Automatic monitoring of acoustic emission saves catastrophic failure
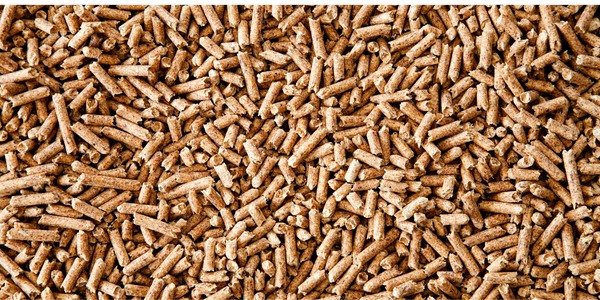
- Analytics & Modeling - Edge Analytics
- Analytics & Modeling - Predictive Analytics
- Functional Applications - Remote Monitoring & Control Systems
- Sensors - Acoustic Sensors
- Sensors - Humidity Sensors
- Sensors - Temperature Sensors
- Construction & Infrastructure
- Discrete Manufacturing
- Machine Condition Monitoring
Traditional measurement tools are ineffective when it comes to slowly rotating equipment. There are faults like Bearing Failure, Ring Plugging, Gear Tooth Crack and many more which can lead to the shutdown of machines. 1 minute of downtime cost the company $10. RingPluggingis a very common issue which Pinnacle Pellet was facing very frequently due to diverse feed quality into the machines. Product ring plugging can be detected as sound levels increase in specific roller bearings.
We proposed our RotationLF system under which we installed wireless sensors as a part of a pilot project on multiple types of equipment.
RotationLFhas several features including:
- Vibration, Acoustic Emission & Temperature, Humidity & RPM
- Online Diagnosis
- Fault detection
Once installed, strong battery-powered wireless sensors started monitoring pump and motors and sent data to our SaaS-based platform through an encrypted & secured network using Edge and Cloud computing. As data was received, RotationLF platform worked on data analysis using highly sophisticated algorithms.
Approximately 1 month after the sensors were installed, the system alerted Pinnacle that fault had been detected on the equipment named Pelletor 5 specifying the reason for notification sown in the image on right. The acoustic emission pattern depicted in the system is indicative of an early-stage failure.
Related Case Studies.
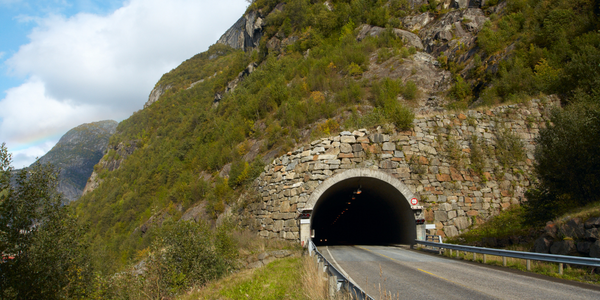
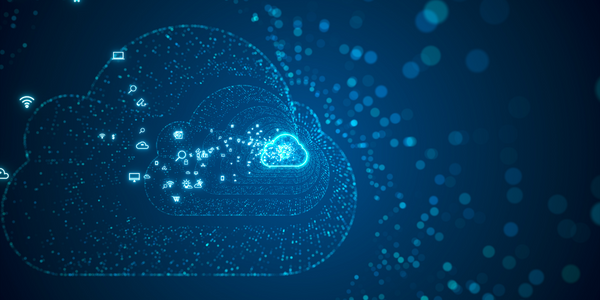
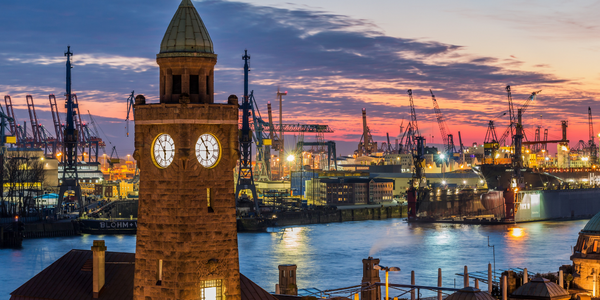
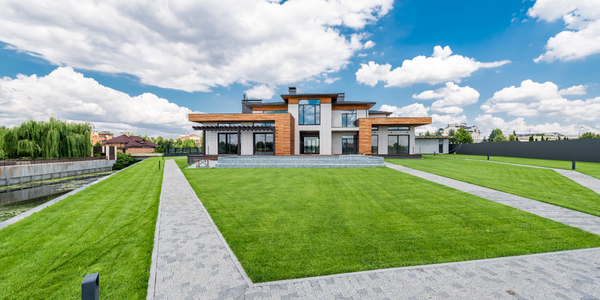
