Download PDF
Unilever's Journey to Optimizing Packaging Designs & Reducing Prototype Costs with IoT
Applicable Industries
- Life Sciences
- Packaging
Applicable Functions
- Product Research & Development
Use Cases
- Intelligent Packaging
- Manufacturing Process Simulation
The Challenge
Unilever, a global leader in the consumer goods industry, was seeking ways to maintain its innovative edge in the male grooming market. The company was particularly focused on differentiating its Lynx (Axe) brand from competitors. The challenge was to design a new deodorant packaging concept that would stand out in the market. However, Unilever lacked the necessary in-house expertise to adopt a simulation and analysis approach for the design and testing of the new can. They needed a development partner to assist with the design and testing of the new packaging concept.
About The Customer
Unilever is a multinational consumer goods company with a strong presence in over 190 countries. The company's product portfolio includes food, beverages, cleaning agents, and personal care products. Unilever is known for its commitment to innovation and constantly seeks ways to differentiate its products from competitors. In this case, the company was focused on enhancing its Lynx (Axe) brand, a popular male grooming product line. The challenge was to design a new deodorant packaging concept that would stand out in the market, but Unilever lacked the necessary in-house expertise to adopt a simulation and analysis approach for the design and testing of the new can.
The Solution
Unilever partnered with Altair ProductDesign to tackle this challenge. The initial deodorant can design concept was created by Unilever, with Altair ProductDesign conducting optimization to define material layouts for stiffening the cap’s button and optimizing the load path through the can’s side walls. A more detailed model was then developed to investigate a series of ‘what if’ scenarios such as loading values, geometry changes, and material options. This process identified areas for reinforcement throughout the cap and measured the effects of different material properties on stiffness and stress. These were then ranked against manufacturing cost, providing valuable metrics for material selection decisions. Altair ProductDesign also equipped Unilever with a set of new process tools developed specifically for packaging design. The ‘Atlas’ system, developed over a 4-5 year period in close collaboration with Unilever’s Capability Development team, allows Unilever’s CAD and concept designers to perform analysis studies very early in the design process.
Operational Impact
Quantitative Benefit
Related Case Studies.
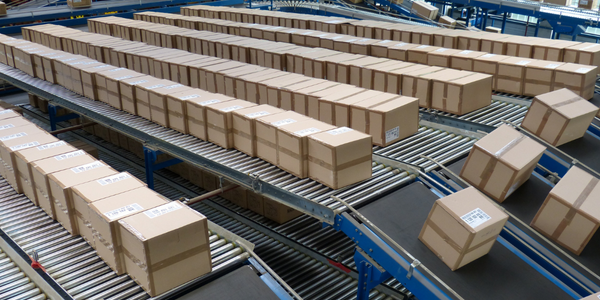
Case Study
IoT Data Analytics Case Study - Packaging Films Manufacturer
The company manufactures packaging films on made to order or configure to order basis. Every order has a different set of requirements from the product characteristics perspective and hence requires machine’s settings to be adjusted accordingly. If the film quality does not meet the required standards, the degraded quality impacts customer delivery causes customer dissatisfaction and results in lower margins. The biggest challenge was to identify the real root cause and devise a remedy for that.
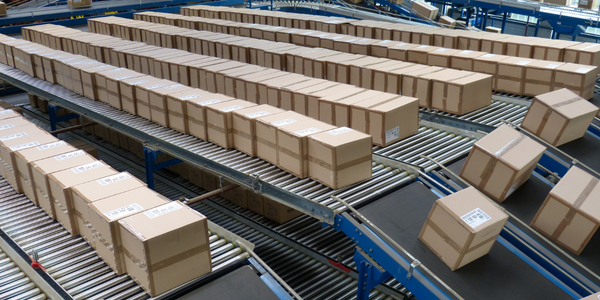
Case Study
Zenon the Ideal Basis for An Ergonomic HMI
KHS develops and produces machines and equipment for filling and packaging in the drinks industry. Because drinks manufacturing, filling and packaging consist of a number of highly complex processes, the user-friendly and intuitive operation of equipment is increasingly gaining in significance. In order to design these processes as simple as possible for the user, KHS decided to introduce a uniform, transparent and standardized solution to the company. The HMI interface should meet the requirement for people with different qualifications and enable them to work on a standard platform.
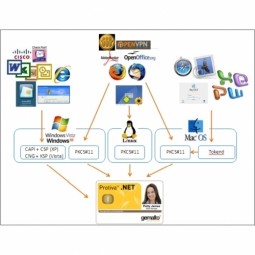
Case Study
Corporate Identity Solution Adds Convenience to Beckman Coulter
Beckman Coulter wanted to implement a single factor solution for physical and remote logical access to corporate network. Bechman Coulter's users were carrying smart card badges for doors, but also needed a one-time password token to access to our corporate network when they were not in the office. They wanted to simplify the process.
