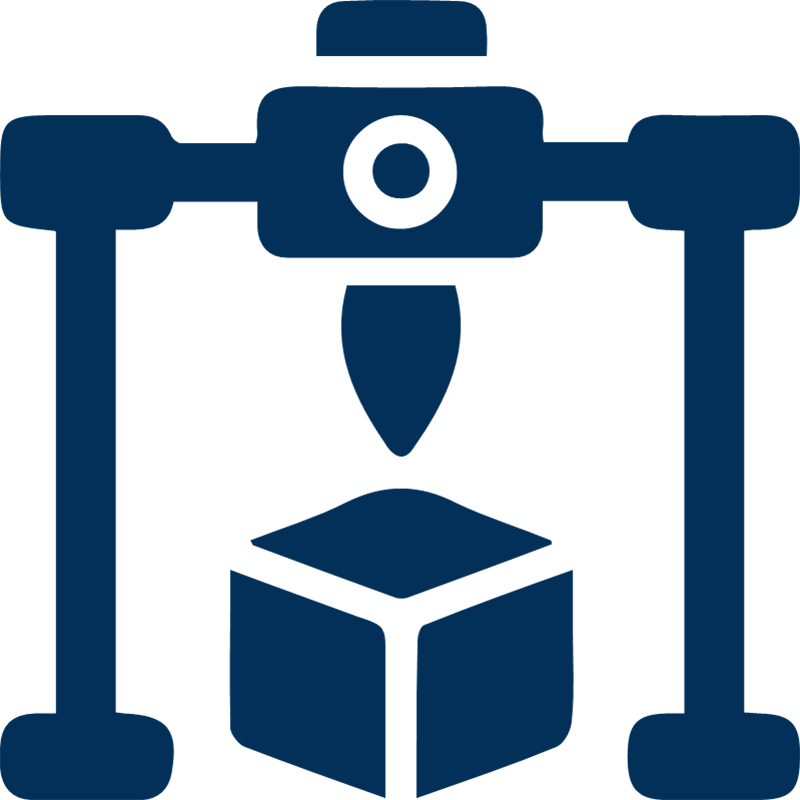
Additive Manufacturing
Additive manufacturing (AM) is one use case for 3D printing technology. The other primary use case is rapid prototyping. Both use cases refer to the processes of synthesizing a three-dimensional object from successive layers of material. These objects can be of almost any shape or geometry and are produced from a 3D model or other data source. Additive Manufacturing is currently much less common than rapid prototyping due to the higher standards for quality and cost competitiveness. It is relatively expensive and time consumptive to produce a prototype using traditional manufacturing technologies. 3D printers can dramatically cut both the cost and time in many cases. And the quality of a prototype can generally be below that of a finished product. In contrast, traditional manufacturing technology is excellent at mass-producing finished products. For this reason, Additive Manufacturing is currently used primarily to produce customized products, small batches of replacement components, and designs that are particularly challenging for traditional manufacturing processes.
- Automotive
- Transportation
- Product Development
The additive manufacturing and rapid prototyping industry are expected to reach over USD 20 billion by 2020.
Source: Capstone Headwaters
The overall 3D printing market is expected to grow from USD 9.9 billion in 2018 to USD 34.8 billion by 2024, at a CAGR of 23.25%.
Source: Markets & Markets
IDTechEx forecasts that the global market for 3D printing equipment, materials, software, and services is estimated to be worth USD 22 billion by the year 2028.
Source: IDTechEX
PR Newswire forecasts the global metal additive manufacturing market to grow at a CAGR of 21.36% during the period 2018-2022.
Source: PR Newswire
What is the main business value of additive manufacturing (AM)?
The radically different production process enables the production of highly customized items on demand. Benefits include:
1. Mass Customization: With 3D printing, it is possible to produce low-volume batches down to a size of one. The economics of producing one product is the same as producing 100 or 1,000. Thus, AM can be applied when customization or small batches are required.
2. Creating complex components: With 3D printing, it is possible to create shapes that can't be made by molding or machining. For example, new classes of physical, bio, and chemical sensors can all be fabricated via 3D printing technology. Companies are also experimenting with printed organs that are built from the cells of the recipient.
3. Greener manufacturing: There are potential environmental benefits for 3D printing, which eliminates the transportation of components (often across thousands of miles). However, we cannot yet compare the environmental impact of traditional mass manufacturing against mass additive manufacturing.
What are the key specifications that additive manufacturing systems are rated?
Key specifications include quality of the end product, production rates (cycle time), dimensional precision, color merging & range, and the number of scraps.
1. Organizations and Departments Allocating Budgets: Additive manufacturing initiatives often require substantial investment, prompting various organizations and departments to play a role in decision-making. In larger enterprises, the decision-making process may involve multiple departments, each with its own focus. For instance, the engineering department might prioritize selecting suitable printing materials, while the procurement team focuses on sourcing printers. In smaller businesses, the responsibility may fall on a single department or even an individual, depending on the scale of the project.
