Download PDF
Bantam Materials Revolutionizes Packaging Supply Chain with Canto
Technology Category
- Application Infrastructure & Middleware - Middleware, SDKs & Libraries
- Functional Applications - Enterprise Asset Management Systems (EAM)
Applicable Industries
- Packaging
- Plastics
Applicable Functions
- Logistics & Transportation
Use Cases
- Intelligent Packaging
- Visual Quality Detection
The Challenge
Bantam Materials, a company dedicated to cleaning up the ocean with their Prevented Ocean Plastic brand, faced a significant challenge in managing and sharing their visual assets. The company, which sources waste plastic bottles from developing countries to turn into RPET flake for use in packaging by well-known brands, needed to share their story effectively. They captured images and videos during their visits to recyclers in Indonesia, South America, and North Africa, highlighting areas where plastic pollution was prevalent. However, these assets were disorganized, saved on servers, desktops, and Dropbox with no formal system in place for organization. Searching for a specific asset could take up to 45 minutes. With offices in the UK, Ireland, and Canada, and working with recyclers worldwide, Bantam needed a global solution to manage thousands of incoming photos and videos. They needed a tool to curate content for different audiences and share assets easily.
About The Customer
Bantam Materials is a London-based company on a mission to clean up the ocean with their Prevented Ocean Plastic brand, certified by Oceancycle. They have reinvented the packaging supply chain by sourcing waste plastic bottles from developing countries to turn into RPET flake, a recycled material used in packaging by well-known brands like Patagonia, The Body Shop, Lidl, and Sainsbury’s. Bantam is developing the largest commercial recycling program in the world and to certify with Oceancycle, they need to completely trace each bottle’s journey. They have offices in the UK, Ireland, and Canada and work with recyclers all over the world.
The Solution
Bantam identified Canto as the solution to their challenge. Canto provided a centralized and searchable asset library, bringing together all of Bantam’s Prevented Ocean Plastic images in one location, tagged with metadata. The team could arrange assets into folders and Portals for each audience, such as manufacturers, brand assets, social media, and PR. Canto’s advanced search made it easy for the team to find the images they were looking for. Bantam also used Canto Portals to create customized media packages for each customer, enabling new business growth. The tool allowed Bantam to win new international business despite travel restrictions, providing all the information customers needed at their fingertips. Bantam’s customers could find the media assets they needed with Canto’s powerful search function, and they and their partners could also add new media. Bantam also streamlined agency workflows by providing their external PR team access to all their videos and images at any time, anywhere in the world, through their PR Portal.
Operational Impact
Quantitative Benefit
Related Case Studies.
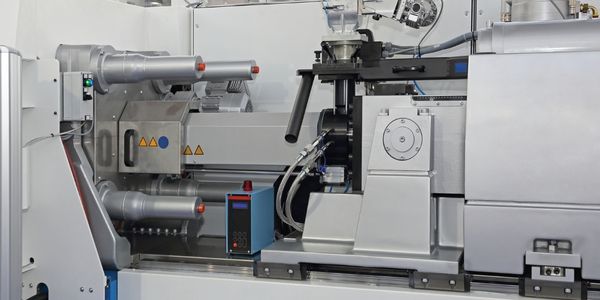
Case Study
Plastic Spoons Case study: Injection Moulding
In order to meet customer expectations by supplying a wide variety of packaging units, from 36 to 1000 spoons per package, a new production and packaging line needed to be built. DeSter wanted to achieve higher production capacity, lower cycle time and a high degree of operator friendliness with this new production line.
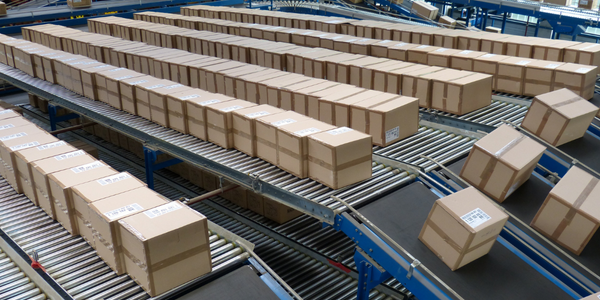
Case Study
IoT Data Analytics Case Study - Packaging Films Manufacturer
The company manufactures packaging films on made to order or configure to order basis. Every order has a different set of requirements from the product characteristics perspective and hence requires machine’s settings to be adjusted accordingly. If the film quality does not meet the required standards, the degraded quality impacts customer delivery causes customer dissatisfaction and results in lower margins. The biggest challenge was to identify the real root cause and devise a remedy for that.
