Download PDF
Nikko Chemicals' Secure Cloud Migration with Data-Driven Approach
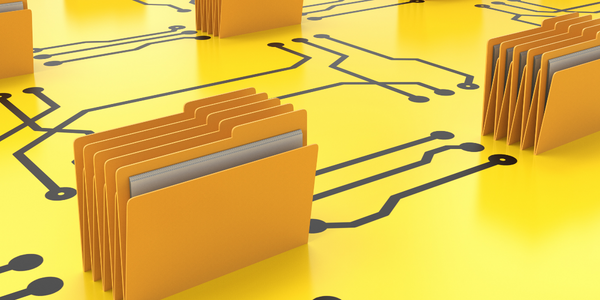
Technology Category
- Platform as a Service (PaaS) - Application Development Platforms
- Sensors - Chemical Sensors
Applicable Industries
- Chemicals
- Pharmaceuticals
Applicable Functions
- Maintenance
Use Cases
- Supply Chain Visibility
- Tamper Detection
Services
- Cloud Planning, Design & Implementation Services
- System Integration
The Challenge
Nikko Chemicals, a specialty chemicals manufacturer in Japan, was facing several challenges in its cloud operations. The company was struggling with the time-consuming integration of logs from disparate sources, which resulted in restricted operational visibility. There were also security concerns related to cloud migration and the management of Software as a Service (SaaS) applications. Additionally, the company had limited manpower and resources for managing its cloud infrastructure. These challenges were hindering the company's business continuity strategy, which aimed to run a secure, scalable, hassle-free, and fully visible cloud operation.
The Customer
Nikko Chemicals
About The Customer
Nikko Chemicals is a specialty chemicals manufacturer based in Japan. The company produces ingredients for cosmetics, pharmaceuticals, food, and sustainable products. As a responsible corporate citizen, Nikko Chemicals works to balance both environmental and economic considerations. The company is committed to running a secure, scalable, hassle-free, and fully visible cloud operation as part of its business continuity strategy. In response to the Great East Japan Earthquake and the subsequent tsunamis in 2011, Nikko Chemicals initiated a cloud migration initiative for better business continuity planning.
The Solution
To overcome these challenges, Nikko Chemicals deployed Splunk®, a software platform that provides real-time operational intelligence. The company replaced its on-premises infrastructures with SaaS applications running on Amazon Web Services (AWS) to minimize damage and speed recovery during disasters. The Splunk platform improved operational visibility across the organization and enabled a small team at Nikko Chemicals to manage multiple SaaS applications through a user-friendly and highly visualized interface. With Splunk, Nikko Chemicals could easily collect security-related logs from a wide range of applications to unify visibility across all its SaaS deployments. Log monitoring was now on a 24/7 basis, and log analysis was done through an external security operations center (SOC) service. This allowed Nikko Chemicals to automatically detect unanticipated outliers and respond to events in real time.
Operational Impact
Quantitative Benefit
Related Case Studies.
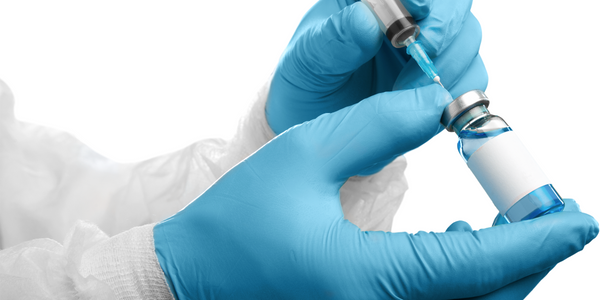
Case Study
Case Study: Pfizer
Pfizer’s high-performance computing software and systems for worldwide research and development support large-scale data analysis, research projects, clinical analytics, and modeling. Pfizer’s computing services are used across the spectrum of research and development efforts, from the deep biological understanding of disease to the design of safe, efficacious therapeutic agents.
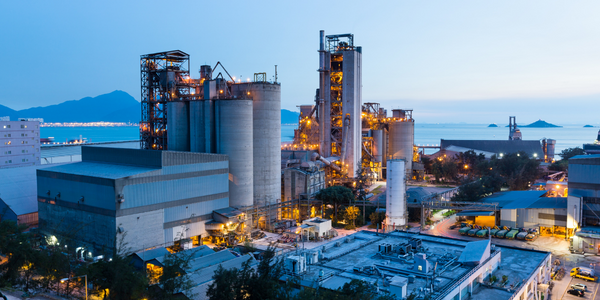
Case Study
Honeywell - Tata Chemicals Improves Data Accessibility with OneWireless
Tata was facing data accessibility challenges in the cement plant control room tapping signals from remote process control areas and other distant locations, including the gas scrubber. Tata needed a wireless solution to extend its control network securely to remote locations that would also provide seamless communication with existing control applications.
