Download PDF
Turning Salt into Sales
Technology Category
- Functional Applications - Enterprise Resource Planning Systems (ERP)
Applicable Functions
- Business Operation
- Quality Assurance
- Warehouse & Inventory Management
Use Cases
- Inventory Management
- Predictive Maintenance
- Process Control & Optimization
Services
- Software Design & Engineering Services
- System Integration
The Challenge
After acquiring two plants, US Salt realized the need to improve customer service, reduce costs, and enhance overall operational efficiency. The company decided to link its plants and headquarters through a Wide Area Network (WAN) and centralize certain financial business functions. The most expedient hardware setup was determined to be a client/server configuration with the server residing in Jacksonville and client workstations in Jacksonville and the two plants. This setup would leverage currently installed hardware and provide the benefits of a centrally managed system, including ease of maintenance, avoidance of duplication of functionality, and easy implementation of software upgrades. Additionally, it would ensure that the most current information was readily available to users.
About The Customer
U.S. Salt, with annual revenues exceeding thirty million dollars, is a major producer of salt globally. The privately held company serves a diverse range of customers, from bakeries and pharmaceutical manufacturers that buy salt in bulk to OEMs requiring prepackaging and private labeling of various salt products. The company offers about 20 different lines of salt products, including table salt, salt crystals, salt blocks, and sodium nitrite, a compound used as a preservative and in various rubber formulas. Headquartered in Jacksonville, Florida, U.S. Salt maintains plants in Watkins Glen, New York, where most of the salt is extracted, and in Gibbstown, New Jersey.
The Solution
The Watkins Glen facility had been using an ERP solution that was not conducive to a client/server architecture. US Salt's reseller suggested SYSPRO ERP software, which is designed specifically for client/server environments and is easily scalable. SYSPRO's ability to address formulas and recipes as a process client, along with its balanced functionality for manufacturing, financial, and distribution processes, influenced the decision. The reseller's experience in implementing software in industries with various manufacturing methods was also a critical factor. SYSPRO ERP software was implemented to accommodate US Salt's diverse manufacturing methodologies, including batch process, continuous process, make-to-stock, and make-to-order. The software's flexibility allowed US Salt to meet customer demand while maximizing plant capacities. SYSPRO also provided unexpected benefits, such as user-friendly Windows-based operation, customizable screens, shortcut keys, and an event management feature. Additionally, data could be easily downloaded from the SYSPRO database to Microsoft Access for management reporting.
Operational Impact
Quantitative Benefit
Related Case Studies.
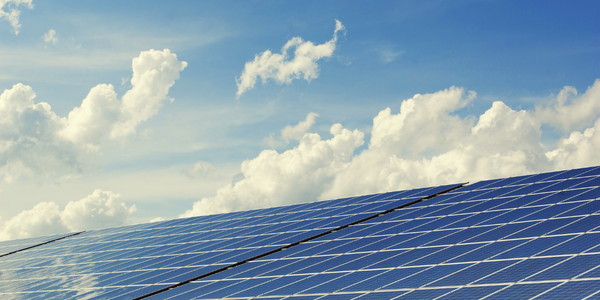
Case Study
Remote Monitoring & Predictive Maintenance App for a Solar Energy System
The maintenance & tracking of various modules was an overhead for the customer due to the huge labor costs involved. Being an advanced solar solutions provider, they wanted to ensure early detection of issues and provide the best-in-class customer experience. Hence they wanted to automate the whole process.
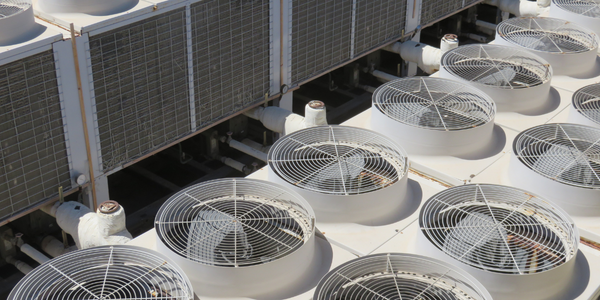
Case Study
Predictive Maintenance for Industrial Chillers
For global leaders in the industrial chiller manufacturing, reliability of the entire production process is of the utmost importance. Chillers are refrigeration systems that produce ice water to provide cooling for a process or industrial application. One of those leaders sought a way to respond to asset performance issues, even before they occur. The intelligence to guarantee maximum reliability of cooling devices is embedded (pre-alarming). A pre-alarming phase means that the cooling device still works, but symptoms may appear, telling manufacturers that a failure is likely to occur in the near future. Chillers who are not internet connected at that moment, provide little insight in this pre-alarming phase.
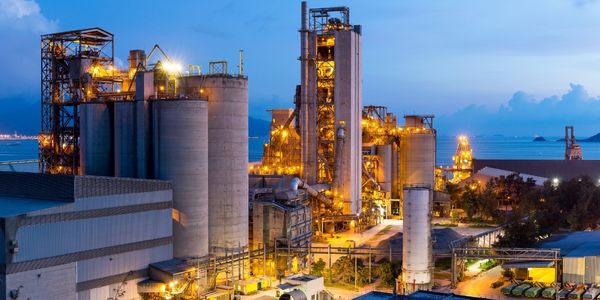
Case Study
System 800xA at Indian Cement Plants
Chettinad Cement recognized that further efficiencies could be achieved in its cement manufacturing process. It looked to investing in comprehensive operational and control technologies to manage and derive productivity and energy efficiency gains from the assets on Line 2, their second plant in India.
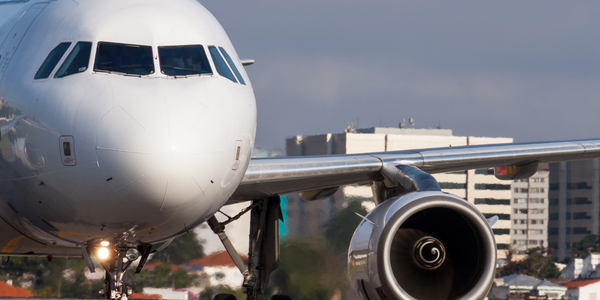
Case Study
Airbus Soars with Wearable Technology
Building an Airbus aircraft involves complex manufacturing processes consisting of thousands of moving parts. Speed and accuracy are critical to business and competitive advantage. Improvements in both would have high impact on Airbus’ bottom line. Airbus wanted to help operators reduce the complexity of assembling cabin seats and decrease the time required to complete this task.
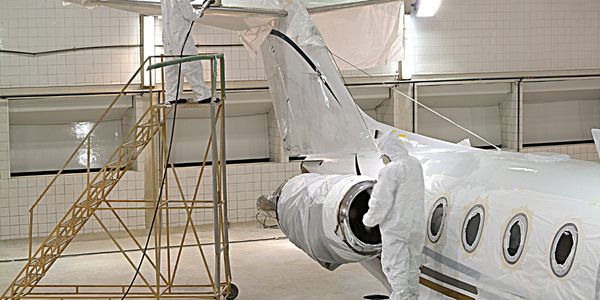
Case Study
Aircraft Predictive Maintenance and Workflow Optimization
First, aircraft manufacturer have trouble monitoring the health of aircraft systems with health prognostics and deliver predictive maintenance insights. Second, aircraft manufacturer wants a solution that can provide an in-context advisory and align job assignments to match technician experience and expertise.