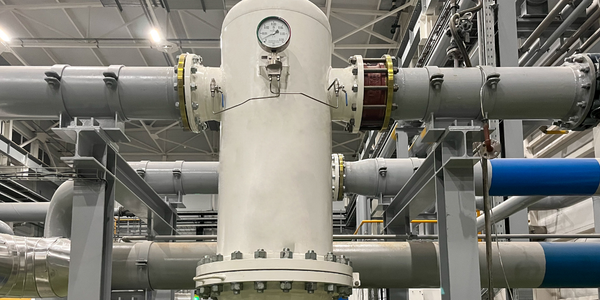
Case Study
Sparks Dynamics Assists Atlas Container Secure a $15,000 BGE Energy Rebate
The ReMASTER Compressed Air Monitoring system was installed in 2015. This system is capable of monitoring compressed air system parameters on a continuous basis and transferring that information to a cloud server which can be accessed by Atlas Container personnel, Industrial Diagnostics and Sparks Dynamics. This information was collected into a database which can be exported to an Excel spreadsheet or displayed graphically using Sparks Dynamics ViewMaster Software. The average annual compressed air electricity expense was estimated to be approximately $116,000. This is based on an incremental $/KWh electric rate of $.091 per KWh and an estimated compressed air energy consumption of 1,279,200 KWH. The implementation phase of Energy Conservation Measures (ECMs) for the Compressed Air System included: • Identification and repair of compressed air leaks • Understanding of compressed air usage per manufacturing machine and installation of shut off valves when the machines are no longer in production mode • Identification of misapplications of compressed air to include blow offs, venturis, and cooling scenarios • Understand system pressure requirements and potential installation of point of use pressure regulation.
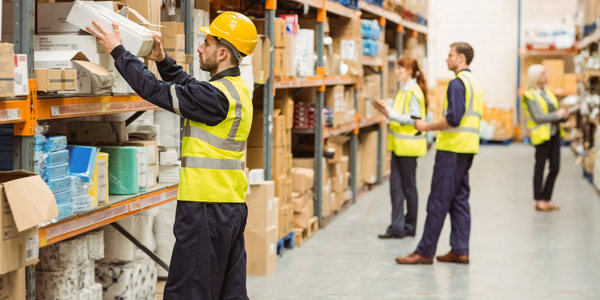
Case Study
Automated Pallet Labeling Solution for SPR Packaging
SPR Packaging, an American supplier of packaging solutions, was in search of an automated pallet labeling solution that could meet their immediate and future needs. They aimed to equip their lines with automatic printer applicators, but also required a solution that could interface with their accounting software. The challenge was to find a system that could read a 2D code on pallets at the stretch wrapper, track the pallet, and flag any pallets with unread barcodes for inspection. The pallets could be single or double stacked, and the system needed to be able to differentiate between the two. SPR Packaging sought a system integrator with extensive experience in advanced printing and tracking solutions to provide a complete traceability system.
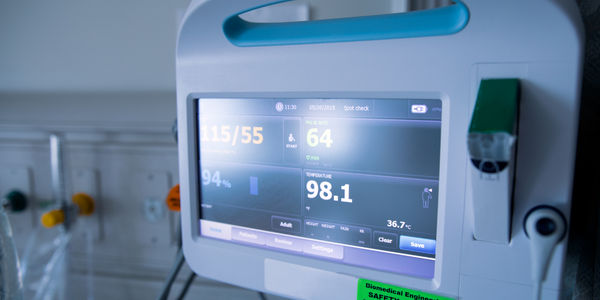
Case Study
Mondi Implements Statistics-Based Health Monitoring and Predictive Maintenance
The extrusion and other machines at Mondi’s plant are large and complex, measuring up to 50 meters long and 15 meters high. Each machine is controlled by up to five programmable logic controllers (PLCs), which log temperature, pressure, velocity, and other performance parameters from the machine’s sensors. Each machine records 300–400 parameter values every minute, generating 7 gigabytes of data daily.Mondi faced several challenges in using this data for predictive maintenance. First, the plant personnel had limited experience with statistical analysis and machine learning. They needed to evaluate a variety of machine learning approaches to identify which produced the most accurate results for their data. They also needed to develop an application that presented the results clearly and immediately to machine operators. Lastly, they needed to package this application for continuous use in a production environment.