Download PDF
Achieves efficient accurate cost control with Lectra technology
Technology Category
- Functional Applications - Product Lifecycle Management Systems (PLM)
Applicable Industries
- Apparel
- Consumer Goods
Applicable Functions
- Product Research & Development
- Quality Assurance
Use Cases
- Predictive Quality Analytics
- Digital Twin
- Remote Collaboration
Services
- Software Design & Engineering Services
- System Integration
The Challenge
Lise Charmel Lingerie, known for its high-quality French embroidery and innovative textiles, faced challenges in controlling costs and fabric consumption. The intricate details of embroidered and lace bands required precise placement to minimize waste. The company sought a way to estimate lace and fabric consumption more accurately and easily to maintain quality while keeping costs reasonable.
About The Customer
Lise Charmel is a renowned lingerie brand that combines the beauty and elegance of French embroidery with innovative textiles. The company is known for its high-quality materials, which are essential for creating unique and sophisticated lingerie. However, these materials are also very expensive, making cost control and fabric consumption a high priority. Lise Charmel has been a long-time user of Lectra technology and has recently implemented the latest version of Lectra's pre-costing and production marker solution, Diamino, to improve efficiency and accuracy in their production processes.
The Solution
Lise Charmel combined Lectra solutions with a smart process to estimate initial costs accurately early in the design and development phases. The teams can now lay pattern pieces out on lace and other fabrics virtually for material estimation purposes. This visual approach has significantly improved the marker-making process, allowing for better usability and time savings. The ability to visualize different piece and fabric placement options directly on the fabric has radically changed the process, making it more reliable and efficient. The new process has also improved communication between different departments, allowing for quicker exchanges and problem-solving.
Operational Impact
Quantitative Benefit
Related Case Studies.
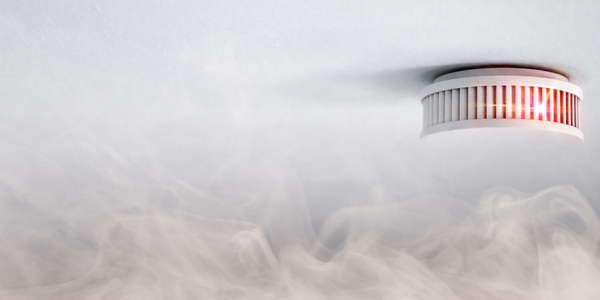
Case Study
Fire Alarm System and Remote Monitoring Sytem
Fire alarm systems are essential in providing an early warning in the event of fire. They help to save lives and protect property whilst also fulfilling the needs of insurance companies and government departments.Fire alarm systems typically consist of several inter-linked components, such as smoke detectors, heat detector, carbon monoxide, manual call points, sounders, alarm and buzzer. The fire alarm system should give immediate information in order to prevent the fire spread and protect live and property.To get maximum protection a shoe manufacturer in Indonesia opted for a new fire alarm system to monitor 13 production sites spread over 160 hectars. Although the company had an existing fire alarm system, it could not be monitored remotely.It was essential that the new system would be able to be monitored from a central control room. It needed to be able to connect to the existing smoke detector and manual call point. Information should be easily collected and passed on to the Supervisory Control and Data Acquisition (SCADA) system. Furthermore, the system should have several features such as alarm management, auto reporting, being connected to many client computers without additional cost, and run 24/7 without fails. The company also needed a system which could be implemented without changing the architecture of the existing fire alarm system.
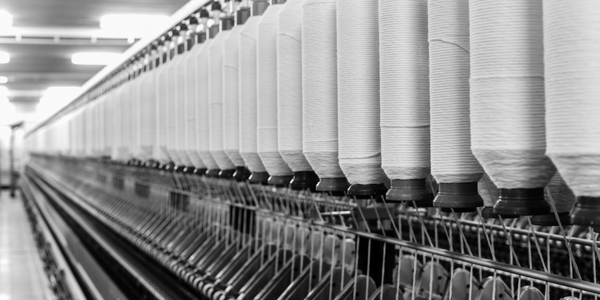
Case Study
IoT Applications and Upgrades in Textile Plant
At any given time, the textile company’s manufacturing facility has up to 2,000 textile carts in use. These carts are pushed from room to room, carrying materials or semi-finished products. Previously, a paper with a hand-written description was attached to each cart. This traditional method of processing made product tracking extremely difficult. Additionally, making sure that every cart of materials or semi-finished products went to its correct processing work station was also a problem. Therefore, the company desired an intelligent solution for tracking assets at their factories. They also wanted a solution that would help them collect process data so they could improve their manufacturing efficiency.
.png)
Case Study
Improving Vending Machine Profitability with the Internet of Things (IoT)
The vending industry is undergoing a sea change, taking advantage of new technologies to go beyond just delivering snacks to creating a new retail location. Intelligent vending machines can be found in many public locations as well as company facilities, selling different types of goods and services, including even computer accessories, gold bars, tickets, and office supplies. With increasing sophistication, they may also provide time- and location-based data pertaining to sales, inventory, and customer preferences. But at the end of the day, vending machine operators know greater profitability is driven by higher sales and lower operating costs.
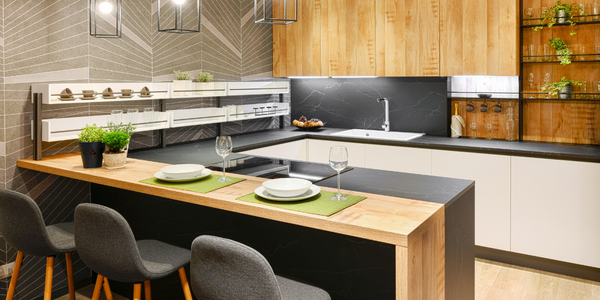
Case Study
Series Production with Lot-size-1 Flexibility
Nobilia manufactures customized fitted kitchens with a lot size of 1. They require maximum transparency of tracking design data and individual processing steps so that they can locate a particular piece of kitchen furniture in the sequence of processes.

Case Study
Retailer Uses RFID Scanner to Improve Efficiency
Patrizia Pepe wished to improve the logistics of their warehouse: accepting incoming goods from their production sites, movement of items throughout
the warehouse, and packaging of goods for distribution to the retail locations. They initially tried to use barcodes for this function. Because barcodes must be individually scanned within a line-of-sight, the acceptance of goods coming into the warehouse was too time consuming. Working with the University of Florence, Patrizia Pepe instituted a five-month pilot project beginning in August of 2009 to test the validity of an RFID solution. The pilot involved tagging of about 60,000 items for the second seasonal collection, and convinced the company to move forward with tagging all items.