Download PDF
A ruAN Logistics pArtNership Adds VALue to BoBcAt, Keeps compANy ruNNiNg LeAN
Technology Category
- Functional Applications - Inventory Management Systems
- Functional Applications - Remote Monitoring & Control Systems
- Networks & Connectivity - Network Management & Analysis Software
Applicable Industries
- Construction & Infrastructure
- Agriculture
Applicable Functions
- Logistics & Transportation
- Warehouse & Inventory Management
Use Cases
- Fleet Management
- Predictive Maintenance
- Track & Trace of Assets
Services
- System Integration
- Training
The Challenge
Bobcat faced several logistical challenges with its three manufacturing facilities in the United States. The company shipped equipment directly from these facilities to dealers, leading to inefficiencies such as multiple shipments arriving at dealers on the same day, tying up dealer staff. Additionally, Bobcat was limited by the number of trucking carriers willing to bid on work due to the remote locations of its facilities. Deliveries were often late, and tracking the specific location of shipments was difficult. Other challenges included less-than-load (LTL) deliveries, where Bobcat was charged for full truckloads despite the trucks not being fully loaded, leading to increased costs. The system was inefficient, and dealers demanded a better solution to improve service and reduce costs.
About The Customer
Bobcat Company is a leading manufacturer of construction, landscaping, and agricultural equipment, including skid-steer loaders and compact excavators. The company operates three manufacturing facilities in the United States, located in Gwinner, North Dakota; Bismarck, North Dakota; and Litchfield, Minnesota. Bobcat's customers rely on its equipment to complete their work and meet deadlines, making timely delivery of products crucial. To address logistical challenges and improve overall manufacturing efficiency, Bobcat partnered with Ruan, a logistics and transportation management company. This partnership aimed to streamline Bobcat's delivery processes, reduce costs, and enhance customer satisfaction by ensuring that equipment reached dealers promptly and in optimal condition.
The Solution
Bobcat partnered with Ruan to address its logistical challenges by utilizing the Ruan Consolidation and Distribution Center (RCDC) in Brooklyn Park, Minnesota. Ruan developed a 'merge in transit' solution, where all Bobcat products headed to dealers east of North Dakota are routed to the RCDC. At the RCDC, products are scanned into an inventory system, and Ruan uses routing software to build efficient loads based on inventory and dealer orders. The software considers various criteria, such as dealership operating hours, distance between dealers, and payload factor, to determine the most efficient transportation routes. This system has eliminated less-than-load (LTL) deliveries, increased payload factors, and ensured that attachments and machines are shipped together, reducing costs and improving delivery times. Additionally, Bobcat owns the trucks that transport products to the RCDC and uses them to bring inbound raw materials back to the manufacturing plants, further reducing transportation costs. The partnership has also increased the number of carriers willing to bid on Bobcat transportation, as products are now shipped from a more accessible location in Minneapolis. Ruan manages the loads and negotiates with carriers to secure the best rates, while the Ruan track and trace system provides real-time visibility of shipments, improving communication with dealers and ensuring timely deliveries.
Operational Impact
Quantitative Benefit
Related Case Studies.
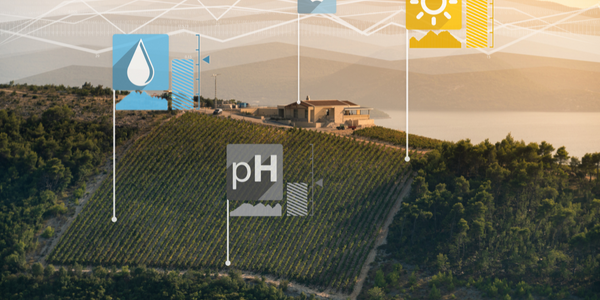
Case Study
Intelligent Farming with ThingWorx Analytics
Z Farms was facing three challenges: costly irrigation systems with water as a limited resource, narrow optimal ranges of soil moisture for growth with difficult maintenance and farm operators could not simply turn on irrigation systems like a faucet.
