Download PDF
Vibrantz Leverages Alchemy's Chemistry Acceleration Software for Enhanced Customer Service and Project Management
Applicable Functions
- Sales & Marketing
Use Cases
- Time Sensitive Networking
- Track & Trace of Assets
Services
- Testing & Certification
The Challenge
Vibrantz, a company known for its commitment to constant improvement and exceptional customer service, was facing challenges in tracking projects, formulas, materials, testing, and feedback for their new development and technical service requests. The company was using outdated Sharepoint and Biovia lab notebook systems, which were not efficient enough to meet their growing needs. The technical service teams were handling thousands of color match requests and related lab work each year, but the process of capturing all formulation and test data was cumbersome and time-consuming. The company was also struggling with automating calculations, process steps, and approvals to speed up the end-to-end tech service process.
About The Customer
Vibrantz is a forward-thinking company that places a high value on constant improvement and exceptional customer service. As an early adopter of technology, the company is always on the lookout for innovative solutions that can enhance its operations and service delivery. Vibrantz's technical group handles a large volume of work each year, including thousands of color match requests and related lab work. The company is committed to delivering fast and accurate results to its customers, and to achieving this, it leverages advanced technologies like Alchemy’s Chemistry Acceleration Software.
The Solution
Vibrantz adopted Alchemy’s Chemistry Acceleration Software in February 2019 to overcome these challenges. The software enabled the company to track and manage their projects, formulas, materials, testing, and feedback more efficiently. The technical service teams started using Alchemy to track and manage thousands of color match requests and related lab work each year. The software also allowed them to capture all formulation and test data in one place, making it easy to filter and search to accelerate the process of hitting an exact match on future color requests. Alchemy’s software also automated calculations, process steps, and approvals, thereby accelerating the end-to-end tech service process. Vibrantz also streamlined the approvals process for custom formulation work and planned to expand the use of Alchemy to new product and technical service teams across North America, Europe, and APAC. They also planned to integrate Alchemy with Salesforce for a closed-loop tech service request and lab process that seamlessly connects the lab and sales team functions.
Operational Impact
Quantitative Benefit
Related Case Studies.
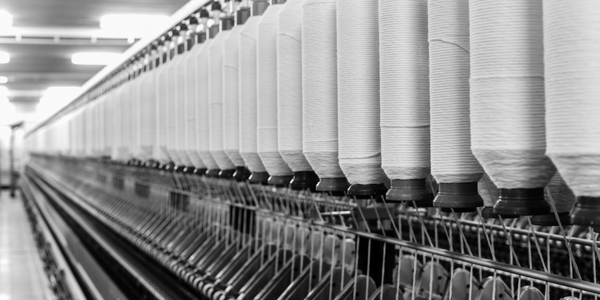
Case Study
IoT Applications and Upgrades in Textile Plant
At any given time, the textile company’s manufacturing facility has up to 2,000 textile carts in use. These carts are pushed from room to room, carrying materials or semi-finished products. Previously, a paper with a hand-written description was attached to each cart. This traditional method of processing made product tracking extremely difficult. Additionally, making sure that every cart of materials or semi-finished products went to its correct processing work station was also a problem. Therefore, the company desired an intelligent solution for tracking assets at their factories. They also wanted a solution that would help them collect process data so they could improve their manufacturing efficiency.
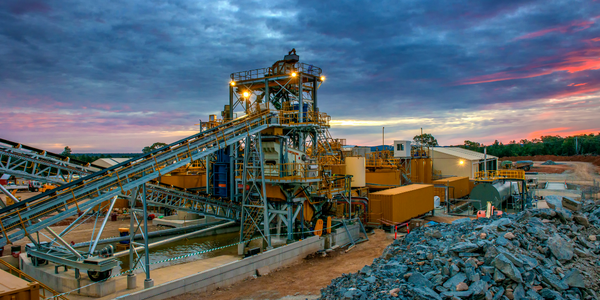
Case Study
Goldcorp: Internet of Things Enables the Mine of the Future
Goldcorp is committed to responsible mining practices and maintaining maximum safety for its workers. At the same time, the firm is constantly exploring ways to improve the efficiency of its operations, extend the life of its assets, and control costs. Goldcorp needed technology that can maximize production efficiency by tracking all mining operations, keep employees safe with remote operations and monitoring of hazardous work areas and control production costs through better asset and site management.
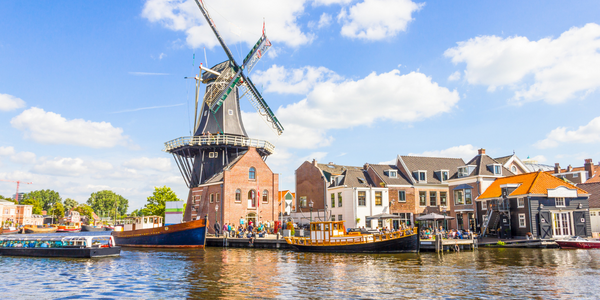
Case Study
Buoy Status Monitoring with LoRa
The Netherlands are well-known for their inland waterways, canals, sluices and of course port activities. The Dutch Ministry of Infrastructure indicates that there are thousands of buoys and fixed items in and near water environments that would profit from IoT monitoring. One of the problems with buoys for example, is that they get hit by ships and the anchor cable breaks. Without connectivity, it takes quite some time to find out that something has happened with that buoy. Not to mention the costs of renting a boat to go to the buoy to fix it. Another important issue, is that there is no real-time monitoring of the buoys at this moment. Only by physically visiting the object on the water, one gains insight in its status.
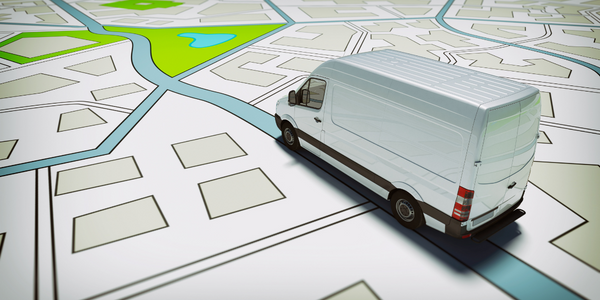
Case Study
IoT Based Asset Tracking System
The existing system used by the customer could only track a few thousand assets and was able to generate only a few standard set of reports. As the number of assets tracked grew exponentially, the system started to break at the seams. The Tracking devices were from different manufacturers following different protocols. There was no proper integration among the devices to send instant alerts. There are thousands of tracking devices spread across multiple geographies, that are moving. The configuration and troubleshooting of these devices incurred heavy costs, which was a logistics challenge. The existing system did not provide sophisticated Analytics, Business Intelligence and Insights from the data
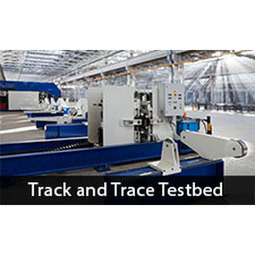
Case Study
IIC - Track and Trace Testbed
Factory systems can detect - within a meter - the location of a tool; Misuse of tools can result in serious accident or injury; The production of many industrial and consumer goods requires exacting work - down to the precise force used to tighten a screw. GOAL Manage smart, hand-held tools in manufacturing, maintenance, and industrial environments