Download PDF
Arca Architects’ Silver Café: Beacon on the BAY
Technology Category
- Functional Applications - Remote Monitoring & Control Systems
Applicable Industries
- Construction & Infrastructure
Applicable Functions
- Facility Management
- Quality Assurance
Use Cases
- Building Automation & Control
- Building Energy Management
- Construction Site Monitoring
- Digital Twin
Services
- Software Design & Engineering Services
- System Integration
The Challenge
Around the middle of the 20th century, Morecambe was a vibrant and thriving seaside resort. With the rise of the cheap package holiday and the collapse of the manufacturing industry, the area suffered a serious slowdown. Morecambe still relies heavily on tourism, hospitality, and catering to buoy its sluggish economy. Starting in the spring of 2006, the town made great strides towards reclaiming its glorious past, most notably with the restoration of the art deco style Midland Hotel. And in 2007, Lancaster City Council and their regeneration team called “Winning Back Morecambe” sought a landmark design to fill the open space between the sea and the promenade. Entrants were encouraged to design a small café that could redefine an area alongside several weathered and worn seaside buildings. After considering several different firms for the job, the council selected Arca in the fall of 2007. Lee and his team met with local neighborhood representatives and discovered that these representatives were far from conservative in their views of the space. In fact, they even supported ideas for unorthodox designs with a commanding presence. This was historic, since the last building to be placed in the area between the promenade and the sea was the second Midland Hotel, built in 1933. Arca understood the great importance of what they were about to undertake.
About The Customer
In 1998, Lee, a former Associate at Grimshaw Architects in London, decided to strike out on his own. Drawing from a pool of highly respected architects and other experienced designers, he formed Arca Architects, a fluid team that he tailors for each architectural project. Arca designs private as well as public spaces, including hotels, infrastructure, art galleries, recreational facilities, and multi-family and single-family homes. Lee strongly believes “that designs should be intellectually satisfying,” so his work incorporates various tactile, graphic, and sensory components to truly stimulate the mind. His efforts paid off, and Arca’s Silver Café won the 2009 Small Scale Commercial Award from the Manchester Society of Architects (MSA). The firm has also been honored with numerous Royal Institute of British Architects (RIBA) design competition laureates and RIBA shortlistings, and Arca was a finalist for two coveted Young Architect of the Year Awards in 2000, a distinction awarded to prominent firms including NORD and Carmody Groarke.
The Solution
Using a feasibility study to provide a baseline for the proposals, the council and regeneration team requested a 40-50 seat café with a kitchen and several auxiliary spaces, as well as four public restrooms that could be placed nearby. Sandwiched between the promenade and the tall sea wall, a small café would have a good view of the wall—but not the bay. Arca responded with an innovative suggestion—to raise the café’s floor level above the sea wall to open up a spectacular vista. The team also recommended shelter for the outdoor spaces to encourage patrons to take in the fresh air. Rather than aligning the café and restrooms architecturally, Lee chose a different approach. He wrapped the leaning rounded rectangular frame of the café with a strip of shiny stainless steel. Meanwhile, he designed the restrooms to be a steel black cuboid. Lee describes the contrasting structures as “taking on the quality of autonomous objects deposited on the tide line.” While both are softened by the beach on one side and a tiered patio on the other, they are a sharp contrast to the older architecture in their backdrop. Lee designed the spaces to withstand the elements well. The café sits on a concrete raft foundation. It has a steel superstructure, which is bound in plywood with a high value insulation to the cladding material. “The stainless steel envelope wraps the space and frames views of the bay,” he explains. To accommodate the raised site, Arca created a ramp that links the café to several redesigned promenade gardens below. The team also expanded the tiered terraces towards the south, creating a protected intimate dining space with garden views. He finished the restrooms in weather resistant black paint. Large, beautiful solid wood doors warm the industrial look and add a layered tactility to the space.
Operational Impact
Quantitative Benefit
Related Case Studies.
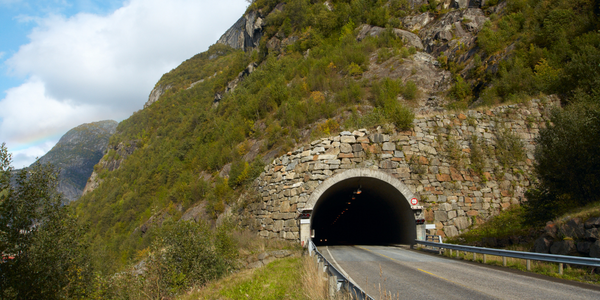
Case Study
IoT System for Tunnel Construction
The Zenitaka Corporation ('Zenitaka') has two major business areas: its architectural business focuses on structures such as government buildings, office buildings, and commercial facilities, while its civil engineering business is targeted at structures such as tunnels, bridges and dams. Within these areas, there presented two issues that have always persisted in regard to the construction of mountain tunnels. These issues are 'improving safety" and "reducing energy consumption". Mountain tunnels construction requires a massive amount of electricity. This is because there are many kinds of electrical equipment being used day and night, including construction machinery, construction lighting, and ventilating fan. Despite this, the amount of power consumption is generally not tightly managed. In many cases, the exact amount of power consumption is only ascertained when the bill from the power company becomes available. Sometimes, corporations install demand-monitoring equipment to help curb the maximum power demanded. However, even in these cases, the devices only allow the total volume of power consumption to be ascertained, or they may issue warnings to prevent the contracted volume of power from being exceeded. In order to tackle the issue of reducing power consumption, it was first necessary to obtain an accurate breakdown of how much power was being used in each particular area. In other words, we needed to be able to visualize the amount of power being consumed. Safety, was also not being managed very rigorously. Even now, tunnel construction sites often use a 'name label' system for managing entry into the work site. Specifically, red labels with white reverse sides that bear the workers' names on both sides are displayed at the tunnel work site entrance. The workers themselves then flip the name label to the appropriate side when entering or exiting from the work site to indicate whether or not they are working inside the tunnel at any given time. If a worker forgets to flip his or her name label when entering or exiting from the tunnel, management cannot be performed effectively. In order to tackle the challenges mentioned above, Zenitaka decided to build a system that could improve the safety of tunnel construction as well as reduce the amount of power consumed. In other words, this new system would facilitate a clear picture of which workers were working in each location at the mountain tunnel construction site, as well as which processes were being carried out at those respective locations at any given time. The system would maintain the safety of all workers while also carefully controlling the electrical equipment to reduce unnecessary power consumption. Having decided on the concept, our next concern was whether there existed any kind of robust hardware that would not break down at the construction work site, that could move freely in response to changes in the working environment, and that could accurately detect workers and vehicles using radio frequency identification (RFID). Given that this system would involve many components that were new to Zenitaka, we decided to enlist the cooperation of E.I.Sol Co., Ltd. ('E.I.Sol') as our joint development partner, as they had provided us with a highly practical proposal.
