Download PDF
Whole Latte Love: Shipping Thousands Of Packages Per Day
Technology Category
- Functional Applications - Enterprise Resource Planning Systems (ERP)
Applicable Industries
- Retail
Applicable Functions
- Logistics & Transportation
- Warehouse & Inventory Management
Use Cases
- Inventory Management
- Supply Chain Visibility
Services
- System Integration
The Challenge
Whole Latte Love, a specialty retailer of homemade coffee, was facing challenges with its home-grown ERP system. The company needed a configurable, cloud-based system to support its growth. However, the initial shipping software caused a six-week ERP deployment delay. The company needed a software that could strike the right balance between ready-to-use and easy-to-configure. The software needed to communicate automatically with the ERP without manual intervention. The company also wanted to improve productivity by eliminating manual keying in of orders and going outside the system to validate addresses.
About The Customer
Whole Latte Love is a specialty retailer of all things homemade coffee. The company offers a wide range of products related to brewing, filtering, and the coffee beans themselves. It is a one-stop shop for coffee lovers. The company has been in the e-commerce business since before the age of high-speed internet. As such, it had a home-grown ERP system in place. However, as the company grew, it realized the need for a more configurable, cloud-based system. The company chose Acumatica as its solution. However, the journey to implementation was not linear, and the company faced several challenges along the way.
The Solution
Whole Latte Love found the solution to its challenges in Pacejet, a Fulfilled by Acumatica shipping software. The software was able to draw information from, and write back to, the ERP without manual intervention. This eliminated the need for manual keying in of orders and going outside the system to validate addresses, thereby improving productivity. With the implementation of Pacejet, the company was able to improve throughput by almost 30%, reduce the time needed to process complex orders by over 50%, and increase its capacity to ship thousands of packages per day. The company is now exploring ways to capture international demand, make shipping less expensive and more efficient for larger products and orders using more LTL freight carriers, and efficiently scale.
Operational Impact
Quantitative Benefit
Related Case Studies.
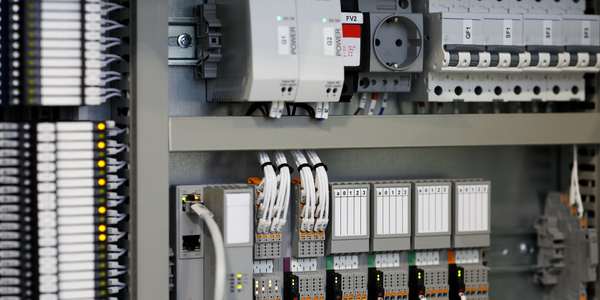
Case Study
Improving Production Line Efficiency with Ethernet Micro RTU Controller
Moxa was asked to provide a connectivity solution for one of the world's leading cosmetics companies. This multinational corporation, with retail presence in 130 countries, 23 global braches, and over 66,000 employees, sought to improve the efficiency of their production process by migrating from manual monitoring to an automatic productivity monitoring system. The production line was being monitored by ABB Real-TPI, a factory information system that offers data collection and analysis to improve plant efficiency. Due to software limitations, the customer needed an OPC server and a corresponding I/O solution to collect data from additional sensor devices for the Real-TPI system. The goal is to enable the factory information system to more thoroughly collect data from every corner of the production line. This will improve its ability to measure Overall Equipment Effectiveness (OEE) and translate into increased production efficiencies. System Requirements • Instant status updates while still consuming minimal bandwidth to relieve strain on limited factory networks • Interoperable with ABB Real-TPI • Small form factor appropriate for deployment where space is scarce • Remote software management and configuration to simplify operations
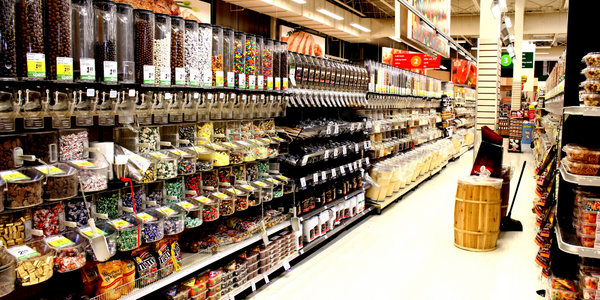
Case Study
How Sirqul’s IoT Platform is Crafting Carrefour’s New In-Store Experiences
Carrefour Taiwan’s goal is to be completely digital by end of 2018. Out-dated manual methods for analysis and assumptions limited Carrefour’s ability to change the customer experience and were void of real-time decision-making capabilities. Rather than relying solely on sales data, assumptions, and disparate systems, Carrefour Taiwan’s CEO led an initiative to find a connected IoT solution that could give the team the ability to make real-time changes and more informed decisions. Prior to implementing, Carrefour struggled to address their conversion rates and did not have the proper insights into the customer decision-making process nor how to make an immediate impact without losing customer confidence.
