Download PDF
Weisser Distributing Case Study
Technology Category
- Platform as a Service (PaaS) - Connectivity Platforms
Applicable Industries
- E-Commerce
- Retail
Applicable Functions
- Logistics & Transportation
- Warehouse & Inventory Management
Use Cases
- Inventory Management
- Supply Chain Visibility
Services
- System Integration
The Challenge
Weisser Distributing was looking for ways to speed up its fulfillment process, automate various manual processes and gain operational efficiencies. The company’s previous shipping software did not provide automated rate shopping and instead, warehouse employees were selecting shipping rates - resulting in unnecessarily high shipping costs. With a product mix of 11,000 SKUs, the company wanted an automated tool to relieve warehouse workers of “shipping fatigue” from having to decide the best shipping option per product/SKU and streamline the entire process. Moreover, the company had specific needs for shipping policies and rules to identify the best carrier to fit specific requirements, such as hazardous material and large, heavy products. Most importantly, Weisser Distributing needed a system that would integrate easily with NetSuite, its ERP solution. As the company operates out of two locations in South Dakota and Nevada, it needed consistent processes and communication channels to conduct fulfillment from multiple warehouses. With such a large product mix it was essential that product details and dimensions were automatically syncing to and from NetSuite.
About The Customer
Founded in 1978, Weisser Distributing provides eCommerce fulfillment services for dozens of marketplaces, including Amazon, Walmart, eBay, and Shopify. It has become one of the fastest growing employers in the Midwest, with headquarters in Sioux Falls, SD. The company operates out of two locations in South Dakota and Nevada, and has a product mix of 11,000 SKUs. Weisser Distributing was looking for ways to speed up its fulfillment process, automate various manual processes and gain operational efficiencies.
The Solution
ShipHawk’s Smart Packing and automated rate shopping delivered what Weisser Distributing needed most: every order is now shipped in the most efficient packaging, with the right carrier and correct service level, reducing “shipper fatigue” and saving time. “ShipHawk’s shipping rules ensure you’re searching for the best carrier and service level - so instead of relying on a worker to choose from up to 50 different carrier and shipping options, ShipHawk automatically filters based on customized shipping rules and tells the employee which carrier fits best,” said Warehouse Project Manager, Ann Traphagen. By reducing the average order processing time, ShipHawk delivers a faster, more efficient process. Once an item is fulfilled, ShipHawk creates the shipment fulfillment to be completed, with seamless communication with the warehouse picking technology. Additionally, ShipHawk identifies the recommended packing material, which reduces shippers’ time spent deciding how to deal with a new or unique product that needs to be packed.
Operational Impact
Related Case Studies.
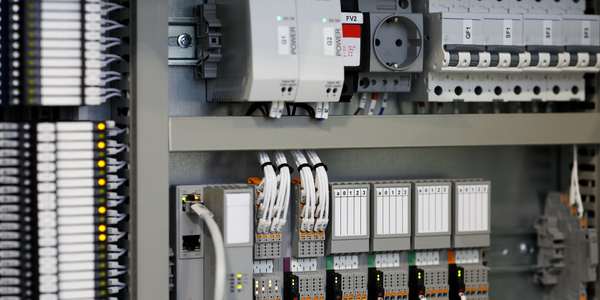
Case Study
Improving Production Line Efficiency with Ethernet Micro RTU Controller
Moxa was asked to provide a connectivity solution for one of the world's leading cosmetics companies. This multinational corporation, with retail presence in 130 countries, 23 global braches, and over 66,000 employees, sought to improve the efficiency of their production process by migrating from manual monitoring to an automatic productivity monitoring system. The production line was being monitored by ABB Real-TPI, a factory information system that offers data collection and analysis to improve plant efficiency. Due to software limitations, the customer needed an OPC server and a corresponding I/O solution to collect data from additional sensor devices for the Real-TPI system. The goal is to enable the factory information system to more thoroughly collect data from every corner of the production line. This will improve its ability to measure Overall Equipment Effectiveness (OEE) and translate into increased production efficiencies. System Requirements • Instant status updates while still consuming minimal bandwidth to relieve strain on limited factory networks • Interoperable with ABB Real-TPI • Small form factor appropriate for deployment where space is scarce • Remote software management and configuration to simplify operations
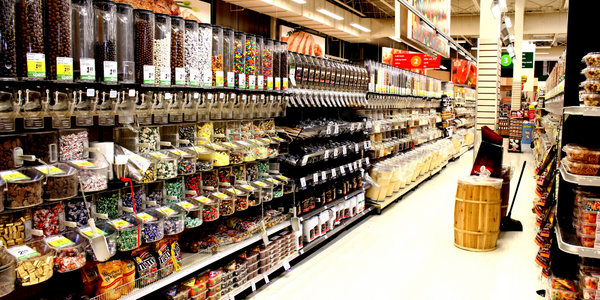
Case Study
How Sirqul’s IoT Platform is Crafting Carrefour’s New In-Store Experiences
Carrefour Taiwan’s goal is to be completely digital by end of 2018. Out-dated manual methods for analysis and assumptions limited Carrefour’s ability to change the customer experience and were void of real-time decision-making capabilities. Rather than relying solely on sales data, assumptions, and disparate systems, Carrefour Taiwan’s CEO led an initiative to find a connected IoT solution that could give the team the ability to make real-time changes and more informed decisions. Prior to implementing, Carrefour struggled to address their conversion rates and did not have the proper insights into the customer decision-making process nor how to make an immediate impact without losing customer confidence.