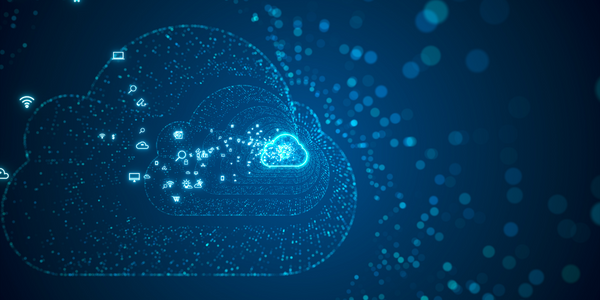
Case Study
Splunk Partnership Ties Together Big Data & IoT Services
Splunk was faced with the need to meet emerging customer demands for interfacing IoT projects to its suite of services. The company required an IoT partner that would be able to easily and quickly integrate with its Splunk Enterprise platform, rather than allocating development resources and time to building out an IoT interface and application platform.
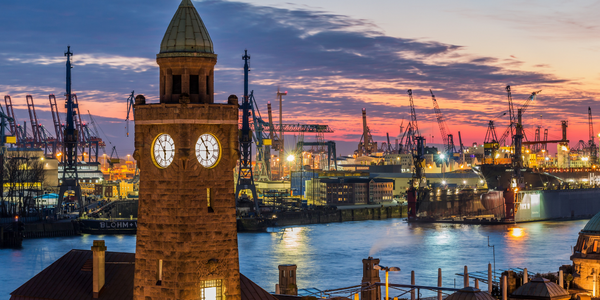
Case Study
Bridge monitoring in Hamburg Port
Kattwyk Bridge is used for both rail and road transport, and it has played an important role in the Port of Hamburg since 1973. However, the increasing pressure from traffic requires a monitoring solution. The goal of the project is to assess in real-time the bridge's status and dynamic responses to traffic and lift processes.
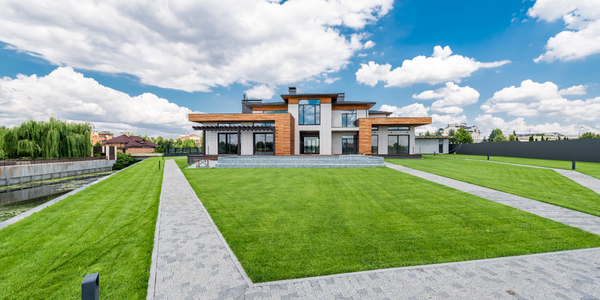
Case Study
Bellas Landscaping
Leading landscaping firm serving central Illinois streamlines operations with Samsara’s real-time fleet tracking solution: • 30+ vehicle fleet includes International Terrastar dump trucks and flatbeds, medium- and light-duty pickups from Ford and Chevrolet. Winter fleet includes of snow plows and salters.

Case Study
Condition Based Monitoring for Industrial Systems
A large construction aggregate plant operates 10 high horsepower Secondary Crusher Drive Motors and associated conveyor belts, producing 600 tons of product per hour. All heavy equipment requires maintenance, but the aggregate producer’s costs were greatly magnified any time that the necessary maintenance was unplanned and unscheduled. The product must be supplied to the customers on a tight time schedule to fulfill contracts, avoid penalties, and prevent the loss of future business. Furthermore, a sudden failure in one of the drive motors would cause rock to pile up in unwanted locations, extending the downtime and increasing the costs.Clearly, preventative maintenance was preferable to unexpected failures. So, twice each year, the company brought in an outside vendor to attach sensors to the motors, do vibration studies, measure bearing temperatures and attempt to assess the health of the motors. But that wasn’t enough. Unexpected breakdowns continued to occur. The aggregate producer decided to upgrade to a Condition Based Monitoring (CBM) sensor system that could continually monitor the motors in real time, apply data analytics to detect changes in motor behavior before they developed into major problems, and alert maintenance staff via email or text, anywhere they happened to be.A wired sensor network would have been cost prohibitive. An aggregate plant has numerous heavy vehicles moving around, so any cabling would have to be protected. But the plant covers 400 acres, and the cable would have to be trenched to numerous locations. Cable wasn’t going to work. The aggregate producer needed a wireless solution.