Download PDF
The Sultan Center meets expansion and compliance objectives with Manhattan Associates’ solutions
Technology Category
- Analytics & Modeling - Predictive Analytics
- Functional Applications - Warehouse Management Systems (WMS)
Applicable Industries
- Food & Beverage
- Retail
Applicable Functions
- Logistics & Transportation
- Warehouse & Inventory Management
Use Cases
- Inventory Management
- Predictive Replenishment
- Supply Chain Visibility
Services
- System Integration
- Training
The Challenge
The Sultan Center faced the challenge of expanding its business while adhering to rigorous health ministry requirements for imported foods. The legacy system in place was inadequate for managing these complex requirements and supporting the company's long-term expansion plans into new territories such as Syria, Egypt, and North Africa. The need for greater control over existing warehouses and the ability to track health ministry requirements on products were critical issues that needed to be addressed.
About The Customer
The Sultan Center (TSC) is Kuwait’s largest independent retailer and a leading supplier of supermarket items, perishables, and general merchandise in the Middle East. The company operates 13 major retail outlets in Kuwait and holds a 15 percent share of the country’s retail market. TSC also has retail operations in Jordan, Oman, Bahrain, and Lebanon. The company is known for its broad range of foreign branded food products, imported from all over the world, which necessitates maintaining high on-shelf availability of all stocked brands. TSC's portfolio includes retail, restaurants, trading, fashion, and telecoms, making it a highly diversified business.
The Solution
The Sultan Center decided to implement Manhattan Associates’ Warehouse Management for Open Systems and Supply Chain Intelligence solutions at four of its sites in Kuwait. These solutions were chosen to enhance visibility of stock, improve picking rates and accuracy, handle increasing product volumes, and track goods against health ministry requirements. The implementation was completed in just eight weeks, even after a warehouse fire disrupted operations. The new system provided significant benefits, including increased efficiencies in warehouse operations such as put-away and picking, and dramatically improved pick accuracy and pick rates. Phase two of the project aims to leverage additional features like 'put-to-store' and 'multi-order picking' for further efficiency improvements and cost reductions.
Operational Impact
Quantitative Benefit
Related Case Studies.
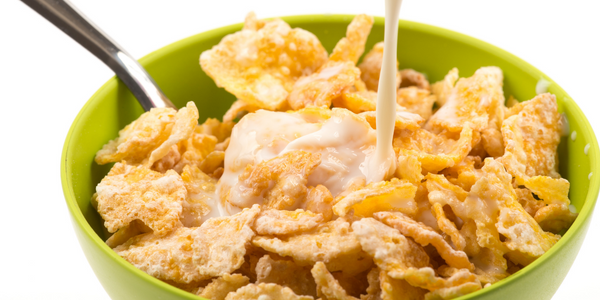
Case Study
The Kellogg Company
Kellogg keeps a close eye on its trade spend, analyzing large volumes of data and running complex simulations to predict which promotional activities will be the most effective. Kellogg needed to decrease the trade spend but its traditional relational database on premises could not keep up with the pace of demand.
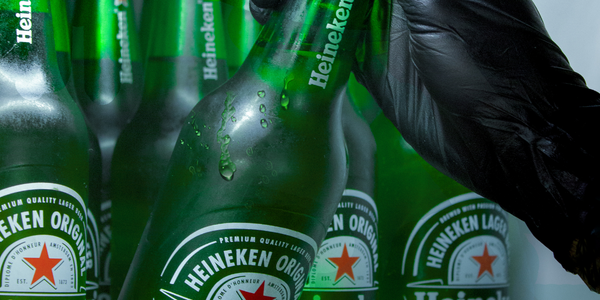
Case Study
HEINEKEN Uses the Cloud to Reach 10.5 Million Consumers
For 2012 campaign, the Bond promotion, it planned to launch the campaign at the same time everywhere on the planet. That created unprecedented challenges for HEINEKEN—nowhere more so than in its technology operation. The primary digital content for the campaign was a 100-megabyte movie that had to play flawlessly for millions of viewers worldwide. After all, Bond never fails. No one was going to tolerate a technology failure that might bruise his brand.Previously, HEINEKEN had supported digital media at its outsourced datacenter. But that datacenter lacked the computing resources HEINEKEN needed, and building them—especially to support peak traffic that would total millions of simultaneous hits—would have been both time-consuming and expensive. Nor would it have provided the geographic reach that HEINEKEN needed to minimize latency worldwide.
