Download PDF
Autogrill's Supply Chain Enhancement through IoT Connectivity and Visibility
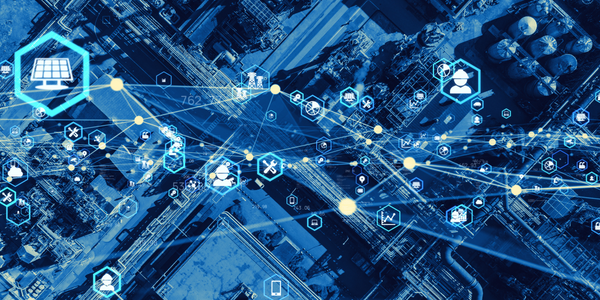
Technology Category
- Application Infrastructure & Middleware - Event-Driven Application
- Platform as a Service (PaaS) - Application Development Platforms
Applicable Functions
- Logistics & Transportation
Use Cases
- Supply Chain Visibility
Services
- System Integration
The Challenge
Autogrill, a multinational catering company operating in 30 countries, faced a significant challenge in providing their suppliers with direct access to their core system data. The suppliers required this access for improved visibility, analytics, and order effectiveness. Autogrill also needed better anticipation of stock levels, localized costs in each market, and additional supply chain information. The data resided in their IBM i (AS/400) and SAP systems, and accessing it in a quick, secure, and cost-effective manner without creating thousands of queries was a significant challenge. Autogrill was in search of a partner who could support them in achieving these goals and provide secure services granting real-time information from their core systems.
The Customer
Autogrill
About The Customer
Autogrill is an Italian-based multinational catering company that sells food and non-food products. The company operates in 30 different countries, primarily in Europe, and runs restaurants along all Italian highways. Autogrill also represents other important brands in Italy and Europe. Many suppliers are interested in selling their goods in Autogrill shops, making the company a significant player in the catering industry. Autogrill's operations are vast and complex, requiring efficient and effective supply chain management.
The Solution
Autogrill partnered with OpenLegacy, a company that specializes in creating and developing APIs. After the CIO of Autogrill attended a webinar by OpenLegacy, he saw potential in their technology and business solution. Autogrill, in collaboration with their technological partners, formed a team with knowledge of the legacy systems and integration processes. This team included multiple connectors to their backends that generate cloud-native microservices. These microservices were created and used by the Autogrill team and partners to leverage their core systems. OpenLegacy's support for IBM i and SAP was a significant factor in Autogrill's digitalization and modernization strategy.
Operational Impact
Quantitative Benefit
Related Case Studies.
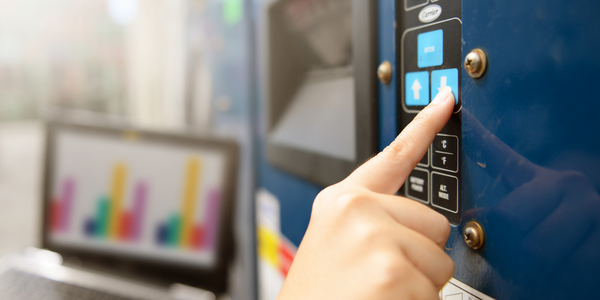
Case Study
Remote Temperature Monitoring of Perishable Goods Saves Money
RMONI was facing temperature monitoring challenges in a cold chain business. A cold chain must be established and maintained to ensure goods have been properly refrigerated during every step of the process, making temperature monitoring a critical business function. Manual registration practice can be very costly, labor intensive and prone to mistakes.
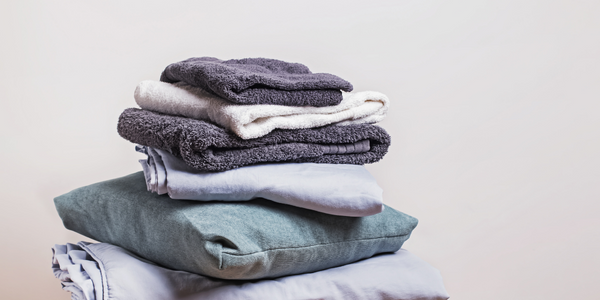
Case Study
Retail Uses RFID to Enable Cold Chain Monitoring
Like most grocery retailers, Hy-Vee is faced with the challenge of providing the highest quality products to its shoppers. Shoppers want the longest possible shelf life from perishable products and expect a consistent product experience each time they shop. Controlling the quality of products sold leads to shopper loyalty, which is of paramount importance to the success of Hy-Vee. Before products arrive in stores, Hy-Vee's distribution centers (DCs) handle items including dairy products, fresh meats, seafood, deli items, produce and frozen goods, all of which have different temperature needs and sensitivities. During transit from suppliers to DCs, Hy-Vee has limited visibility and temperature management abilities due to large amount of supplier managed transportation. For instance, during a week-long transit, a supplier's carrier equipment may malfunction, causing an item to thaw and then refreeze once repairs are made. Hy-Vee sought help from TempTRIP, an RFID solution provider that focuses on shipping, storage, receiving, and temperature control. TempTRIP's EPC RFID tags use Impinj chips to monitor and report temperature readings throughout the shipping and receiving process. The tags can also be re-configured and re-used, a unique feature within the current market of temperature monitoring devices.
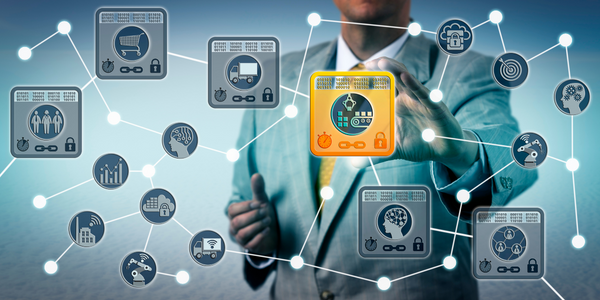
Case Study
Covisint Improves Mitsubishi's Collaboration With Its Supply Chain
Mitsubishi sought to improve supplier relationships on a global basis and to offer an easy-to-use solution to interact with them. In August 2004, Mitsubishi selected Covisint’s platform to help improve sharing of information and collaborative business processes with its global suppliers. Covisint enabled Mitsubishi to provide its suppliers with immediate access to information and applications to obtain more collaborative working relationships