Download PDF
Technology Enabled High Performance Culture
Technology Category
- Analytics & Modeling - Predictive Analytics
- Application Infrastructure & Middleware - Data Visualization
- Functional Applications - Manufacturing Execution Systems (MES)
Applicable Industries
- Electronics
Applicable Functions
- Process Manufacturing
- Quality Assurance
Use Cases
- Machine Condition Monitoring
- Manufacturing System Automation
- Predictive Maintenance
Services
- Software Design & Engineering Services
- System Integration
The Challenge
A Vice President of Operations for a US-based electronics manufacturer found his team struggling to identify opportunities to improve their business. Turf wars were common, as were racks of components waiting for rework and retesting. Bright, motivated engineers worked independently to optimize their domain. In doing so, they competed with each other for resources, missed common problems that spanned their areas of responsibility, and were unable to prioritize the most important issues for the entire organization. The organization lacked timely, accurate, unbiased visibility into the performance of the entire manufacturing floor. The VP envisioned a single standard to aggregate, contextualize, analyze, and visualize manufacturing performance in real time.
About The Customer
Hertzler Systems has been a leader in manufacturing analytics and visualization software for over 30 years. Their software and services enable clients to connect, collect, analyze, and visualize data, building a data infrastructure for making data-driven decisions. These capabilities help clients improve throughput and yield, improve cycle times, reduce costs and errors, and increase profitability. Hertzler Systems serves a diverse customer base, including BAE Systems, Kiva Inc., ITW, Solo/Dart, McCormick & Company, Inc., Hormel Foods Corporation, Snyder's-Lance, Titleist & Footjoy, IDEX Corporation, and TaylorMade-Adidas Golf Worldwide.
The Solution
Hertzler Systems provided the single standard that the VP envisioned. This standard aggregated, contextualized, analyzed, and visualized manufacturing performance in real time. The solution enabled the team to have timely, accurate, and unbiased visibility into the performance of the entire manufacturing floor. This visibility allowed the team to identify and prioritize the most critical performance issues, reducing the competition for resources and enabling a more collaborative approach to problem-solving. The implementation of this standard significantly improved the organization's ability to focus on critical performance issues, leading to substantial improvements in their operations.
Operational Impact
Quantitative Benefit
Related Case Studies.
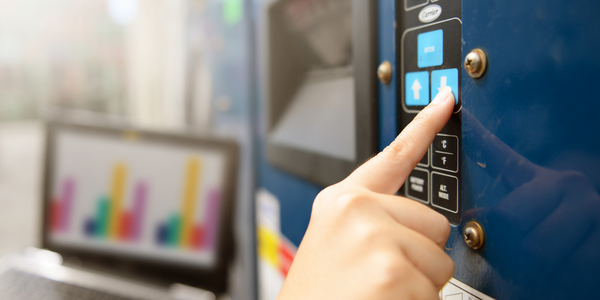
Case Study
Remote Temperature Monitoring of Perishable Goods Saves Money
RMONI was facing temperature monitoring challenges in a cold chain business. A cold chain must be established and maintained to ensure goods have been properly refrigerated during every step of the process, making temperature monitoring a critical business function. Manual registration practice can be very costly, labor intensive and prone to mistakes.
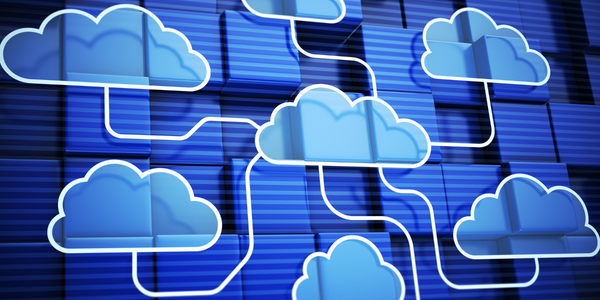
Case Study
Cloud Solution for Energy Management Platform-Schneider Electric
Schneider Electric required a cloud solution for its energy management platform to manage high computational operations, which were essential for catering to client requirements. As the business involves storage and analysis of huge amounts of data, the company also needed a convenient and scalable storage solution to facilitate operations efficiently.
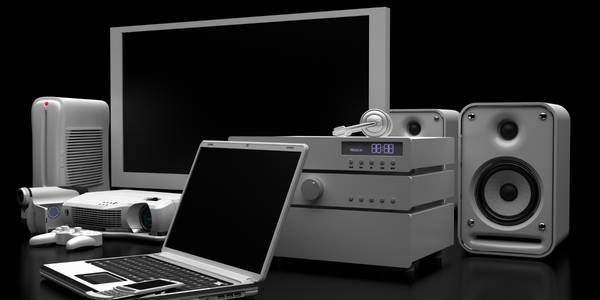
Case Study
Leveraging the IoT to Gain a Competitive Edge in International Competition
Many large manufacturers in and outside Japan are competing for larger market share in the same space, expecting a growing demand for projectors in the areas of entertainment, which requires glamor and strong visual performance as well as digital signage that can attract people’s attention. “It is becoming more and more difficult to differentiate ourselves with stand-alone hardware products,” says Kazuyuki Kitagawa, Director of Service & Support at Panasonic AVC Networks. “In order for Panasonic to grow market share and overall business, it is essential for us to develop solutions that deliver significant added value.” Panasonic believes projection failure and quality deterioration should never happen. This is what and has driven them to make their projectors IoT-enabled. More specifically, Panasonic has developed a system that collects data from projectors, visualizes detailed operational statuses, and predicts issues and address them before failure occurs. Their projectors are embedded with a variety of sensors that measure power supply, voltage, video input/ output signals, intake/exhaust air temperatures, cooling fan operations, and light bulb operating time. These sensors have been used to make the projector more intelligent, automatically suspending operation when the temperature rises excessively, and automatically switching light bulbs. Although this was a great first step, Panasonic projectors were still not equipped with any capability to send the data over a network.