Download PDF
Transforming Health and Safety Reporting with IoT: Avara Foods Case Study
Applicable Industries
- Food & Beverage
- Healthcare & Hospitals
Use Cases
- Onsite Human Safety Management
Services
- Training
The Challenge
Avara Foods, one of the UK's largest food businesses, was grappling with a labor-intensive, paper-based health and safety reporting process. The company's health and safety teams were tasked with managing the risk of accidents within the farms, factories, and office areas. They relied on paper forms and Excel to collect, analyze, and mitigate accident risk. However, as the business expanded, the number of independent paper-based systems also increased, making it increasingly difficult to manage the required interventions. Consolidating a view of health and safety risk across the sites took several days. The situation was further complicated by a merger with another food business, which necessitated a complete review of the processes and systems employed.
About The Customer
Avara Foods is one of the UK's largest food businesses, supplying poultry products to some of Britain's largest supermarkets and restaurant chains. The company operates seven food processing plants, six hatcheries, three mills for producing poultry feed, and 100 owned and subcontracted farms. Avara Foods has been using K2 Software for over 20 years to streamline processes and deliver ongoing efficiencies for the business. The company employs 7,000 people and is committed to improving health and safety across its operations.
The Solution
Avara Foods turned to Nintex K2 Five to digitize and automate its health and safety reporting process. The company replaced its paper-based process with a digital form, automated workflow, and centralized reporting dashboard. A standardized approach for first aid incident reporting was created, which could be used across the organization's seven food processing plants, six hatcheries, three mills, and 100 owned and subcontracted farms. Employees record details of any incidents in a digital form, which is then passed electronically to line managers and the health and safety manager for review and approval. The Nintex K2 Five-based process provides Avara Foods with oversight of all first aid incidents across the business on digital dashboards. The company can now use a Nintex K2 Five dashboard in health and safety campaigns to monitor the impact of its interventions.
Operational Impact
Quantitative Benefit
Related Case Studies.
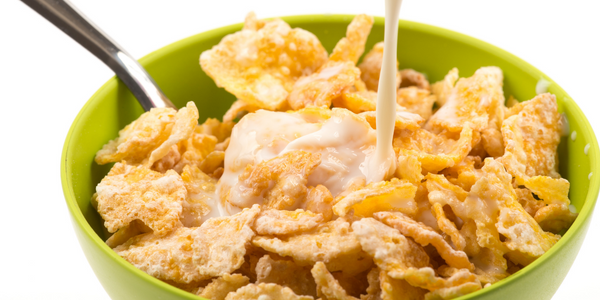
Case Study
The Kellogg Company
Kellogg keeps a close eye on its trade spend, analyzing large volumes of data and running complex simulations to predict which promotional activities will be the most effective. Kellogg needed to decrease the trade spend but its traditional relational database on premises could not keep up with the pace of demand.
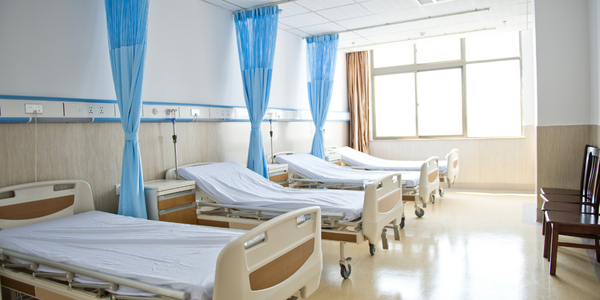
Case Study
Hospital Inventory Management
The hospital supply chain team is responsible for ensuring that the right medical supplies are readily available to clinicians when and where needed, and to do so in the most efficient manner possible. However, many of the systems and processes in use at the cancer center for supply chain management were not best suited to support these goals. Barcoding technology, a commonly used method for inventory management of medical supplies, is labor intensive, time consuming, does not provide real-time visibility into inventory levels and can be prone to error. Consequently, the lack of accurate and real-time visibility into inventory levels across multiple supply rooms in multiple hospital facilities creates additional inefficiency in the system causing over-ordering, hoarding, and wasted supplies. Other sources of waste and cost were also identified as candidates for improvement. Existing systems and processes did not provide adequate security for high-cost inventory within the hospital, which was another driver of cost. A lack of visibility into expiration dates for supplies resulted in supplies being wasted due to past expiry dates. Storage of supplies was also a key consideration given the location of the cancer center’s facilities in a dense urban setting, where space is always at a premium. In order to address the challenges outlined above, the hospital sought a solution that would provide real-time inventory information with high levels of accuracy, reduce the level of manual effort required and enable data driven decision making to ensure that the right supplies were readily available to clinicians in the right location at the right time.