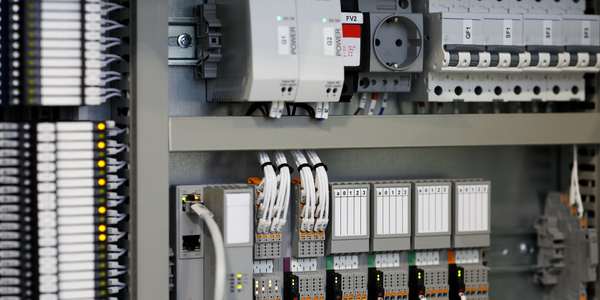
Case Study
Improving Production Line Efficiency with Ethernet Micro RTU Controller
Moxa was asked to provide a connectivity solution for one of the world's leading cosmetics companies. This multinational corporation, with retail presence in 130 countries, 23 global braches, and over 66,000 employees, sought to improve the efficiency of their production process by migrating from manual monitoring to an automatic productivity monitoring system. The production line was being monitored by ABB Real-TPI, a factory information system that offers data collection and analysis to improve plant efficiency. Due to software limitations, the customer needed an OPC server and a corresponding I/O solution to collect data from additional sensor devices for the Real-TPI system. The goal is to enable the factory information system to more thoroughly collect data from every corner of the production line. This will improve its ability to measure Overall Equipment Effectiveness (OEE) and translate into increased production efficiencies. System Requirements • Instant status updates while still consuming minimal bandwidth to relieve strain on limited factory networks • Interoperable with ABB Real-TPI • Small form factor appropriate for deployment where space is scarce • Remote software management and configuration to simplify operations
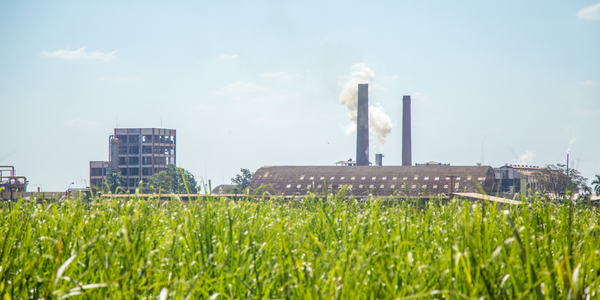
Case Study
Energy Management System at Sugar Industry
The company wanted to use the information from the system to claim under the renewable energy certificate scheme. The benefit to the company under the renewable energy certificates is Rs 75 million a year. To enable the above, an end-to-end solution for load monitoring, consumption monitoring, online data monitoring, automatic meter data acquisition which can be exported to SAP and other applications is required.
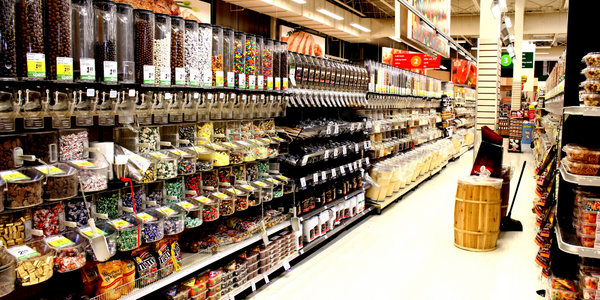
Case Study
How Sirqul’s IoT Platform is Crafting Carrefour’s New In-Store Experiences
Carrefour Taiwan’s goal is to be completely digital by end of 2018. Out-dated manual methods for analysis and assumptions limited Carrefour’s ability to change the customer experience and were void of real-time decision-making capabilities. Rather than relying solely on sales data, assumptions, and disparate systems, Carrefour Taiwan’s CEO led an initiative to find a connected IoT solution that could give the team the ability to make real-time changes and more informed decisions. Prior to implementing, Carrefour struggled to address their conversion rates and did not have the proper insights into the customer decision-making process nor how to make an immediate impact without losing customer confidence.