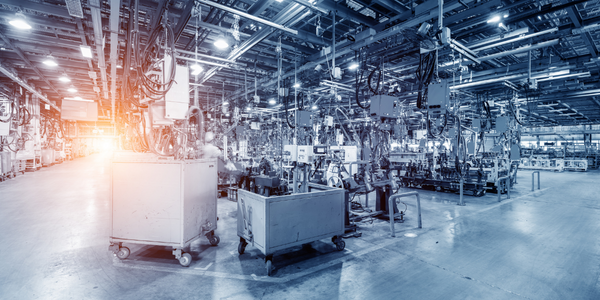
Case Study
Advanced Elastomer Systems Upgrades Production
In order to maintain its share of the international market for thermoplastic elastomers AES recently expanded its Florida plant by adding a new production line. While the existing lines were operating satisfactorily using a PROVOX distributed control system with traditional analog I/O, AES wanted advanced technology on the new line for greater economy, efficiency, and reliability. AES officials were anxious to get this line into production to meet incoming orders, but two hurricanes slowed construction.
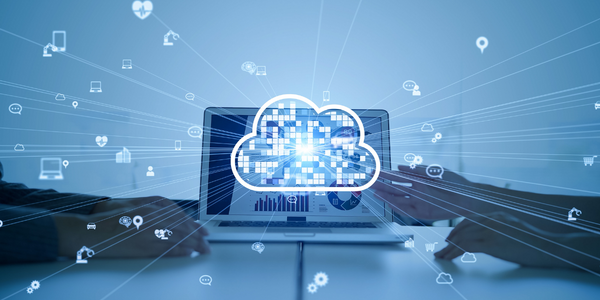
Case Study
Fusion Middleware Integration on Cloud for Pharma Major
Customer wanted a real-time, seamless, cloud based integration between the existing on premise and cloud based application using SOA technology on Oracle Fusion Middleware Platform, a Contingent Worker Solution to collect, track, manage and report information for on-boarding, maintenance and off-boarding of contingent workers using a streamlined and Integrated business process, and streamlining of integration to the back-end systems and multiple SaaS applications.
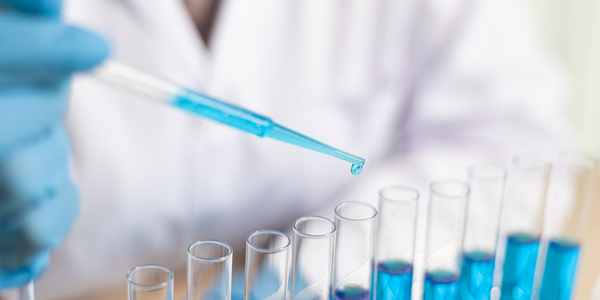
Case Study
Process Control System Support
In many automated production facilities, changes are made to SIMATIC PCS 7 projects on a daily basis, with individual processes often optimised by multiple workers due to shift changes. Documentation is key here, as this keeps workers informed about why a change was made. Furthermore, SIMATIC PCS 7 installations are generally used in locations where documentation is required for audits and certification. The ability to track changes between two software projects is not only an invaluable aid during shift changes, but also when searching for errors or optimising a PCS 7 installation. Every change made to the system is labour-intensive and time-consuming. Moreover, there is also the risk that errors may occur. If a change is saved in the project, then the old version is lost unless a backup copy was created in advance. If no backup was created, it will no longer be possible to return to the previous state if and when programming errors occur. Each backup denotes a version used by the SIMATIC PCS 7 system to operate an installation. To correctly interpret a version, information is required on WHO changed WHAT, WHERE, WHEN and WHY: - Who created the version/who is responsible for the version? - Who released the version? - What was changed in the version i.e. in which block or module of the SIMATIC PCS 7 installation were the changes made? - When was the version created? Is this the latest version or is there a more recent version? - Why were the changes made to the version? If they are part of a regular maintenance cycle, then is the aim to fix an error or to improve production processes? - Is this particular version also the version currently being used in production? The fact that SIMATIC PCS 7 projects use extremely large quantities of data complicates the situation even further, and it can take a long time to load and save information as a result. Without a sustainable strategy for operating a SIMATIC PCS 7 installation, searching for the right software version can become extremely time-consuming and the installation may run inefficiently as a result.