Download PDF
Taking Ownership at Tek Pak with the Help of Made2Manage Shop Floor Manager
Technology Category
- Functional Applications - Enterprise Resource Planning Systems (ERP)
- Functional Applications - Manufacturing Execution Systems (MES)
Applicable Industries
- Plastics
Applicable Functions
- Discrete Manufacturing
- Quality Assurance
Use Cases
- Inventory Management
- Manufacturing System Automation
Services
- System Integration
The Challenge
Tek Pak, a manufacturer of packaging for the electronics industry, was struggling with its bar code data collection system for shop floor reporting and inventory. The system was not interactive and provided no feedback, leading to errors, missing and incomplete transactions, and a general disinterest among the workforce. The reporting was not reliable, and the data was often a day behind, making it of no real value. Material usage was logged only once per week by supervisors based on hand-written notes from operators, so material issues went generally unnoticed until it was too late. Inventory accuracy and visibility were lacking.
About The Customer
Tek Pak, Inc. is a manufacturer of packaging for the electronics industry and more. The company was founded in 1992 and has 78 employees. Tek Pak serves the electronics, healthcare, and consumer industries, offering custom thermoforming, prototyping, and tooling, as well as product development. The company has been a user of Made2Manage ERP since 1998. However, they struggled with errors, missing and incomplete transactions, and a general disinterest among the workforce due to the lack of interactivity and feedback from their bar code data collection system for shop floor reporting and inventory.
The Solution
Tek Pak decided to implement Made2Manage Shop Floor Manager (SFM), a shop floor execution system designed to complement Made2Manage, due to its interactive interface for the production floor and the fact that it allowed visibility into the current status of a job without having to constantly generate reports. Tek Pak set up SFM workstations on the plant floor for employees to clock on and off of jobs as well as enter material usage directly so that it was applied to the correct job. In addition, the SFM displays gave work station users access to corresponding job documents, such as drawings and work instructions, right at their fingertips. The system was accepted as easier to use than the bar code system and users were able to clearly see direct benefits.
Operational Impact
Quantitative Benefit
Related Case Studies.
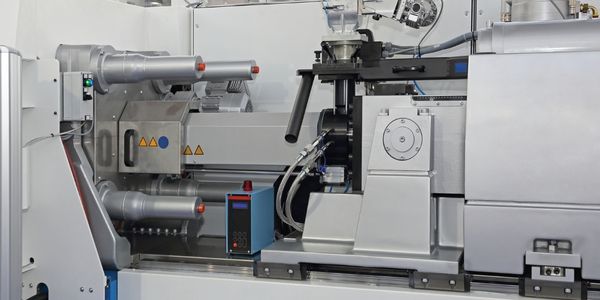
Case Study
Plastic Spoons Case study: Injection Moulding
In order to meet customer expectations by supplying a wide variety of packaging units, from 36 to 1000 spoons per package, a new production and packaging line needed to be built. DeSter wanted to achieve higher production capacity, lower cycle time and a high degree of operator friendliness with this new production line.
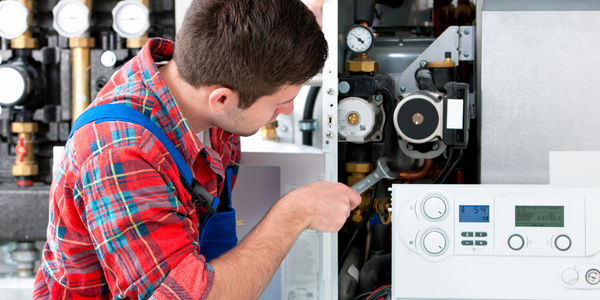
Case Study
Boiler Control System for Plastic Manufacturing Applications
Factory automation applications must be equipped to handle and monitor the myriads of information from attached devices. For plastic manufacturing applications, the boiler control system plays a critical role by gathering and regulating information to ensure production is accurate and smooth. In this particular case, the customer combines eight subsystems that include power meters, water meters, alarm output, displays, and I/O status to be controlled by several intelligent controllers with Modbus RTU interface. The Modbus TCP protocol is used for this application due to the distance. System Requirements: • Modbus serial to Modbus TCP translation • Multiple slaves/masters support • Automatic Modbus TCP response time detection
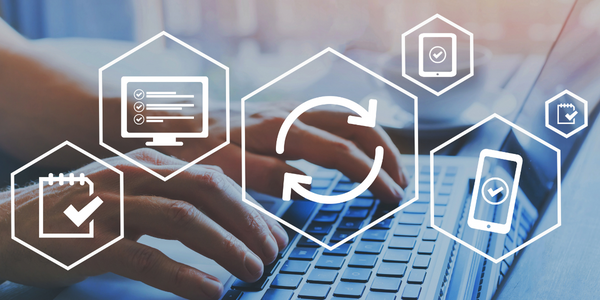
Case Study
Ascend Performance Materials Case Study
Ascend operations must access multiple software systems to manage day-to-day operations in an effective and secure manner. These systems generate large sets of data which contain critical information pertaining to management systems, planning and cost information in business systems and energy consumption. As a result, Ascend management was challenged with creating relevant reports reflecting performance measures in overall context of their operational process. The company’s previous process entailed collecting and analyzing data manually which was not effective, since the information collected was generated after the fact, and was too complex for collaborative use across the organization.
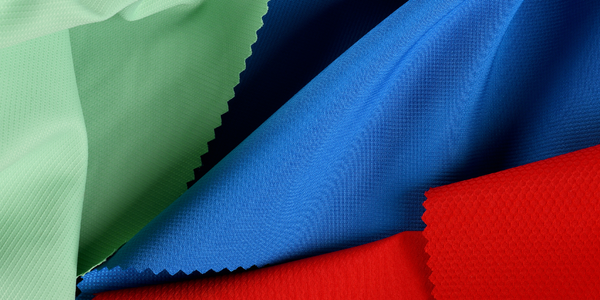
Case Study
Remake Enterprise-to-production System
The client was running a legacy material flow tracking system and wanted to replace the system with a more effective one as the system was increasingly expensive to maintain and support and also was not extendable. The client's IT landscape was filled with modern applications and it was difficult to interface the material flow tracking system with modern applications.