Download PDF
Astec Industries' Optimization of Hot-Mix Asphalt Equipment with ANSYS ICEM CFD
Applicable Industries
- Equipment & Machinery
Applicable Functions
- Product Research & Development
The Challenge
Astec Industries, a leading manufacturer of hot-mix asphalt plants and soil remediation equipment, faced several challenges in their design and manufacturing process. The company started with CAD models intended solely for manufacturing, which resulted in very complex and imperfect assemblies. They needed to quickly generate parametric studies to determine key design variables, but were constrained by demanding time scales for results. Additionally, there was a vast difference in the scale of detail on most models, further complicating the design and optimization process.
About The Customer
Astec Industries, Inc. is a leading American company that designs and manufactures a complete line of continuous and batch-process hot-mix asphalt plants, as well as soil remediation equipment. Since its inception in 1972, Astec has grown to become the market leader in hot-mix asphalt plants in the United States. The company prides itself on listening to customers and understanding every aspect of their business, which enables it to provide new products that solve problems and increase profitability. Astec's design engineers use a range of analysis tools, including CFD, FEA, and DEM, to design and optimize critical components.
The Solution
Astec Industries turned to ANSYS ICEM CFD Tetra and its direct CAD interface to address these challenges. The software allowed linking of mesh parameters with the CAD geometry, streamlining the generation of parametric studies. The extensive geometry clean-up tools provided by ANSYS ICEM CFD enabled the modification of imperfect geometry, making the design process more efficient. The solution also offered curvature and proximity-based auto-refinement and excellent interactive refinement controls, which further enhanced the design and optimization process.
Operational Impact
Related Case Studies.
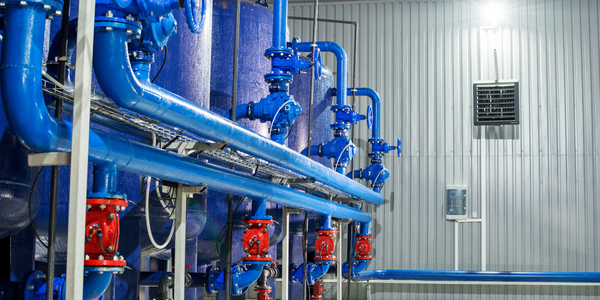
Case Study
Smart Water Filtration Systems
Before working with Ayla Networks, Ozner was already using cloud connectivity to identify and solve water-filtration system malfunctions as well as to monitor filter cartridges for replacements.But, in June 2015, Ozner executives talked with Ayla about how the company might further improve its water systems with IoT technology. They liked what they heard from Ayla, but the executives needed to be sure that Ayla’s Agile IoT Platform provided the security and reliability Ozner required.
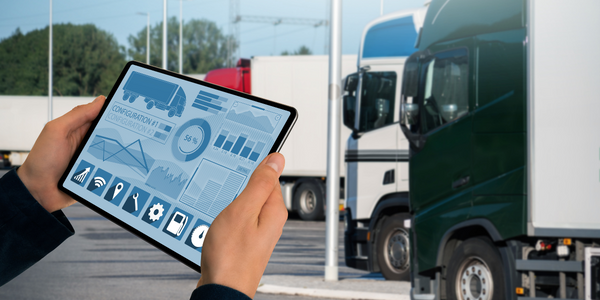
Case Study
IoT enabled Fleet Management with MindSphere
In view of growing competition, Gämmerler had a strong need to remain competitive via process optimization, reliability and gentle handling of printed products, even at highest press speeds. In addition, a digitalization initiative also included developing a key differentiation via data-driven services offers.
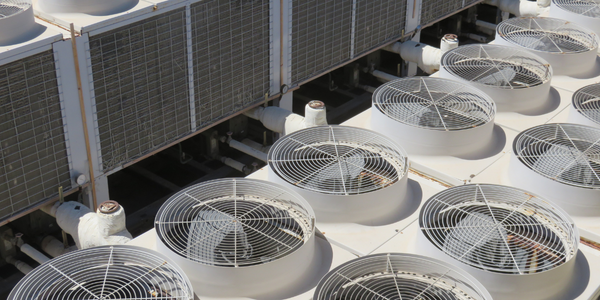
Case Study
Predictive Maintenance for Industrial Chillers
For global leaders in the industrial chiller manufacturing, reliability of the entire production process is of the utmost importance. Chillers are refrigeration systems that produce ice water to provide cooling for a process or industrial application. One of those leaders sought a way to respond to asset performance issues, even before they occur. The intelligence to guarantee maximum reliability of cooling devices is embedded (pre-alarming). A pre-alarming phase means that the cooling device still works, but symptoms may appear, telling manufacturers that a failure is likely to occur in the near future. Chillers who are not internet connected at that moment, provide little insight in this pre-alarming phase.
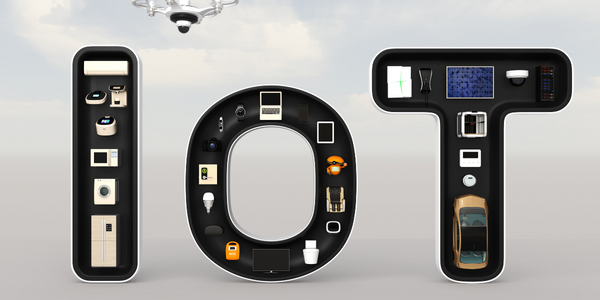
Case Study
Premium Appliance Producer Innovates with Internet of Everything
Sub-Zero faced the largest product launch in the company’s history:It wanted to launch 60 new products as scheduled while simultaneously opening a new “greenfield” production facility, yet still adhering to stringent quality requirements and manage issues from new supply-chain partners. A the same time, it wanted to increase staff productivity time and collaboration while reducing travel and costs.
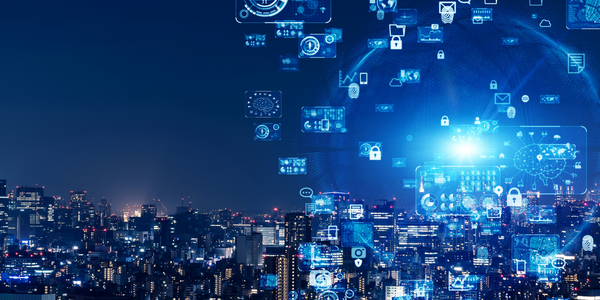
Case Study
Integration of PLC with IoT for Bosch Rexroth
The application arises from the need to monitor and anticipate the problems of one or more machines managed by a PLC. These problems, often resulting from the accumulation over time of small discrepancies, require, when they occur, ex post technical operations maintenance.
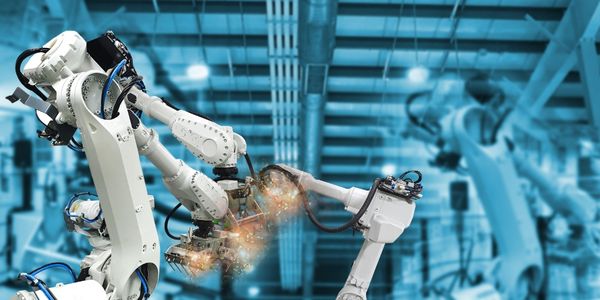
Case Study
Robot Saves Money and Time for US Custom Molding Company
Injection Technology (Itech) is a custom molder for a variety of clients that require precision plastic parts for such products as electric meter covers, dental appliance cases and spools. With 95 employees operating 23 molding machines in a 30,000 square foot plant, Itech wanted to reduce man hours and increase efficiency.