Download PDF
US Air Force Optimizes CubeSat using Architected Materials
Technology Category
- Analytics & Modeling - Digital Twin / Simulation
- Analytics & Modeling - Generative AI
- Other - Additive Manufacturing
Applicable Industries
- Aerospace
Applicable Functions
- Product Research & Development
- Quality Assurance
Use Cases
- Digital Twin
- Manufacturing System Automation
- Rapid Prototyping
Services
- Software Design & Engineering Services
- System Integration
The Challenge
The U.S. Air Force Institute of Technology (AFIT) faced the challenge of reducing the weight and production time of a CubeSat bus, which traditionally required machining of nearly 150 parts. The conventional design demanded tight tolerances and close quality control, creating 150 potential points of failure. The goal was to develop a structure that fulfills all design requirements and can be manufactured using a repeatable process.
About The Customer
The U.S. Air Force Institute of Technology (AFIT) is a premier institution that provides advanced education and research opportunities to military and civilian personnel. AFIT focuses on leveraging cutting-edge technologies to solve complex engineering challenges. In this case, AFIT aimed to optimize the CubeSat bus, a small and relatively inexpensive satellite used for research and communications by government and private agencies. CubeSats enable the concept of ridesharing, allowing multiple satellites to be launched on a single structural chassis, thereby reducing the high cost of sending a payload into orbit.
The Solution
AFIT used nTopology's software to leverage architected materials, developing a CubeSat bus assembly from Inconel 718 that was 50% lighter and 20% stiffer than the original aluminum assembly. The R&D team explored multiple thin-walled TMPS and strut-based lattice structures, assessing their performance using engineering simulation. After several iterations, they identified a design with a superior stiffness-to-weight ratio and a lower coefficient of thermal expansion. Using nTopology’s direct-to-manufacture capabilities, the team bypassed the need to generate STL files, creating slices and tool paths directly in the design software. A 3D printed and finished CubeSat was ready for testing in only 3.5 business days. The structural bus was then evaluated and certified according to the NASA GEVS launch profile methodology.
Operational Impact
Quantitative Benefit
Related Case Studies.
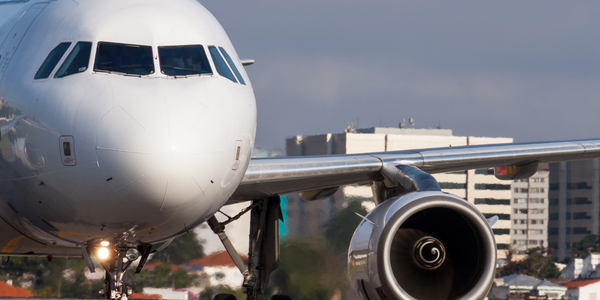
Case Study
Airbus Soars with Wearable Technology
Building an Airbus aircraft involves complex manufacturing processes consisting of thousands of moving parts. Speed and accuracy are critical to business and competitive advantage. Improvements in both would have high impact on Airbus’ bottom line. Airbus wanted to help operators reduce the complexity of assembling cabin seats and decrease the time required to complete this task.
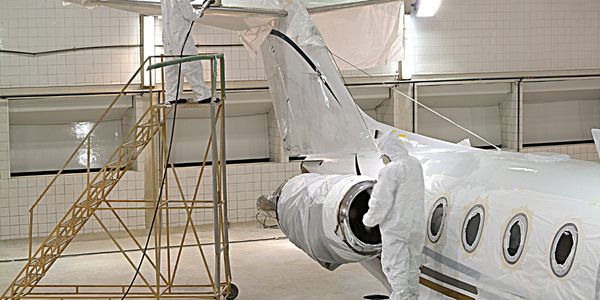
Case Study
Aircraft Predictive Maintenance and Workflow Optimization
First, aircraft manufacturer have trouble monitoring the health of aircraft systems with health prognostics and deliver predictive maintenance insights. Second, aircraft manufacturer wants a solution that can provide an in-context advisory and align job assignments to match technician experience and expertise.
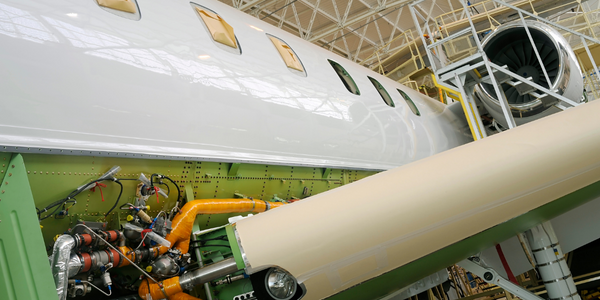
Case Study
Aerospace & Defense Case Study Airbus
For the development of its new wide-body aircraft, Airbus needed to ensure quality and consistency across all internal and external stakeholders. Airbus had many challenges including a very aggressive development schedule and the need to ramp up production quickly to satisfy their delivery commitments. The lack of communication extended design time and introduced errors that drove up costs.