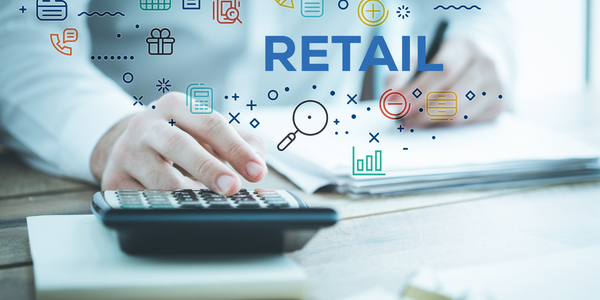
Case Study
Digital Retail Security Solutions
Sennco wanted to help its retail customers increase sales and profits by developing an innovative alarm system as opposed to conventional connected alarms that are permanently tethered to display products. These traditional security systems were cumbersome and intrusive to the customer shopping experience. Additionally, they provided no useful data or analytics.
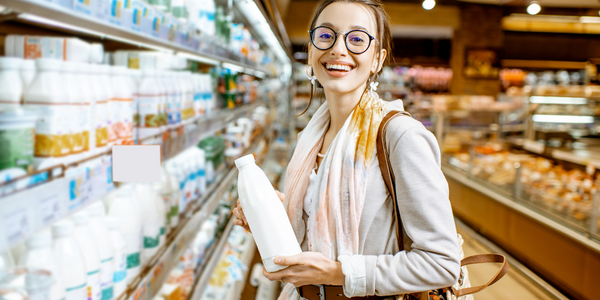
Case Study
Ensures Cold Milk in Your Supermarket
As of 2014, AK-Centralen has over 1,500 Danish supermarkets equipped, and utilizes 16 operators, and is open 24 hours a day, 365 days a year. AK-Centralen needed the ability to monitor the cooling alarms from around the country, 24 hours a day, 365 days a year. Each and every time the door to a milk cooler or a freezer does not close properly, an alarm goes off on a computer screen in a control building in southwestern Odense. This type of alarm will go off approximately 140,000 times per year, equating to roughly 400 alarms in a 24-hour period. Should an alarm go off, then there is only a limited amount of time to act before dairy products or frozen pizza must be disposed of, and this type of waste can quickly start to cost a supermarket a great deal of money.
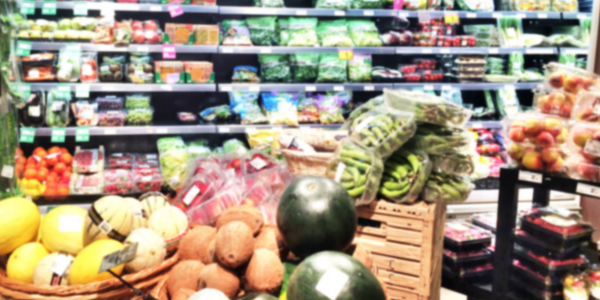
Case Study
Supermarket Energy Savings
The client had previously deployed a one-meter-per-store monitoring program. Given the manner in which energy consumption changes with external temperature, hour of the day, day of week and month of year, a single meter solution lacked the ability to detect the difference between a true problem and a changing store environment. Most importantly, a single meter solution could never identify root cause of energy consumption changes. This approach never reduced the number of truck-rolls or man-hours required to find and resolve issues.