Download PDF
The Sweet Smell of Success
Technology Category
- Analytics & Modeling - Predictive Analytics
- Functional Applications - Manufacturing Execution Systems (MES)
Applicable Industries
- Consumer Goods
- Retail
Applicable Functions
- Quality Assurance
Use Cases
- Predictive Maintenance
- Process Control & Optimization
Services
- Software Design & Engineering Services
- System Integration
- Training
The Challenge
As part of continuous improvement efforts, Coty determined that its filling process was generating a higher level of waste than expected. This was due in part to some lines overfilling containers to ensure aesthetic fills were met, which led to higher expenses on supplies. Considering the price of some of the fill liquids, this realization provided a significant opportunity to reduce overfill and save money. However, the company did not have enough historical data on the lines that were overfilling to understand the entire problem. This meant that process engineers and quality professionals did not have sufficient information to develop a viable solution. The manufacturing team at Coty’s Sanford, North Carolina, manufacturing facility turned to Statistical Process Control (SPC) analysis to better understand scrap at the point of manufacture on its filling lines. As part of its SPC Fill Height Project, Coty wanted to determine ways to reduce liquid scrap and better understand its process capability.
About The Customer
Coty, a leader in the global beauty and fragrance industry, was founded in Paris in 1904 by François Coty. The company today exhibits innovation and a drive to quickly capture emerging trends, creating enduring brands that speak to the aspirations and lifestyles of today’s consumers. That spirit of innovation leads Coty to pursue continuous improvements in all its operations. Driven by passion, creative freedom, and an entrepreneurial spirit, Coty has built a unique portfolio of beauty brands that include some of the strongest consumer franchises in history. The company’s products span fragrances, color cosmetics, and skin and body care. Coty has an annual revenue of over $8 billion, is headquartered in New York City with offices in more than 35 countries, and employs 19,000 people worldwide. The company has a global manufacturing presence with Research and Development Centers of Excellence, 8 manufacturing facilities, and locations in Europe, the United States, and China.
The Solution
Coty approached InfinityQS, the global authority on manufacturing quality management, about implementing its proven Quality Intelligence software—powered by a centralized SPC analysis engine—at its Sanford facility. Coty used InfinityQS Professional Services to help ensure the most effective deployment of the solution. Leveraging the skills and experience of InfinityQS’ certified quality engineers, industrial statisticians, and Six Sigma Black Belts, Coty implemented its SPC Fill Height Project incrementally across 12 fragrance lines. The company set target amounts for every SKU (2,600 parts), control limits for each product and line combination (filling variation), and specification limits (min and max fill height levels). The implementation process also included training for more than 100 users, from line operators and quality inspectors to managers and directors. This highly focused, customized training helps promote a positive adoption of the new solution by users, ensuring they enjoy the benefits of the new tools at their disposal. Training also helps ensure the company gets the greatest value from its software investment.
Operational Impact
Quantitative Benefit
Related Case Studies.
.png)
Case Study
Improving Vending Machine Profitability with the Internet of Things (IoT)
The vending industry is undergoing a sea change, taking advantage of new technologies to go beyond just delivering snacks to creating a new retail location. Intelligent vending machines can be found in many public locations as well as company facilities, selling different types of goods and services, including even computer accessories, gold bars, tickets, and office supplies. With increasing sophistication, they may also provide time- and location-based data pertaining to sales, inventory, and customer preferences. But at the end of the day, vending machine operators know greater profitability is driven by higher sales and lower operating costs.
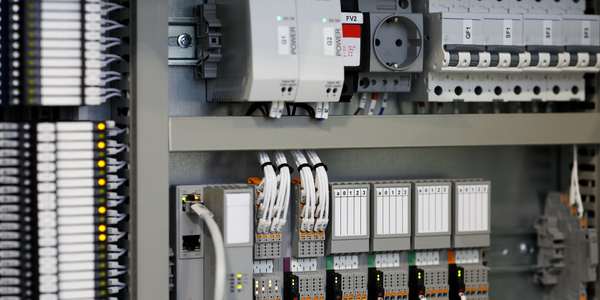
Case Study
Improving Production Line Efficiency with Ethernet Micro RTU Controller
Moxa was asked to provide a connectivity solution for one of the world's leading cosmetics companies. This multinational corporation, with retail presence in 130 countries, 23 global braches, and over 66,000 employees, sought to improve the efficiency of their production process by migrating from manual monitoring to an automatic productivity monitoring system. The production line was being monitored by ABB Real-TPI, a factory information system that offers data collection and analysis to improve plant efficiency. Due to software limitations, the customer needed an OPC server and a corresponding I/O solution to collect data from additional sensor devices for the Real-TPI system. The goal is to enable the factory information system to more thoroughly collect data from every corner of the production line. This will improve its ability to measure Overall Equipment Effectiveness (OEE) and translate into increased production efficiencies. System Requirements • Instant status updates while still consuming minimal bandwidth to relieve strain on limited factory networks • Interoperable with ABB Real-TPI • Small form factor appropriate for deployment where space is scarce • Remote software management and configuration to simplify operations
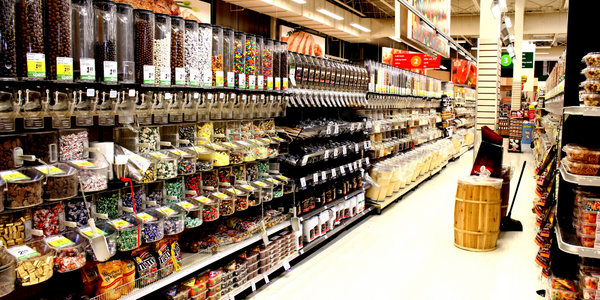
Case Study
How Sirqul’s IoT Platform is Crafting Carrefour’s New In-Store Experiences
Carrefour Taiwan’s goal is to be completely digital by end of 2018. Out-dated manual methods for analysis and assumptions limited Carrefour’s ability to change the customer experience and were void of real-time decision-making capabilities. Rather than relying solely on sales data, assumptions, and disparate systems, Carrefour Taiwan’s CEO led an initiative to find a connected IoT solution that could give the team the ability to make real-time changes and more informed decisions. Prior to implementing, Carrefour struggled to address their conversion rates and did not have the proper insights into the customer decision-making process nor how to make an immediate impact without losing customer confidence.
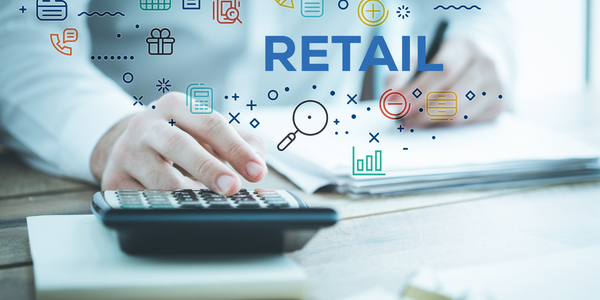
Case Study
Digital Retail Security Solutions
Sennco wanted to help its retail customers increase sales and profits by developing an innovative alarm system as opposed to conventional connected alarms that are permanently tethered to display products. These traditional security systems were cumbersome and intrusive to the customer shopping experience. Additionally, they provided no useful data or analytics.