Download PDF
Automated Dashboards in Customer Analysis: A Case Study of OVH
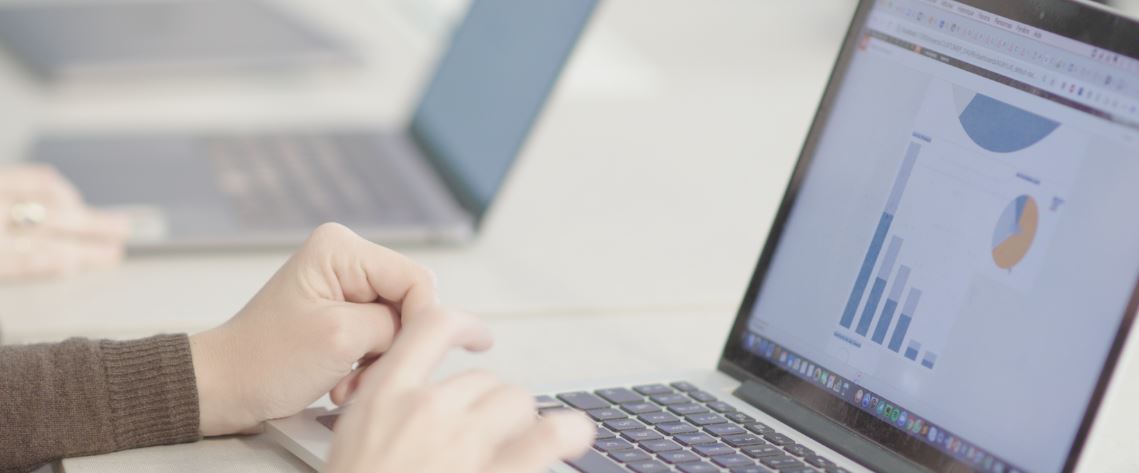
Technology Category
- Application Infrastructure & Middleware - Data Visualization
- Functional Applications - Enterprise Resource Planning Systems (ERP)
Applicable Industries
- Electrical Grids
- Equipment & Machinery
Applicable Functions
- Quality Assurance
Use Cases
- Rapid Prototyping
- Time Sensitive Networking
Services
- Testing & Certification
The Challenge
OVH, a global provider of hyperscale cloud, faced a significant challenge in analyzing user interactions on their website to inform product and operations decisions. The primary point of contact between OVH and its users was through their website, where customers could place orders and receive technical advice or support. The business analysts responsible for disseminating data and insights to inform on the commercialization and optimization of the website had built a dashboard with basic, high-level metrics like user behaviors and site traffic. However, the dashboard's utility was limited as it did not combine different data sources for a complete view, necessitating ad-hoc analysis. The analysts had little time for this, and the ETL (extract, transform, load) for the dashboard presented concerns for the data architects around data and insights quality. There was a lack of transparency around exactly what data was being transformed and how.
The Customer
OVH
About The Customer
OVH is a global provider of hyperscale cloud, offering businesses a benchmark for value and performance in the sector. Founded in 1999, the group manages and maintains 27 data centers in 12 sites across four continents, deploys its own global fibre optic network, and manages the entire supply chain for web hosting. Running on its own infrastructures, OVH provides simple, powerful tools for businesses, revolutionizing the way that more than 1 million customers work across the globe. The primary point of contact between OVH and its users is through their website, where customers can place an order and receive technical advice or support.
The Solution
OVH turned to Dataiku to power their dashboards, leveraging its features to slash data preparation time and ensure visibility into the data life cycle. Dataiku allowed OVH business analysts to connect directly to any number of data sources, such as weblogs and CRM, and combine these data sources for more complete customer insights. The data preparation work was made efficient thanks to an intuitive visual interface and the automation of much of the process. This fostered a culture of experimentation and rapid prototyping, enabling a small team of data scientists to accomplish more. Dataiku also gave data architects peace of mind that analysts were working with quality data thanks to the clear visualization of data flows. It allowed data architects to clearly see and correct any issues in data quality directly, and gave data scientists the opportunity to work directly with data prepared by analysts to apply ML techniques to other facets of the business more efficiently.
Operational Impact
Quantitative Benefit
Related Case Studies.
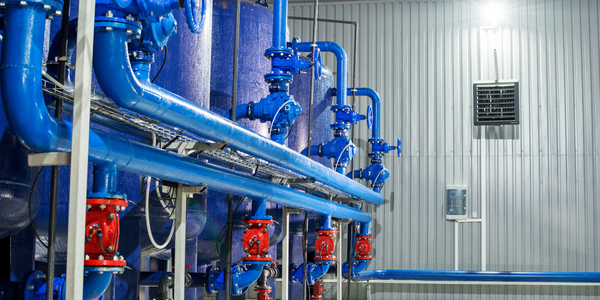
Case Study
Smart Water Filtration Systems
Before working with Ayla Networks, Ozner was already using cloud connectivity to identify and solve water-filtration system malfunctions as well as to monitor filter cartridges for replacements.But, in June 2015, Ozner executives talked with Ayla about how the company might further improve its water systems with IoT technology. They liked what they heard from Ayla, but the executives needed to be sure that Ayla’s Agile IoT Platform provided the security and reliability Ozner required.
