Download PDF
AcoustiFLO: Enhancing Efficiency and Reducing Costs with IoT
Technology Category
- Sensors - Airflow Sensors
- Sensors - Liquid Detection Sensors
Applicable Functions
- Product Research & Development
- Quality Assurance
Use Cases
- Experimentation Automation
- Virtual Prototyping & Product Testing
Services
- Hardware Design & Engineering Services
- Testing & Certification
The Challenge
The commercial fan market has been shifting from large custom-designed fan systems to more standardized factory-manufactured units. In response to this trend, AcoustiFLO aimed to develop an efficient small centrifugal fan that could be marketed as a standardized, modular component suitable for packaged air handlers. The concept for this small fan consisted of a centrifugal impeller housed in a vaneless diffuser. However, optimizing the static pressure efficiency of the unit required simultaneous optimization of both the impeller and the diffuser due to their interaction. The engineers at AcoustiFLO found that physical testing was not only cost prohibitive but also failed to provide the necessary insight into the airflow for design improvement. The less powerful CFD software they had been using for simpler design tasks lacked the power to analyze the turbulence and rotational dynamics in the impeller.
About The Customer
AcoustiFLO LLC is a privately held company based in Boulder, Colorado, U.S.A. The company specializes in custom fan application engineering, catering to customers who have efficiency and acoustic performance requirements that cannot be met with off-the-shelf systems. AcoustiFLO has a broad customer base, having worked with most major semiconductor manufacturers. The company boasts hundreds of fan installations around the world, demonstrating its global reach and the widespread demand for its specialized services.
The Solution
AcoustiFLO turned to ANSYS Fluent CFD software to overcome these challenges. This technology allowed the engineers to systematically evaluate a large number of design changes before testing a prototype. They were able to verify that the Fluent model predictions were sufficiently close to the prototype test results. The software also enabled them to discover unexpected interactions between the diffuser and the impeller that would have been difficult to assess with physical testing alone. As a result, they were able to develop a prototype design with optimum performance. The use of Fluent CFD software not only provided valuable insights into the airflow inside the impeller and diffuser that would not have been possible with a testing-based approach but also increased the peak efficiency of the unit by 13 percent.
Operational Impact
Quantitative Benefit
Related Case Studies.
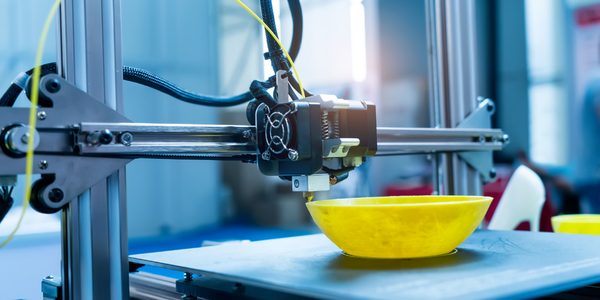
Case Study
Intralox Using Demo3D Case Study
Intralox strives to create significant economic value for our customers by optimizing their conveyance systems. Intralox wants to emulate real-world production environments for end users and OEMs working in multiple industries, including packaging, warehousing, parcel, beverage, brewery, food, tire, and consumer goods. They frequently had to perform physical tests to demonstrate to customers how ARB equipment would handle their products.
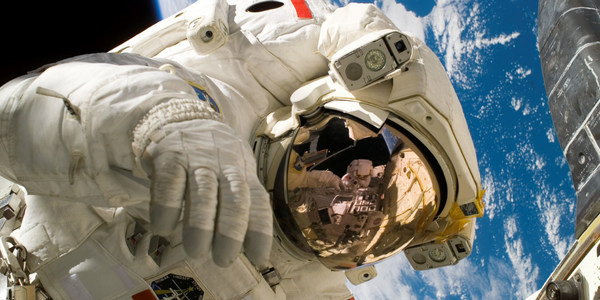
Case Study
General Dynamics Uses Wind River Simics to Meet NASA Challenge
In designing and building Fermi, the General Dynamics C4 Systems business unit was faced with a challenge: it needed to provide an environment that could support rigorous testing by multiple Fermi subsystem groups before the spacecraft hardware was available.
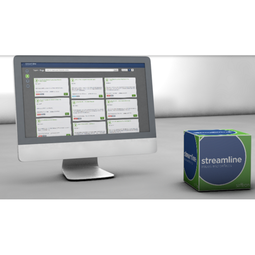
Case Study
Issue and Defect Resolution
One of the world's largest complex hardware manufacturers' business units, responsible for the post-product validation process, was looking to speed up its time to market and the time it took to identify and resolve process issues. Duplicate debugging hardware and software issues was eating up 70% of production time, slowing down time to market and costing money.