Download PDF
Tackling Complex Problems in the Life Sciences Industry
Technology Category
- Analytics & Modeling - Predictive Analytics
- Functional Applications - Manufacturing Execution Systems (MES)
Applicable Industries
- Life Sciences
- Pharmaceuticals
Applicable Functions
- Process Manufacturing
- Quality Assurance
Use Cases
- Machine Condition Monitoring
- Predictive Quality Analytics
- Process Control & Optimization
Services
- Software Design & Engineering Services
- System Integration
The Challenge
EMD Millipore had been relying on post-production testing to control quality in pleated cartridge assembly. Under the previous system, the cartridges were bonded and then placed on carts. The carts would then be moved to a testing room where post-production quality inspection would occur. If they passed the inspection, the cartridges would be placed back on the carts and moved to a drying area where they would dry before they could be packaged. This approach was costing EMD Millipore a great deal of time. They were looking for a way to perform the quality tests during production so the cartridges wouldn’t need to be removed from the line. In-process testing would prevent quality issues from occurring, and would reduce the number of defects found during post-production. An ideal system would demonstrate that the bonded parameters were in statistical control and specification in a highly automated production environment—so the post-production testing and the associated handling could be eliminated.
About The Customer
EMD Millipore is a Life Science leader providing cutting-edge technologies, tools, and services for bioscience research and biopharmaceutical manufacturing. As a strategic partner, EMD Millipore collaborates with customers to confront the world’s challenging human health issues. From research through development to production, EMD Millipore’s scientific expertise and innovative solutions help customers tackle their most complex problems and achieve their goals.
The Solution
EMD Millipore chose to implement InfinityQS® ProFicient™ after an on-site demonstration of the industry-leading SPC software. The automated tools and the powerful SPC charting capabilities stood out as key differentiators in the decision-making process. After the demonstration, EMD Millipore knew it could gain an immediate ROI on the software. InfinityQS’ real-time system enabled EMD Millipore to test cartridge bonding attributes during production and include the lot report as part of the batch record. InfinityQS’ real-time data analysis provided intelligence that allowed for the elimination of the postproduction quality test in cartridge assembly. In cartridge assembly, EMD Millipore is achieving savings from the elimination of the test and reductions in scrap, rework, labor, and production overhead that total over $250,000 annually. Along with the quality improvements, EMD Millipore was also able to leverage InfinityQS’ “lights out” tools to streamline their highly automated work cells, where operators are not always present while processes run. It is critical that operators, present or not, take action when a process begins to drift out of statistical control. InfinityQS’ Remote Event Monitoring Service (REMS) monitors EMD Millipore’s automated processes and shuts down the process if an out-of-control condition occurs.
Operational Impact
Quantitative Benefit
Related Case Studies.
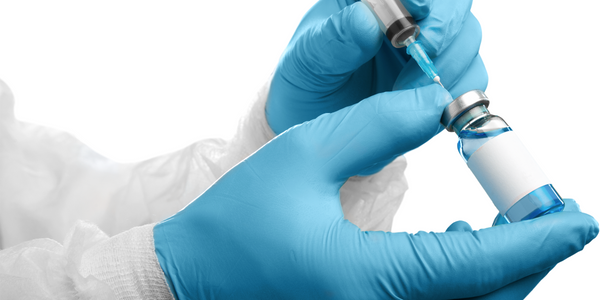
Case Study
Case Study: Pfizer
Pfizer’s high-performance computing software and systems for worldwide research and development support large-scale data analysis, research projects, clinical analytics, and modeling. Pfizer’s computing services are used across the spectrum of research and development efforts, from the deep biological understanding of disease to the design of safe, efficacious therapeutic agents.
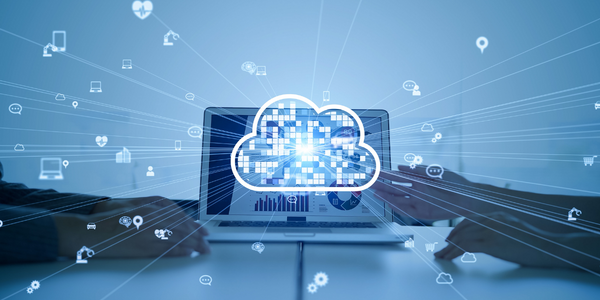
Case Study
Fusion Middleware Integration on Cloud for Pharma Major
Customer wanted a real-time, seamless, cloud based integration between the existing on premise and cloud based application using SOA technology on Oracle Fusion Middleware Platform, a Contingent Worker Solution to collect, track, manage and report information for on-boarding, maintenance and off-boarding of contingent workers using a streamlined and Integrated business process, and streamlining of integration to the back-end systems and multiple SaaS applications.