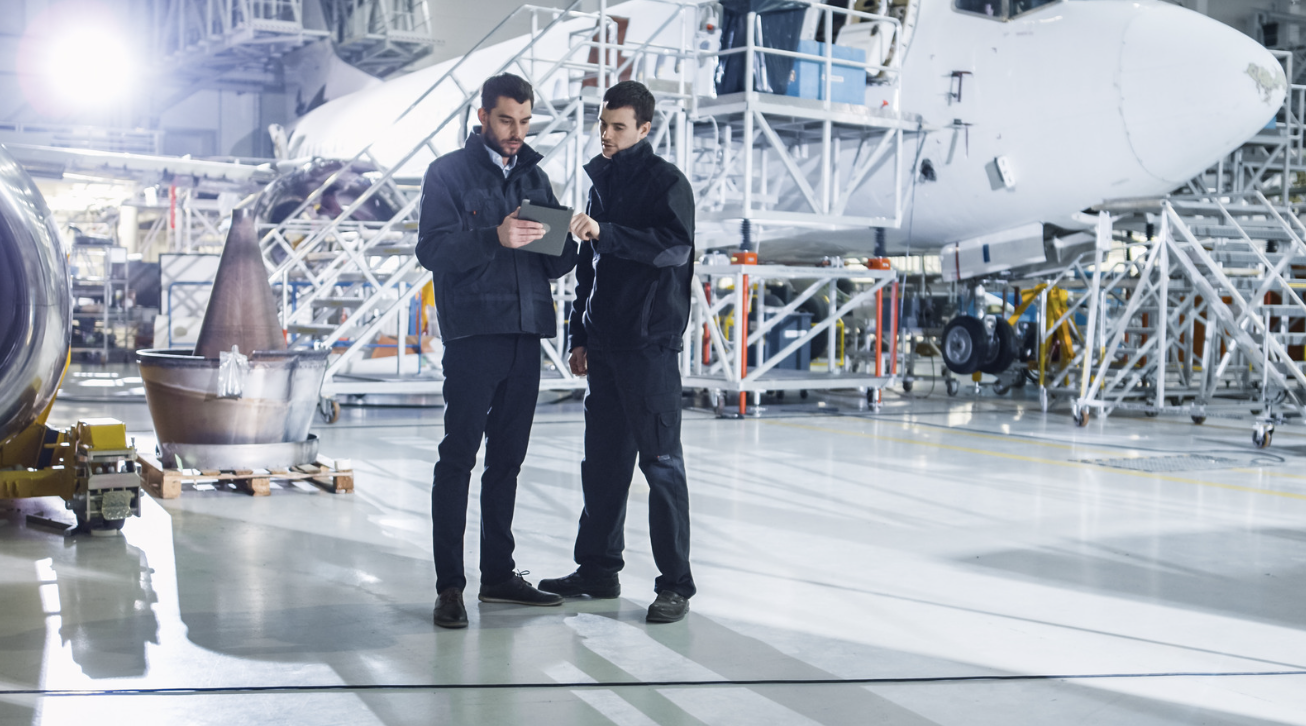
Case Study
Developing Smart Tools for the Airbus Factory
Manufacturing and assembly of aircraft, which involves tens of thousands of steps that must be followed by the operators, and a single mistake in the process could cost hundreds of thousands of dollars to fix, makes the room for error very small.
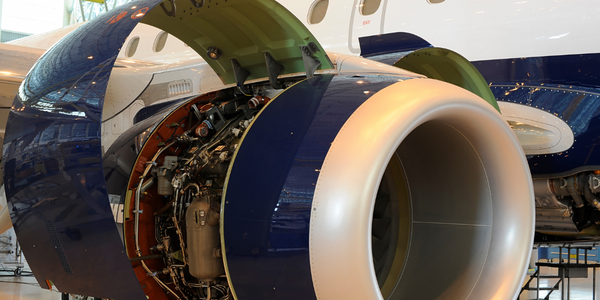
Case Study
Accelerate Production for Spirit AeroSystems
The manufacture and assembly of massive fuselage assemblies and other large structures generates a river of data. In fact, the bill of materials for a single fuselage alone can be millions of rows of data. In-house production processes and testing, as well as other manufacturers and customers created data flows that overwhelmed previous processes and information systems. Spirit’s customer base had grown substantially since their 2005 divestiture from Boeing, resulting in a $41 billion backlog of orders to fill. To address this backlog, meet increased customer demands and minimize additional capital investment, the company needed a way to improve throughput in the existing operational footprint. Spirit had a requirement from customers to increase fuselage production by 30%. To accomplish this goal, Spirit needed real-time information on its value chain and workflow. However, the two terabytes of data being pulled from their SAP ECC was unmanageable and overloaded their business warehouse. It had become time-consuming and difficult to pull aggregate data, disaggregate it for the needed information and then reassemble to create a report. During the 6-8 hours it took to build a report, another work shift (they run three per day) would have already taken place, thus the report content was out-of-date before it was ever delivered. As a result, supervisors often had to rely on manual efforts to provide charts, reports and analysis.