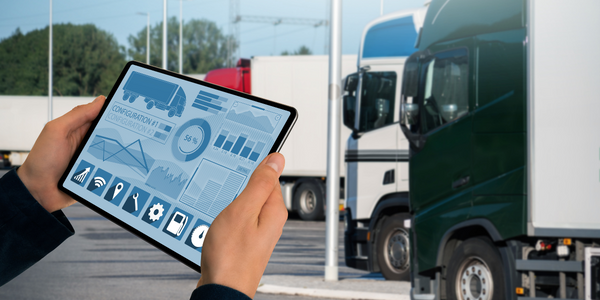
Case Study
IoT enabled Fleet Management with MindSphere
In view of growing competition, Gämmerler had a strong need to remain competitive via process optimization, reliability and gentle handling of printed products, even at highest press speeds. In addition, a digitalization initiative also included developing a key differentiation via data-driven services offers.
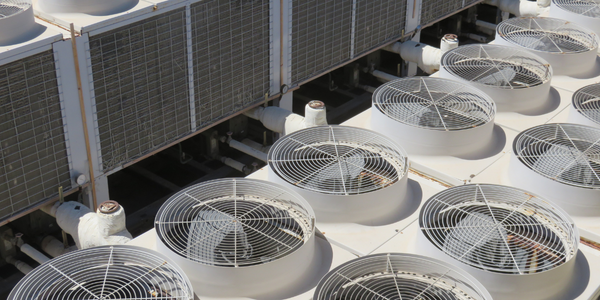
Case Study
Predictive Maintenance for Industrial Chillers
For global leaders in the industrial chiller manufacturing, reliability of the entire production process is of the utmost importance. Chillers are refrigeration systems that produce ice water to provide cooling for a process or industrial application. One of those leaders sought a way to respond to asset performance issues, even before they occur. The intelligence to guarantee maximum reliability of cooling devices is embedded (pre-alarming). A pre-alarming phase means that the cooling device still works, but symptoms may appear, telling manufacturers that a failure is likely to occur in the near future. Chillers who are not internet connected at that moment, provide little insight in this pre-alarming phase.
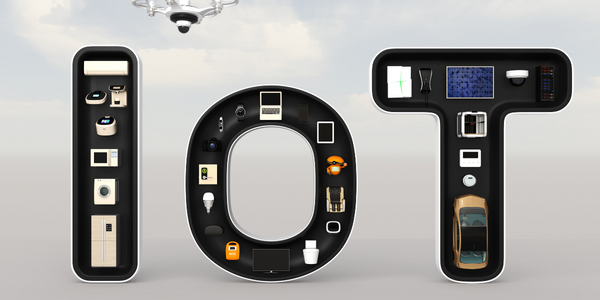
Case Study
Premium Appliance Producer Innovates with Internet of Everything
Sub-Zero faced the largest product launch in the company’s history:It wanted to launch 60 new products as scheduled while simultaneously opening a new “greenfield” production facility, yet still adhering to stringent quality requirements and manage issues from new supply-chain partners. A the same time, it wanted to increase staff productivity time and collaboration while reducing travel and costs.
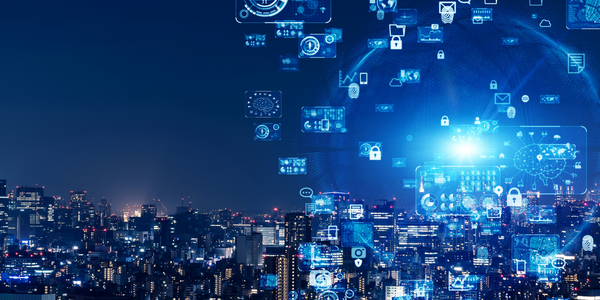
Case Study
Integration of PLC with IoT for Bosch Rexroth
The application arises from the need to monitor and anticipate the problems of one or more machines managed by a PLC. These problems, often resulting from the accumulation over time of small discrepancies, require, when they occur, ex post technical operations maintenance.
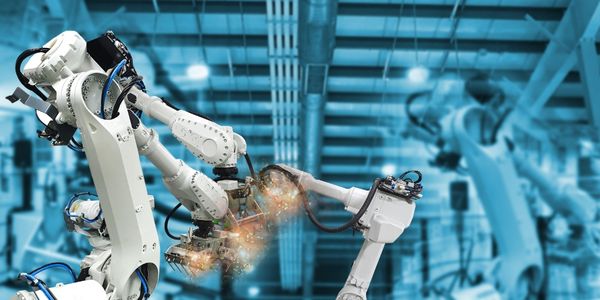
Case Study
Robot Saves Money and Time for US Custom Molding Company
Injection Technology (Itech) is a custom molder for a variety of clients that require precision plastic parts for such products as electric meter covers, dental appliance cases and spools. With 95 employees operating 23 molding machines in a 30,000 square foot plant, Itech wanted to reduce man hours and increase efficiency.