical Device products, and as such has established a Good Manufacturing Practices program that includes a mandatory Lot Traceability visibility. When the time came for a new ERP software, that was a primary consideration.
About The Customer
Since they opened the original plant in Union, MO, in 1972, Pharma Tech has been providing full-service contract manufacturing and packaging services to the pharmaceutical industry, specifically producing over-the-counter drugs. In 2005, however, the company added the Royston plant – and a cosmetics division – to the business, more than doubling the company’s size and tripling their square-footage. Most notably, they took over production of the world’s supply of Johnson & Johnson’s Baby Powder. Pharma Tech provides various client services, from blending, milling, screening and classifying, to repackaging of bulk intermediates. Pharma Tech provides these services to both raw material suppliers and pharmaceutical manufacturers. Between the two facilities the company today employs over 250 people. Explains Pharma Tech President, Carl Oberg, “Our Union plant produces over the-counter pharmaceuticals. Our Royston plant produces cosmetics. However, both must comply with FDA regulations and undergo periodic inspections by that body. Since Johnson’s Baby Powder is considered a ‘pharmaceutical,’ there is a high level of comfort and confidence in having the powder produced in Pharma Tech’s FDA controlled environment.”
The Solution
Pharma Tech selected the SYSPRO ERP solution for its long history with and dedication to the manufacturing industry, for its user-friendly functionality, for its capability to facilitate FDA compliance and for the speed at which it could be implemented. Kristin Brown, Pharma Tech’s customer service and planning manager, says that, “The SYSPRO STARS implementation methodology was also important to us, since we were on a very tight time schedule for going live.” Brown’s confidence, it turns out, was fully justified when the SYSPRO implementation was accomplished in less than four months. The SYSPRO Lot Traceability module is of paramount importance to the compliance requirements embedded in Pharma Tech’s day-to-day operations. The company needs to be able to trace each and every item going into and out of its facilities. The SYSPRO module allows Pharma Tech not only to track those items but also to track the inspection progress involving them.
Operational Impact
Quantitative Benefit
Related Case Studies.
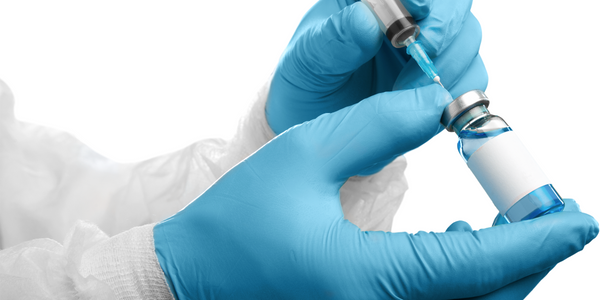
Case Study
Case Study: Pfizer
Pfizer’s high-performance computing software and systems for worldwide research and development support large-scale data analysis, research projects, clinical analytics, and modeling. Pfizer’s computing services are used across the spectrum of research and development efforts, from the deep biological understanding of disease to the design of safe, efficacious therapeutic agents.
.png)
Case Study
Improving Vending Machine Profitability with the Internet of Things (IoT)
The vending industry is undergoing a sea change, taking advantage of new technologies to go beyond just delivering snacks to creating a new retail location. Intelligent vending machines can be found in many public locations as well as company facilities, selling different types of goods and services, including even computer accessories, gold bars, tickets, and office supplies. With increasing sophistication, they may also provide time- and location-based data pertaining to sales, inventory, and customer preferences. But at the end of the day, vending machine operators know greater profitability is driven by higher sales and lower operating costs.
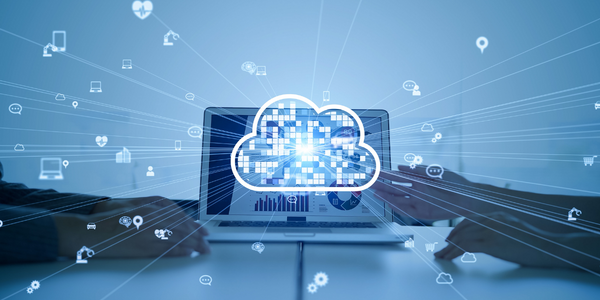
Case Study
Fusion Middleware Integration on Cloud for Pharma Major
Customer wanted a real-time, seamless, cloud based integration between the existing on premise and cloud based application using SOA technology on Oracle Fusion Middleware Platform, a Contingent Worker Solution to collect, track, manage and report information for on-boarding, maintenance and off-boarding of contingent workers using a streamlined and Integrated business process, and streamlining of integration to the back-end systems and multiple SaaS applications.
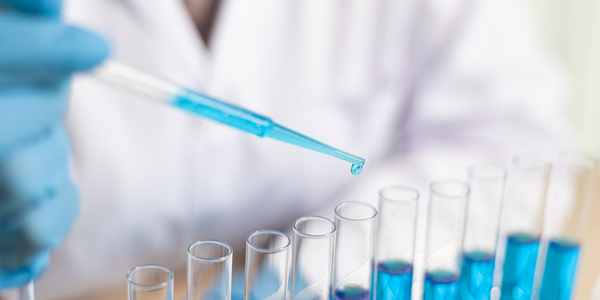
Case Study
Process Control System Support
In many automated production facilities, changes are made to SIMATIC PCS 7 projects on a daily basis, with individual processes often optimised by multiple workers due to shift changes. Documentation is key here, as this keeps workers informed about why a change was made. Furthermore, SIMATIC PCS 7 installations are generally used in locations where documentation is required for audits and certification. The ability to track changes between two software projects is not only an invaluable aid during shift changes, but also when searching for errors or optimising a PCS 7 installation. Every change made to the system is labour-intensive and time-consuming. Moreover, there is also the risk that errors may occur. If a change is saved in the project, then the old version is lost unless a backup copy was created in advance. If no backup was created, it will no longer be possible to return to the previous state if and when programming errors occur. Each backup denotes a version used by the SIMATIC PCS 7 system to operate an installation. To correctly interpret a version, information is required on WHO changed WHAT, WHERE, WHEN and WHY: - Who created the version/who is responsible for the version? - Who released the version? - What was changed in the version i.e. in which block or module of the SIMATIC PCS 7 installation were the changes made? - When was the version created? Is this the latest version or is there a more recent version? - Why were the changes made to the version? If they are part of a regular maintenance cycle, then is the aim to fix an error or to improve production processes? - Is this particular version also the version currently being used in production? The fact that SIMATIC PCS 7 projects use extremely large quantities of data complicates the situation even further, and it can take a long time to load and save information as a result. Without a sustainable strategy for operating a SIMATIC PCS 7 installation, searching for the right software version can become extremely time-consuming and the installation may run inefficiently as a result.
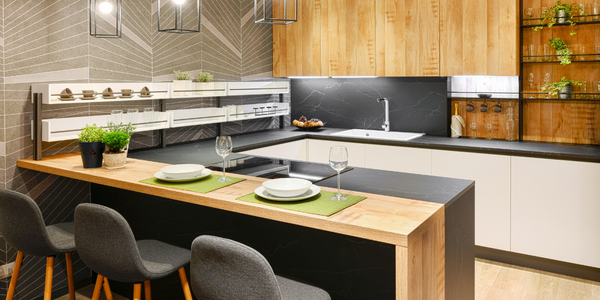
Case Study
Series Production with Lot-size-1 Flexibility
Nobilia manufactures customized fitted kitchens with a lot size of 1. They require maximum transparency of tracking design data and individual processing steps so that they can locate a particular piece of kitchen furniture in the sequence of processes.