Download PDF
AVINED: Securing the Dutch Poultry Sector with IoT
Technology Category
- Infrastructure as a Service (IaaS) - Cloud Databases
- Platform as a Service (PaaS) - Application Development Platforms
Applicable Functions
- Logistics & Transportation
Use Cases
- Supply Chain Visibility
The Challenge
The Dutch Ministry of Economic Affairs (EZ) is tasked with ensuring the safety of poultry supply chains in the Netherlands. One of the key responsibilities is the collection of salmonella data in the poultry supply chain, a task that has been delegated to AVINED. The challenge was to manage and offer a self-regulatory database for this purpose. The data collected is crucial for a variety of tasks such as registration of laboratory tests, reporting, and issuing important alerts. The poultry sector, like many others, has a complex structure with numerous stakeholders, making data management and collection a daunting task. The need for a system that could simplify this process, enable rapid response, and ensure transparency throughout the sector was evident.
About The Customer
AVINED is an organization tasked by the Dutch Ministry of Economic Affairs (EZ) with certain responsibilities related to the safety of the poultry supply chain in the Netherlands. One of their key roles is the management of a self-regulatory database for collecting salmonella data in the poultry supply chain. AVINED works closely with affiliated foundations OVONED and PLUIMNED, which use the same technology to implement quality management systems. AVINED's work is crucial in ensuring the safety and transparency of the poultry sector in the Netherlands.
The Solution
To address this challenge, AVINED implemented ChainPoint technology as their platform of choice. A dedicated platform, KIPnet, was created based on ChainPoint’s technology. KIPnet serves as the official salmonella database for the Dutch Poultry sector in the Netherlands. In addition, the affiliated foundations OVONED and PLUIMNED use ChainPoint to implement the “IKB Ei” and “IKB Kip” quality management systems. The recorded data and the platform are used for a variety of tasks including management of hygiene and other IKB programmes, registration of lab-tests for salmonella with interfacing to the Dutch Food and Consumer Product Safety Authority, mass-balance traceability of egg consumption, sharing of data and information with internal and external platforms, and storytelling: using the print code on the egg to display information about the producing farmer.
Operational Impact
Related Case Studies.
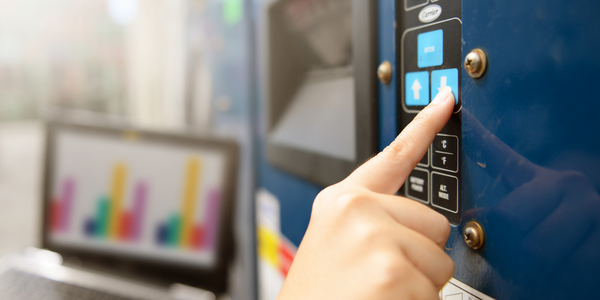
Case Study
Remote Temperature Monitoring of Perishable Goods Saves Money
RMONI was facing temperature monitoring challenges in a cold chain business. A cold chain must be established and maintained to ensure goods have been properly refrigerated during every step of the process, making temperature monitoring a critical business function. Manual registration practice can be very costly, labor intensive and prone to mistakes.
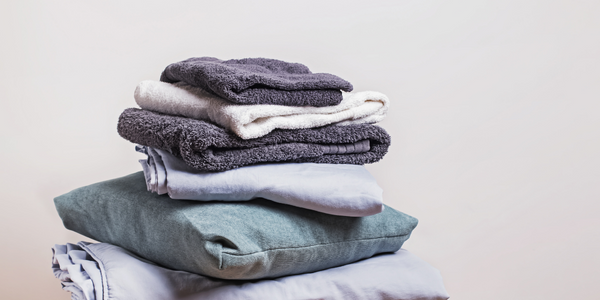
Case Study
Retail Uses RFID to Enable Cold Chain Monitoring
Like most grocery retailers, Hy-Vee is faced with the challenge of providing the highest quality products to its shoppers. Shoppers want the longest possible shelf life from perishable products and expect a consistent product experience each time they shop. Controlling the quality of products sold leads to shopper loyalty, which is of paramount importance to the success of Hy-Vee. Before products arrive in stores, Hy-Vee's distribution centers (DCs) handle items including dairy products, fresh meats, seafood, deli items, produce and frozen goods, all of which have different temperature needs and sensitivities. During transit from suppliers to DCs, Hy-Vee has limited visibility and temperature management abilities due to large amount of supplier managed transportation. For instance, during a week-long transit, a supplier's carrier equipment may malfunction, causing an item to thaw and then refreeze once repairs are made. Hy-Vee sought help from TempTRIP, an RFID solution provider that focuses on shipping, storage, receiving, and temperature control. TempTRIP's EPC RFID tags use Impinj chips to monitor and report temperature readings throughout the shipping and receiving process. The tags can also be re-configured and re-used, a unique feature within the current market of temperature monitoring devices.
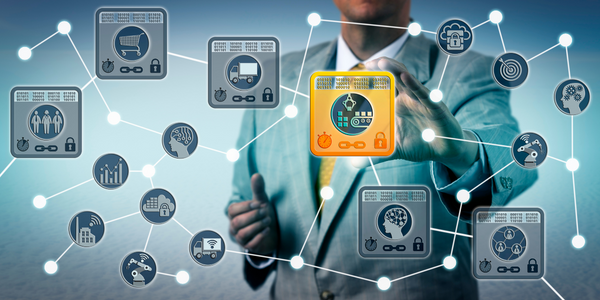
Case Study
Covisint Improves Mitsubishi's Collaboration With Its Supply Chain
Mitsubishi sought to improve supplier relationships on a global basis and to offer an easy-to-use solution to interact with them. In August 2004, Mitsubishi selected Covisint’s platform to help improve sharing of information and collaborative business processes with its global suppliers. Covisint enabled Mitsubishi to provide its suppliers with immediate access to information and applications to obtain more collaborative working relationships