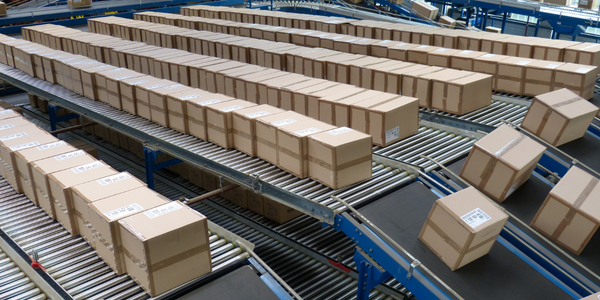
Case Study
Zenon the Ideal Basis for An Ergonomic HMI
KHS develops and produces machines and equipment for filling and packaging in the drinks industry. Because drinks manufacturing, filling and packaging consist of a number of highly complex processes, the user-friendly and intuitive operation of equipment is increasingly gaining in significance. In order to design these processes as simple as possible for the user, KHS decided to introduce a uniform, transparent and standardized solution to the company. The HMI interface should meet the requirement for people with different qualifications and enable them to work on a standard platform.
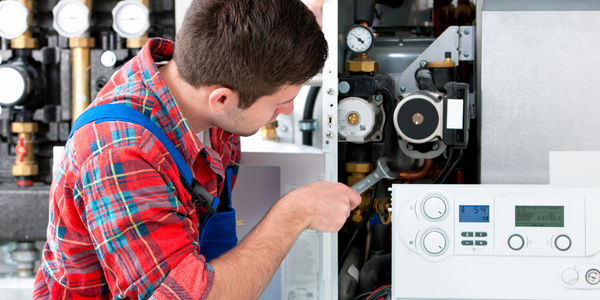
Case Study
Boiler Control System for Plastic Manufacturing Applications
Factory automation applications must be equipped to handle and monitor the myriads of information from attached devices. For plastic manufacturing applications, the boiler control system plays a critical role by gathering and regulating information to ensure production is accurate and smooth. In this particular case, the customer combines eight subsystems that include power meters, water meters, alarm output, displays, and I/O status to be controlled by several intelligent controllers with Modbus RTU interface. The Modbus TCP protocol is used for this application due to the distance. System Requirements: • Modbus serial to Modbus TCP translation • Multiple slaves/masters support • Automatic Modbus TCP response time detection
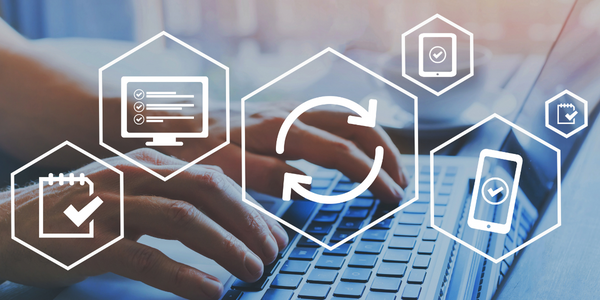
Case Study
Ascend Performance Materials Case Study
Ascend operations must access multiple software systems to manage day-to-day operations in an effective and secure manner. These systems generate large sets of data which contain critical information pertaining to management systems, planning and cost information in business systems and energy consumption. As a result, Ascend management was challenged with creating relevant reports reflecting performance measures in overall context of their operational process. The company’s previous process entailed collecting and analyzing data manually which was not effective, since the information collected was generated after the fact, and was too complex for collaborative use across the organization.
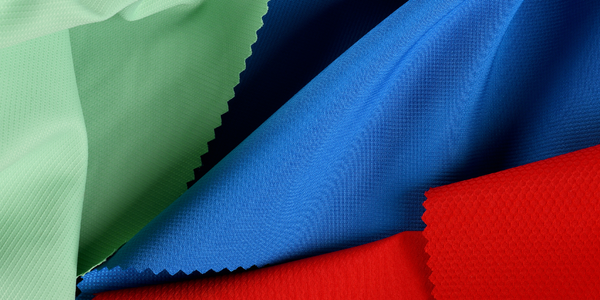
Case Study
Remake Enterprise-to-production System
The client was running a legacy material flow tracking system and wanted to replace the system with a more effective one as the system was increasingly expensive to maintain and support and also was not extendable. The client's IT landscape was filled with modern applications and it was difficult to interface the material flow tracking system with modern applications.