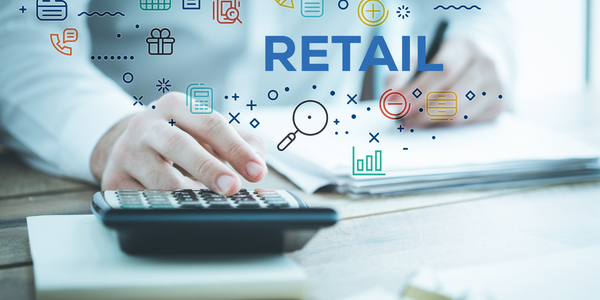
Case Study
Digital Retail Security Solutions
Sennco wanted to help its retail customers increase sales and profits by developing an innovative alarm system as opposed to conventional connected alarms that are permanently tethered to display products. These traditional security systems were cumbersome and intrusive to the customer shopping experience. Additionally, they provided no useful data or analytics.
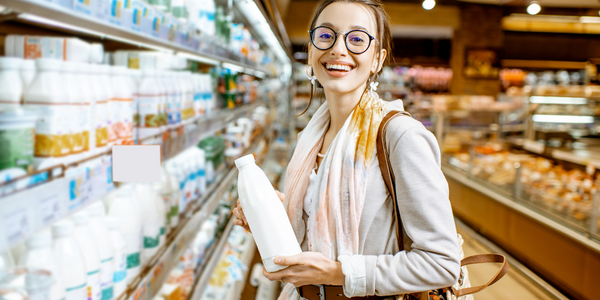
Case Study
Ensures Cold Milk in Your Supermarket
As of 2014, AK-Centralen has over 1,500 Danish supermarkets equipped, and utilizes 16 operators, and is open 24 hours a day, 365 days a year. AK-Centralen needed the ability to monitor the cooling alarms from around the country, 24 hours a day, 365 days a year. Each and every time the door to a milk cooler or a freezer does not close properly, an alarm goes off on a computer screen in a control building in southwestern Odense. This type of alarm will go off approximately 140,000 times per year, equating to roughly 400 alarms in a 24-hour period. Should an alarm go off, then there is only a limited amount of time to act before dairy products or frozen pizza must be disposed of, and this type of waste can quickly start to cost a supermarket a great deal of money.
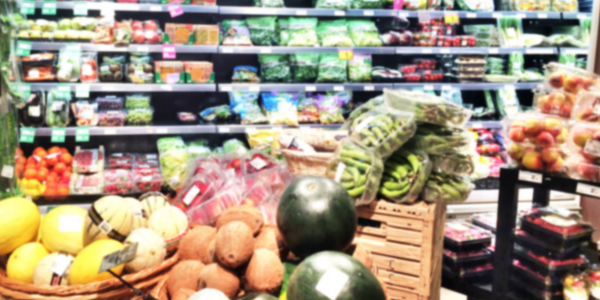
Case Study
Supermarket Energy Savings
The client had previously deployed a one-meter-per-store monitoring program. Given the manner in which energy consumption changes with external temperature, hour of the day, day of week and month of year, a single meter solution lacked the ability to detect the difference between a true problem and a changing store environment. Most importantly, a single meter solution could never identify root cause of energy consumption changes. This approach never reduced the number of truck-rolls or man-hours required to find and resolve issues.