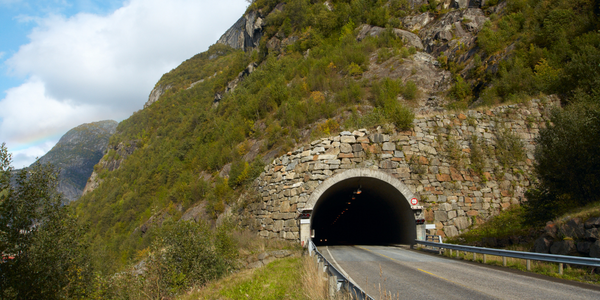
Case Study
IoT System for Tunnel Construction
The Zenitaka Corporation ('Zenitaka') has two major business areas: its architectural business focuses on structures such as government buildings, office buildings, and commercial facilities, while its civil engineering business is targeted at structures such as tunnels, bridges and dams. Within these areas, there presented two issues that have always persisted in regard to the construction of mountain tunnels. These issues are 'improving safety" and "reducing energy consumption". Mountain tunnels construction requires a massive amount of electricity. This is because there are many kinds of electrical equipment being used day and night, including construction machinery, construction lighting, and ventilating fan. Despite this, the amount of power consumption is generally not tightly managed. In many cases, the exact amount of power consumption is only ascertained when the bill from the power company becomes available. Sometimes, corporations install demand-monitoring equipment to help curb the maximum power demanded. However, even in these cases, the devices only allow the total volume of power consumption to be ascertained, or they may issue warnings to prevent the contracted volume of power from being exceeded. In order to tackle the issue of reducing power consumption, it was first necessary to obtain an accurate breakdown of how much power was being used in each particular area. In other words, we needed to be able to visualize the amount of power being consumed. Safety, was also not being managed very rigorously. Even now, tunnel construction sites often use a 'name label' system for managing entry into the work site. Specifically, red labels with white reverse sides that bear the workers' names on both sides are displayed at the tunnel work site entrance. The workers themselves then flip the name label to the appropriate side when entering or exiting from the work site to indicate whether or not they are working inside the tunnel at any given time. If a worker forgets to flip his or her name label when entering or exiting from the tunnel, management cannot be performed effectively. In order to tackle the challenges mentioned above, Zenitaka decided to build a system that could improve the safety of tunnel construction as well as reduce the amount of power consumed. In other words, this new system would facilitate a clear picture of which workers were working in each location at the mountain tunnel construction site, as well as which processes were being carried out at those respective locations at any given time. The system would maintain the safety of all workers while also carefully controlling the electrical equipment to reduce unnecessary power consumption. Having decided on the concept, our next concern was whether there existed any kind of robust hardware that would not break down at the construction work site, that could move freely in response to changes in the working environment, and that could accurately detect workers and vehicles using radio frequency identification (RFID). Given that this system would involve many components that were new to Zenitaka, we decided to enlist the cooperation of E.I.Sol Co., Ltd. ('E.I.Sol') as our joint development partner, as they had provided us with a highly practical proposal.
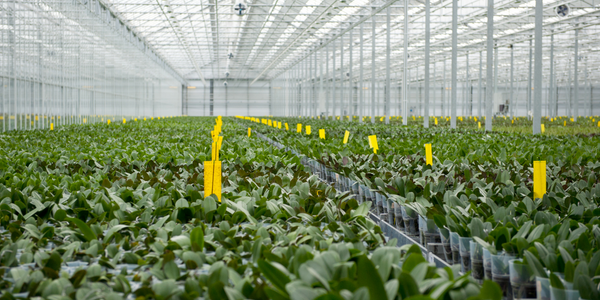
Case Study
Greenhouse Intelligent Monitoring and Control Solution
Farming Orchids is the most successful form of precision farming in Taiwan, and also the most exported flower. Orchids need a specific temperature and humidity conditions to grow and bloom, and its flowering time may not be in line with market demands, so the price collapses when there is overproduction. Therefore, some farmers began to import automated greenhouse control systems for breeding and forcing, which not only improves quality, but also effectively controls the production period and yield to ensure revenue. In 2012, an orchid farmer built a Forcing Greenhouse of about 200 pings (approximately 661 Square Meters) in Tainan, Taiwan. The system integrator adopted Advantech’s APAX-5000 series programmable automation controllers to build the control platform, coupled with Advantech WebAccess HMI/SCADA software, to achieve cloud monitoring. The staff of the orchid field can monitor important data anytime via smart phone, iPad, and other handheld devices, and control the growth and flowering conditions. System requirements: In the past, most environmental control systems of orchid greenhouses in Taiwan used PLCs (Programmable Logic Controller) with poorscalability and control, and could not be connected to the Internet formonitoring from the cloud. For advanced database analysis and networking capability, the PC platform must be adopted. Therefore, PAC Systems (Programmable Automation Controller) with both PLC programming capabilities andPC functions is a better choice.The environmental control of the Orchid greenhouse switches on and off devices like fan, shade net, cooling/heat pump, liquid flow control, water-cooling wall etc. It is controlled by a control panel of electric controllers, and is driven by a motor, to adjust the greenhouse temperature, humidity, and other environmental conditions to the set parameters.
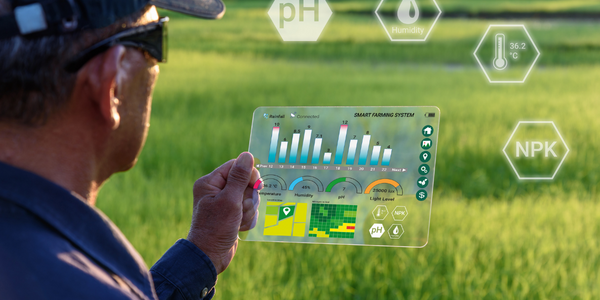
Case Study
Enabling Internet of Things Innovation in Agriculture
DigiBale, wanted to apply technology know-how and IP from implementations successfully to more agriculture sectors including cotton, forestry, sugarcane and cattle. However, farmers and growers still have worries about the connected technology.