Download PDF
Third-Party Logistics Company Finds Increases in Productivity
Technology Category
- Functional Applications - Warehouse Management Systems (WMS)
- Automation & Control - Automation & Process Control Systems
Applicable Functions
- Warehouse & Inventory Management
- Logistics & Transportation
Use Cases
- Warehouse Automation
- Inventory Management
Services
- System Integration
The Challenge
Consolidating two warehouse spaces into one meant a chance for Pacific Coast Warehouse to gain efficiency and improve control over product movement. It also meant considering a different warehouse design and installing a new fleet of lift trucks to work in racking that is significantly higher than the racking in the previous locations. As part of its research on which material handling company would obtain the order for the new lift trucks, Pacific Coast Warehouse tested all the competition, both in a controlled environment and on site in one of its facilities. The decision came down to projected value in productivity and ease of financing.
About The Customer
In business since 1927, Pacific Coast Warehouse Company is a third-party logistics company that operates more than 1.3 million square feet of warehousing space in southern and northern California. It provides storage, handling, and transportation services to manufacturers that import products from overseas. The company has a long-standing reputation for reliability and efficiency in the logistics sector, serving a diverse range of clients with varying needs. With a focus on optimizing warehouse operations and improving service delivery, Pacific Coast Warehouse continually seeks innovative solutions to enhance its operational capabilities.
The Solution
Raymond Handling Solutions, an authorized Raymond Sales and Service Center and partner of Pacific Coast Warehouse for more than 26 years, was selected for the project in a competitive review process after offering not only lift trucks but a complete, integrated solution that included racking, lift trucks, and a comprehensive lift truck service program. With the objectives of improving productivity, storing the same amount of pallets, and achieving the same revenue within a smaller footprint, Raymond Handling Solutions helped the company devise a material handling system using Raymond Model 7400 Deep-Reach® lift trucks to place loads of product on 26-foot-high racks. The all-AC-drive lift trucks were projected to deliver 20 to 25 percent higher productivity with 15 to 20 percent energy savings when compared with the trucks used at the existing sites.
Operational Impact
Quantitative Benefit
Related Case Studies.
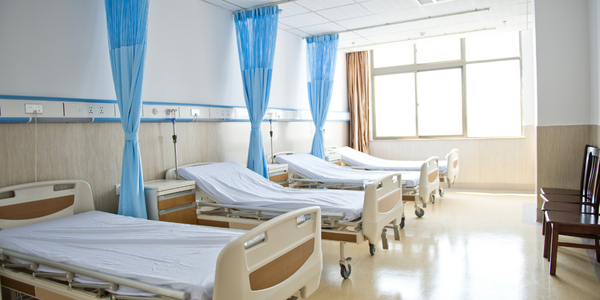
Case Study
Hospital Inventory Management
The hospital supply chain team is responsible for ensuring that the right medical supplies are readily available to clinicians when and where needed, and to do so in the most efficient manner possible. However, many of the systems and processes in use at the cancer center for supply chain management were not best suited to support these goals. Barcoding technology, a commonly used method for inventory management of medical supplies, is labor intensive, time consuming, does not provide real-time visibility into inventory levels and can be prone to error. Consequently, the lack of accurate and real-time visibility into inventory levels across multiple supply rooms in multiple hospital facilities creates additional inefficiency in the system causing over-ordering, hoarding, and wasted supplies. Other sources of waste and cost were also identified as candidates for improvement. Existing systems and processes did not provide adequate security for high-cost inventory within the hospital, which was another driver of cost. A lack of visibility into expiration dates for supplies resulted in supplies being wasted due to past expiry dates. Storage of supplies was also a key consideration given the location of the cancer center’s facilities in a dense urban setting, where space is always at a premium. In order to address the challenges outlined above, the hospital sought a solution that would provide real-time inventory information with high levels of accuracy, reduce the level of manual effort required and enable data driven decision making to ensure that the right supplies were readily available to clinicians in the right location at the right time.

Case Study
IoT Solution for Cold Chain
Most of the customer's warehouses run on utility and generator power. Since these warehouses are in remote locations, power outages are a very common scenario. Diesel fuel, thereby, becomes a significant cost for these warehouses. Energy consumption was also very high due to the lack of a consistent temperature throughout the facility. This lack of a consistent temperature in all areas and no way to control it, resulted in the customer losing a significant amount of their temperature sensitive goods due to spoilage.
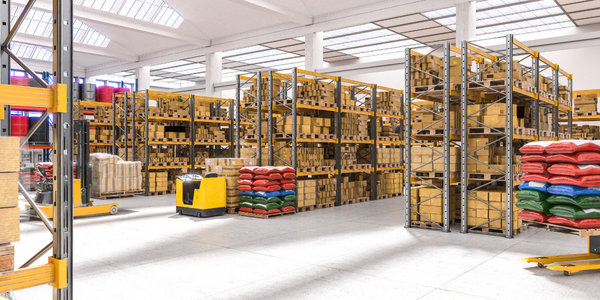
Case Study
Hardware Retailer Uses Data Warehouse to Track Inventory
Ace tracked which products retailers ordered, when they were ordered and shipped. However, the company could not track or forecast actual sales. Data used for reporting was up to a one-week old, owing to performance and data cleansing issues. Requirement to integrate wholesale and inventory data with POS data to help drive key business decisions, improve category management, lower inventory costs and optimize pricing. Reliance on custom coding to integrate POS data was excessively resource intensive and led to major performance constraints.
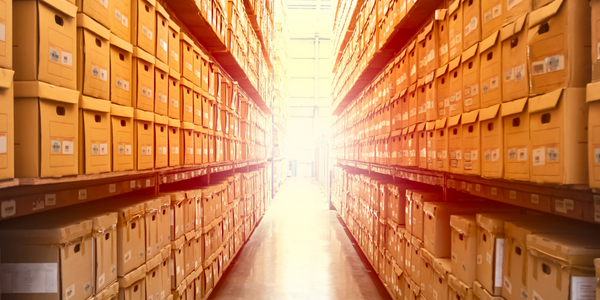
Case Study
DSV Road levels their workflow and decreases stress thanks to 4 BT Autopilots
During peaks in the workflow employeescan experience stress which makes them prone to causing damage. Avoiding these peaks also eliminates the need to hire temporary workers that require extra time and costs for education.