Download PDF
There in a Pinch for Smokey Mountain Snuf
Technology Category
- Functional Applications - Enterprise Resource Planning Systems (ERP)
Applicable Industries
- Consumer Goods
Applicable Functions
- Discrete Manufacturing
- Quality Assurance
Use Cases
- Manufacturing System Automation
Services
- System Integration
The Challenge
When Dan Calandro joined Smokey Mountain Chew as CFO in January 1999, he discovered that a great product doesn’t automatically provide great margins. After conducting a thorough financial and operational review, he found that Smokey Mountain’s quality and profitability fell way short of its tremendous potential. Its inadequate off-the-shelf accounting package was part of the problem. It had to be replaced with a system that could handle Smokey Mountain’s complex manufacturing and distribution operations. Quality assurance was Calandro’s initial concern. Product taste and texture were inconsistent from batch to batch. This called for tighter manufacturing controls, closer production monitoring, and batch analysis.
About The Customer
Smokey Mountain Chew is a company that produces America’s original and best-selling tobacco-free snuff. The company offers an all-natural herbal blend in Classic, Wintergreen, Cherry, and Arctic Mint. Despite having a great product, the company was struggling with quality and profitability issues. The product taste and texture were inconsistent from batch to batch, and the company's off-the-shelf accounting package was inadequate for handling its complex manufacturing and distribution operations.
The Solution
Calandro selected Sage 100 ERP to replace the inadequate off-the-shelf accounting package. Through Sage 100 ERP, a yield analysis report was created utilizing a standard deviation schedule to highlight significant variations by batch. By pinpointing production dates and associated yields, The Sage 100 ERP Bill of Materials module allowed Calandro to establish a quality control matrix. Guidelines were created in the Bill of Materials module for all steps in the manufacturing process, giving Calandro criteria for refusal. The onus of responsibility then fell on the contract manufacturer. Materials falling outside of the criteria are now destroyed, and the costs plus a service charge are billed back to the contract manufacturer.
Operational Impact
Quantitative Benefit
Related Case Studies.
.png)
Case Study
Improving Vending Machine Profitability with the Internet of Things (IoT)
The vending industry is undergoing a sea change, taking advantage of new technologies to go beyond just delivering snacks to creating a new retail location. Intelligent vending machines can be found in many public locations as well as company facilities, selling different types of goods and services, including even computer accessories, gold bars, tickets, and office supplies. With increasing sophistication, they may also provide time- and location-based data pertaining to sales, inventory, and customer preferences. But at the end of the day, vending machine operators know greater profitability is driven by higher sales and lower operating costs.
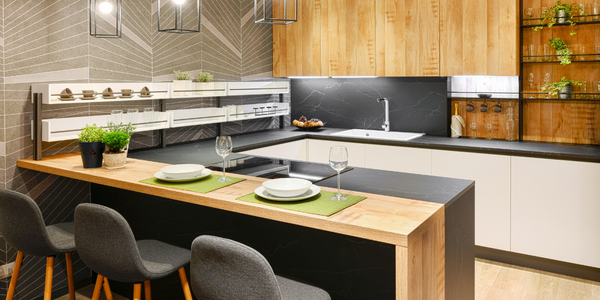
Case Study
Series Production with Lot-size-1 Flexibility
Nobilia manufactures customized fitted kitchens with a lot size of 1. They require maximum transparency of tracking design data and individual processing steps so that they can locate a particular piece of kitchen furniture in the sequence of processes.
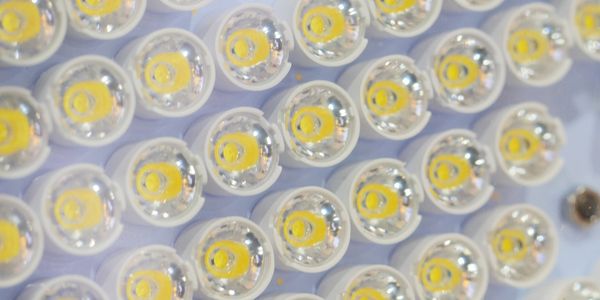
Case Study
American Eagle Achieves LEED with GE LED Lighting Fixtures
American Eagle Outfitters (AEO) was in the process of building a new distribution center. The AEO facility management team decided to look at alternate options for lighting layout that could provide energy and maintenance savings. AEO would need a full-time maintenance employee just to replace burned-out fluorescent tubes.
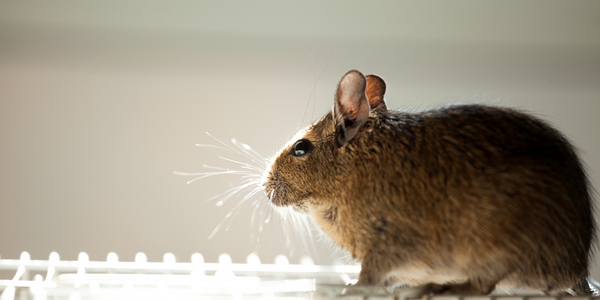
Case Study
Revolutionizing Rodent Control
From pet- and child-safe traps, to touch-free and live-catch rodent control solutions, Victor continues to stay committed to producing superior products that meet the varying needs of today’s pest control professionals. And, with a long standing history supporting customers in the food processing, service, and retail settings, Victor knew that strict regulations were costing organizations thousands of dollars in excess overhead trying to manage their rodent-control solutions. Trap inspections in these environments are often difficult and time consuming, requiring personnel to manually check a trap’s status multiple times per day, amounting to over six hours of manual labor. Victor is looking for an innovative way to increase operational efficiencies with the use of technology.