Download PDF
Actronika Designs Touch-Sensitive Haptic Technology Systems for Interactive Consumer Products
Technology Category
- Platform as a Service (PaaS) - Application Development Platforms
- Application Infrastructure & Middleware - Data Exchange & Integration
- Analytics & Modeling - Real Time Analytics
Applicable Industries
- Automotive
- Consumer Goods
Applicable Functions
- Product Research & Development
- Quality Assurance
- Business Operation
Use Cases
- Predictive Maintenance
- Remote Collaboration
- Digital Twin
Services
- Cloud Planning, Design & Implementation Services
- System Integration
- Software Design & Engineering Services
The Challenge
Haptic technology pioneer Actronika integrates its touch-sensitive screen processors into other companies’ hardware, including automobiles, phones, video games, and other consumer products. Working with multiple partners using multiple CAD systems, the Actronika engineering team was spending a considerable amount of time importing, exporting, and managing CAD files. The company was seeking a cloud-native product development platform that would eliminate the hassles of data management and speed up communication with manufacturing partners.
About The Customer
Based in Paris, France, Actronika is an R&D company that develops patented haptic processing units (HPUs) that connect to actuators and tiny vibrotactile motors inside other companies’ products to create 'endless possibilities of high definition sensations.' Actronika was launched in 2016, based on the research of Vincent Hayward, Professor of Tactile Perception and Technologies at Sorbonne University. The company focuses on enriching the relationship between humans and machines by adding the sense of touch. Actronika’s three main focuses are the automotive, mobile, and gaming industries. They are a partner of Novares, a global plastic component supplier to OEMs and Tier-1 companies in the automotive industry.
The Solution
To streamline communication between their design team and their external partners, Actronika chose PTC’s Onshape, the only SaaS product development platform that combines CAD, data management, real-time collaboration tools, and business analytics. Onshape’s Sharing feature allows Actronika to instantly share CAD models with manufacturing partners to review in real time. The platform’s built-in version control eliminates the risk of engineers working on the wrong version of a design. Onshape’s portability allows easier access for the company’s Linux-using software team to participate in design reviews. Additionally, Onshape’s real-time data management ensures that whenever an engineer makes a change or edit to their 3D CAD model, everyone on the design team instantly sees it. A comprehensive Edit History also records who made what changes and when, allowing the team to return to any prior state of the design at any time.
Operational Impact
Related Case Studies.
.png)
Case Study
Improving Vending Machine Profitability with the Internet of Things (IoT)
The vending industry is undergoing a sea change, taking advantage of new technologies to go beyond just delivering snacks to creating a new retail location. Intelligent vending machines can be found in many public locations as well as company facilities, selling different types of goods and services, including even computer accessories, gold bars, tickets, and office supplies. With increasing sophistication, they may also provide time- and location-based data pertaining to sales, inventory, and customer preferences. But at the end of the day, vending machine operators know greater profitability is driven by higher sales and lower operating costs.
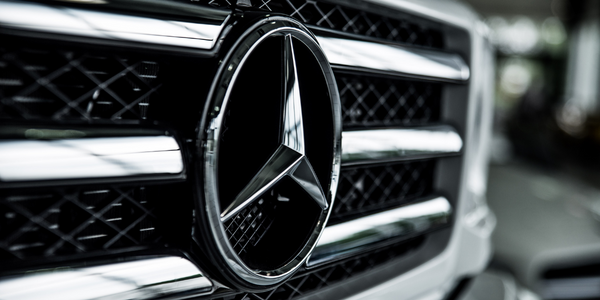
Case Study
Integral Plant Maintenance
Mercedes-Benz and his partner GAZ chose Siemens to be its maintenance partner at a new engine plant in Yaroslavl, Russia. The new plant offers a capacity to manufacture diesel engines for the Russian market, for locally produced Sprinter Classic. In addition to engines for the local market, the Yaroslavl plant will also produce spare parts. Mercedes-Benz Russia and his partner needed a service partner in order to ensure the operation of these lines in a maintenance partnership arrangement. The challenges included coordinating the entire maintenance management operation, in particular inspections, corrective and predictive maintenance activities, and the optimizing spare parts management. Siemens developed a customized maintenance solution that includes all electronic and mechanical maintenance activities (Integral Plant Maintenance).