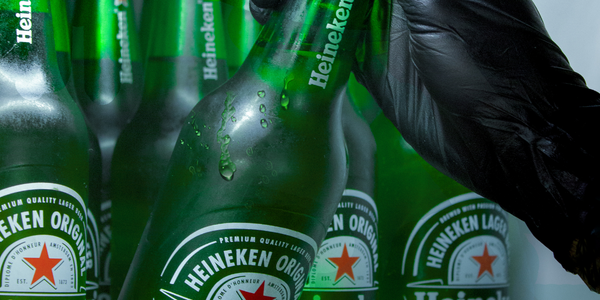
Case Study
HEINEKEN Uses the Cloud to Reach 10.5 Million Consumers
For 2012 campaign, the Bond promotion, it planned to launch the campaign at the same time everywhere on the planet. That created unprecedented challenges for HEINEKEN—nowhere more so than in its technology operation. The primary digital content for the campaign was a 100-megabyte movie that had to play flawlessly for millions of viewers worldwide. After all, Bond never fails. No one was going to tolerate a technology failure that might bruise his brand.Previously, HEINEKEN had supported digital media at its outsourced datacenter. But that datacenter lacked the computing resources HEINEKEN needed, and building them—especially to support peak traffic that would total millions of simultaneous hits—would have been both time-consuming and expensive. Nor would it have provided the geographic reach that HEINEKEN needed to minimize latency worldwide.
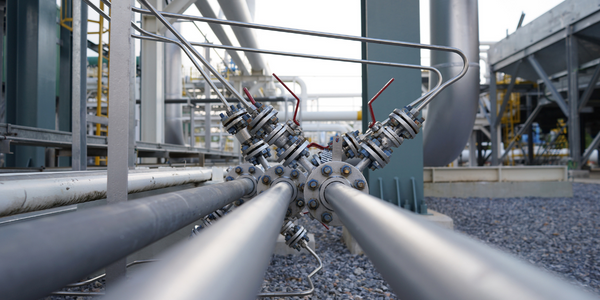
Case Study
Gas Pipeline Monitoring System for Hospitals
This system integrator focuses on providing centralized gas pipeline monitoring systems for hospitals. The service they provide makes it possible for hospitals to reduce both maintenance and labor costs. Since hospitals may not have an existing network suitable for this type of system, GPRS communication provides an easy and ready-to-use solution for remote, distributed monitoring systems System Requirements - GPRS communication - Seamless connection with SCADA software - Simple, front-end control capability - Expandable I/O channels - Combine AI, DI, and DO channels
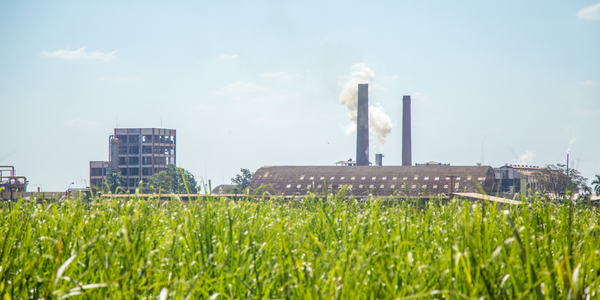
Case Study
Energy Management System at Sugar Industry
The company wanted to use the information from the system to claim under the renewable energy certificate scheme. The benefit to the company under the renewable energy certificates is Rs 75 million a year. To enable the above, an end-to-end solution for load monitoring, consumption monitoring, online data monitoring, automatic meter data acquisition which can be exported to SAP and other applications is required.