2. Operators and Maintainers: The responsibility for operating and maintaining additive manufacturing systems typically lies within the organizations that own them. This could involve dedicated personnel within the engineering or production departments, tasked with ensuring the smooth operation of printers, post-processing equipment, and associated software.
3. Regular Users: The primary users of additive manufacturing systems are often the employees directly involved in the design, prototyping, and production processes. Engineers, designers, and production staff interact with AM systems on a daily basis to bring their concepts to life.
4. External Stakeholders Benefiting from AM Data: While the sharing of additive manufacturing data with external stakeholders may not be as common as with AMI systems, there are still potential beneficiaries. For instance, suppliers and partners in the supply chain may gain insights into production schedules and part availability, enabling better coordination. Additionally, research institutions and regulatory bodies may benefit from access to AM data for quality control and standards development purposes.
5. Innovators and Investors: Much like in the energy sector, there's a burgeoning interest among startups and investors in leveraging additive manufacturing data. Marketplaces for 3D printing services, material suppliers, and software developers are emerging, driven by the potential of AM data to inform business decisions and shape investment strategies.
1. Edge Deployment: The "edge" in additive manufacturing is defined by the deployment of sensors and control systems within the production environment. These sensors can be strategically placed on individual printers, robotic arms, or even directly within the printed parts themselves. As deployment moves closer to the point of manufacturing, such as within a 3D printer's build chamber, the granularity of data improves, allowing for real-time monitoring and control of the printing process.
2. Sensors for Data Acquisition: Various sensors are utilized in additive manufacturing to provide critical data into the IoT (Internet of Things) ecosystem. These may include temperature sensors, humidity sensors, laser displacement sensors, and cameras for monitoring print quality. Factors defining their deployment include the need for accuracy, reliability, and durability in harsh manufacturing environments. Quality assurance is paramount, as low-quality sensors can compromise the integrity of the printing process and result in defective parts.
3. Systems Utilizing AM Data: Additive manufacturing data feeds into a range of systems designed to optimize production processes and ensure quality control. For instance, Computer-Aided Manufacturing (CAM) software utilizes AM data to generate toolpaths for printers, optimizing print times and material usage. Quality management systems leverage AM data to track part traceability and ensure compliance with industry standards and regulations.
4. Connectivity Solutions: Connectivity technologies play a crucial role in facilitating device-to-device and device-to-cloud communication within additive manufacturing ecosystems. Solutions such as wireless communication protocols and industrial Ethernet enable seamless data transfer between printers, control systems, and cloud-based analytics platforms. Factors defining connectivity solutions include reliability, data throughput, scalability, and total infrastructure cost. Robust wireless communication technologies are essential to support the growing complexity and scale of additive manufacturing operations.
What data is required to enable additive manufacturing?
The design must be transmitted through CAD software to the printer. There is a wide range of professional grade and free software available for both the design and transmission of data.
A growing number of software products enable design in collaboration with machine learning algorithms. These algorithms generate, test, and iterate thousands of designs to meet performance specifications provided for the end product. When machine learning is deployed, it can often be useful to seed the system with data sets in order to guide the development process.
What challenges constrain the use of additive manufacturing?
Common feasibility challenges include:
1. The high cost of 3D printing equipment: Equipment remains costly and many companies do not have sufficiently high uptime to maximize the value of their equipment.
2. The limited number of materials available and limitations on the ability to use different materials in the same design.
3. Post-processing requirements: In some cases post-processing can be expensive and require additional tooling.
4. The time required to print each component: At this point, the time and cost required to make one part may not be sustainable for a full fabrication project. 3D printing is not a substitute for precision machining centers and machinery that produce high-quality products in a timely manner.
5. Lack of formal standards: The lack of standards constrains the use of design data across different software programs or machines.
6. Lack of expertise and training: Few designers have a comprehensive understanding of both how to design using 3D printing software and the practical considerations that make additive manufacturing before or worse than traditional manufacturing in a specific case.
Case Studies.
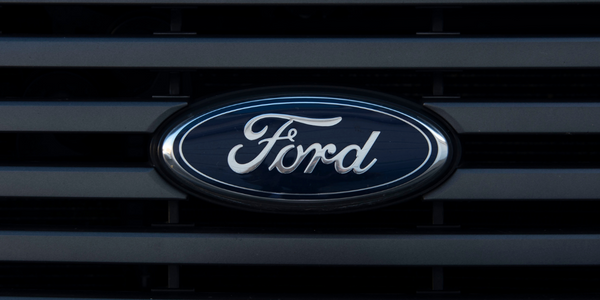
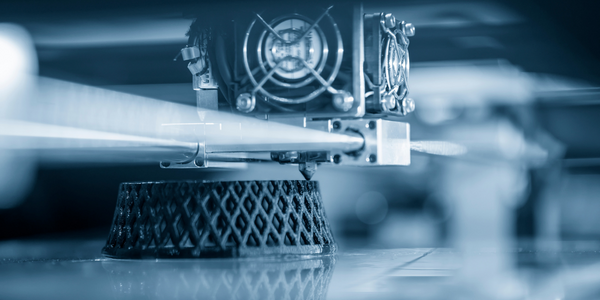