Download PDF
Taking Merchandising Displays to A New Level with Solidworks Premium
Technology Category
- Functional Applications - Product Lifecycle Management Systems (PLM)
- Functional Applications - Manufacturing Execution Systems (MES)
- Analytics & Modeling - Predictive Analytics
Applicable Industries
- Retail
- Consumer Goods
Applicable Functions
- Product Research & Development
- Quality Assurance
Use Cases
- Predictive Maintenance
- Inventory Management
- Manufacturing System Automation
Services
- Software Design & Engineering Services
- System Integration
- Training
The Challenge
Boston Group, Inc. faced the challenge of streamlining the development and fabrication of merchandising display and power systems to compress lead times and accelerate product delivery to customers. The company needed to move from 2D to 3D design to better showcase product concepts to visually oriented merchandising professionals and to become more efficient in their development processes. Shortening delivery and lead times was essential for competing successfully in the market.
About The Customer
Boston Group, Inc. is a manufacturer of display, power, and protection products for retail merchandising display applications. Founded in 1937, the company provides innovative retail merchandising solutions, including eco-friendly impact protection, modular wiring technology, and powered and non-powered merchandising displays and raceways. Operating its own sheet metal fabrication and manufacturing facility, Boston Group has established itself as an industry leader through its commitment to innovative product development, focus on customer needs, and adherence to strict quality and cost controls.
The Solution
Boston Group implemented SOLIDWORKS Standard design and SOLIDWORKS Premium design and analysis software to address their challenges. The company chose SOLIDWORKS for its ease of use, integrated sheet metal design, structural analysis, and photorealistic rendering tools. The software enabled Boston Group to integrate sheet metal design and production, create realistic images of product concepts, and conduct basic load and strength of materials analyses, which helped eliminate prototyping in new product development. The use of SOLIDWORKS, along with the Solution Partner SheetWorks package and the company's combination laser punch/automated sheet metal forming machine, allowed Boston Group to create a direct bridge between design and production, eliminating the need for manual programming of fabrication machines.
Operational Impact
Quantitative Benefit
Related Case Studies.
.png)
Case Study
Improving Vending Machine Profitability with the Internet of Things (IoT)
The vending industry is undergoing a sea change, taking advantage of new technologies to go beyond just delivering snacks to creating a new retail location. Intelligent vending machines can be found in many public locations as well as company facilities, selling different types of goods and services, including even computer accessories, gold bars, tickets, and office supplies. With increasing sophistication, they may also provide time- and location-based data pertaining to sales, inventory, and customer preferences. But at the end of the day, vending machine operators know greater profitability is driven by higher sales and lower operating costs.
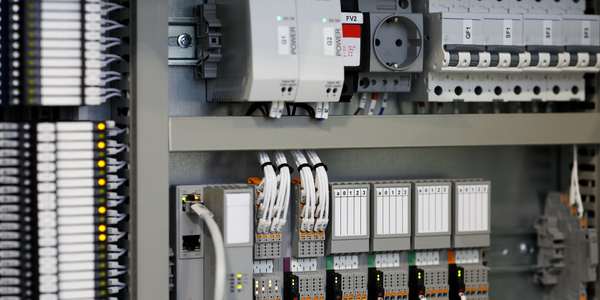
Case Study
Improving Production Line Efficiency with Ethernet Micro RTU Controller
Moxa was asked to provide a connectivity solution for one of the world's leading cosmetics companies. This multinational corporation, with retail presence in 130 countries, 23 global braches, and over 66,000 employees, sought to improve the efficiency of their production process by migrating from manual monitoring to an automatic productivity monitoring system. The production line was being monitored by ABB Real-TPI, a factory information system that offers data collection and analysis to improve plant efficiency. Due to software limitations, the customer needed an OPC server and a corresponding I/O solution to collect data from additional sensor devices for the Real-TPI system. The goal is to enable the factory information system to more thoroughly collect data from every corner of the production line. This will improve its ability to measure Overall Equipment Effectiveness (OEE) and translate into increased production efficiencies. System Requirements • Instant status updates while still consuming minimal bandwidth to relieve strain on limited factory networks • Interoperable with ABB Real-TPI • Small form factor appropriate for deployment where space is scarce • Remote software management and configuration to simplify operations
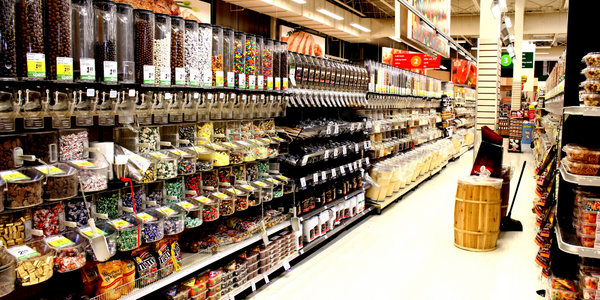
Case Study
How Sirqul’s IoT Platform is Crafting Carrefour’s New In-Store Experiences
Carrefour Taiwan’s goal is to be completely digital by end of 2018. Out-dated manual methods for analysis and assumptions limited Carrefour’s ability to change the customer experience and were void of real-time decision-making capabilities. Rather than relying solely on sales data, assumptions, and disparate systems, Carrefour Taiwan’s CEO led an initiative to find a connected IoT solution that could give the team the ability to make real-time changes and more informed decisions. Prior to implementing, Carrefour struggled to address their conversion rates and did not have the proper insights into the customer decision-making process nor how to make an immediate impact without losing customer confidence.
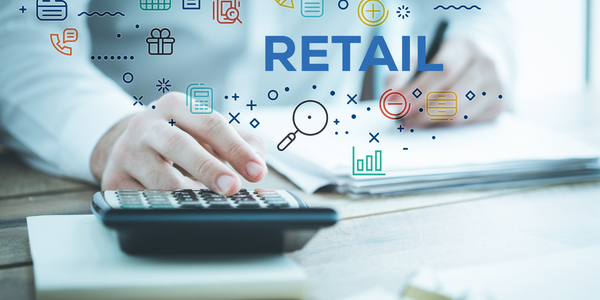
Case Study
Digital Retail Security Solutions
Sennco wanted to help its retail customers increase sales and profits by developing an innovative alarm system as opposed to conventional connected alarms that are permanently tethered to display products. These traditional security systems were cumbersome and intrusive to the customer shopping experience. Additionally, they provided no useful data or analytics.