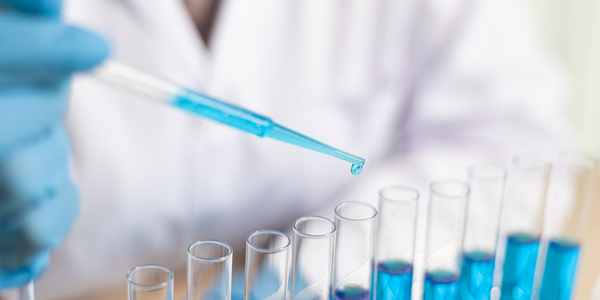
Case Study
Process Control System Support
In many automated production facilities, changes are made to SIMATIC PCS 7 projects on a daily basis, with individual processes often optimised by multiple workers due to shift changes. Documentation is key here, as this keeps workers informed about why a change was made. Furthermore, SIMATIC PCS 7 installations are generally used in locations where documentation is required for audits and certification. The ability to track changes between two software projects is not only an invaluable aid during shift changes, but also when searching for errors or optimising a PCS 7 installation. Every change made to the system is labour-intensive and time-consuming. Moreover, there is also the risk that errors may occur. If a change is saved in the project, then the old version is lost unless a backup copy was created in advance. If no backup was created, it will no longer be possible to return to the previous state if and when programming errors occur. Each backup denotes a version used by the SIMATIC PCS 7 system to operate an installation. To correctly interpret a version, information is required on WHO changed WHAT, WHERE, WHEN and WHY: - Who created the version/who is responsible for the version? - Who released the version? - What was changed in the version i.e. in which block or module of the SIMATIC PCS 7 installation were the changes made? - When was the version created? Is this the latest version or is there a more recent version? - Why were the changes made to the version? If they are part of a regular maintenance cycle, then is the aim to fix an error or to improve production processes? - Is this particular version also the version currently being used in production? The fact that SIMATIC PCS 7 projects use extremely large quantities of data complicates the situation even further, and it can take a long time to load and save information as a result. Without a sustainable strategy for operating a SIMATIC PCS 7 installation, searching for the right software version can become extremely time-consuming and the installation may run inefficiently as a result.
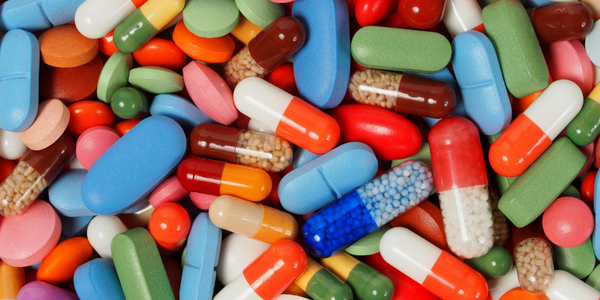
Case Study
Drug Maker Takes the Right Prescription
China Pharm decided to build a cloud-based platform to support the requirements of IT planning for the next five to ten years which includes a dynamic and scalable mail resource pool platform. The platform needed to have the following functions: all nodes support redundancy, ensuring service continuity and good user experience, simple and easy-to-use user interfaces for end users and administrators and good compatibility and supports smooth capacity expansion.
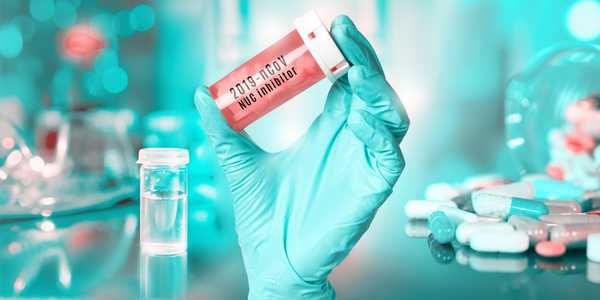
Case Study
ELI LILLY ADOPTS MICROMEDIA’S ALERT NOTIFICATION SYSTEM
Pharmaceutical production is subject to a strict set of enforced rules that must be adhered to and compliance to these standards is critically necessary. Due to the efforts of WIN 911’s strategic partner Micromedia, Lilly was able to adopt an alarm notification infrastructure that integrated smoothly with their existing workflows and emergency hardware and protocols. These raw energy sources enable the industrial process to function: electricity, WIN-911 Software | 4020 South Industrial Drive, Suite 120 | Austin, TX 78744 USA industrial steam, iced water, air mixtures of varying quality. Refrigeration towers, boilers and wastewater are monitored by ALERT. Eli Lilly identified 15000 potential variables, but limitations compelled them to chisel the variable list down to 300. This allowed all major alarms to be covered including pressure, discharge, quantity of waste water discharged,temperature, carbon dioxide content, oxygen & sulphur content, and the water’s pH.