Download PDF
BatchMaster Enables Global Supplier in Fulfilling Manufacturing Commitments, Saving Time and Money
Technology Category
- Application Infrastructure & Middleware - Data Exchange & Integration
Applicable Industries
- Paper & Pulp
Applicable Functions
- Discrete Manufacturing
- Procurement
Use Cases
- Inventory Management
- Predictive Replenishment
Services
- Data Science Services
The Challenge
International Paper, a global paper and packaging company, was facing challenges with its manufacturing system. The company's water-based flexographic ink business was struggling to meet customer requirements due to major fluctuations in customer order patterns. The company had to maintain sizable safety stocks or pay premium prices for delivery of short items to meet customer requirements. As the scale of business grew, so did the severity of this problem. The company realized that the manufacturing system then in place, a semi-custom mainframe-based inventory, sales and purchase order management system, was no longer adequate to support their business. They needed a system that provided immediate access to inventories from all ink manufacturing sites within the company and updated inventories as batches were closed at the various plants.
About The Customer
International Paper (NYSE:IP) is a global paper and packaging company with manufacturing operations in North America, Europe, Latin America, Russia, Asia and North Africa. Its businesses include uncoated papers and industrial and consumer packaging, complemented by Xpedx, the company's North American distribution company. Headquartered in Memphis, Tenn., the company employs more than 50,000 people in more than 20 countries. In 2008, International Paper purchased the CBPR (Containerboard, Packaging and Recycling) Division of the global supplier of Weyerhaeuser, who grows and harvests trees, builds homes, and makes forest products essential to everyday lives. Weyerhaeuser, at the time of the acquisition, was a long-time user of BatchMaster Software's solutions for everything from formula management to (today) Enterprise Resource Planning (ERP).
The Solution
The company decided to implement BatchMaster ERP Coatings. The transition from DOS and Btrieve to Windows and MS SQL was a challenge, but the BatchMaster support team worked diligently with them on all issues. One of the most important advances from the second to the fifth generation of BatchMaster is BatchMaster Enterprise's foundations in Microsoft SQL. This allowed the company to develop new “Crystal Reports,” accessing SQL records in BatchMaster Enterprise, to better manage their business. Real-time access to updated inventory gave Purchasing staff the ability to avoid critical shortages and reduce the amount of periodic adjustments in inventory for discrepancies between virtual and physical counts. On the formulation side, SQL queries made possible the easy analysis of any “problem formula,” that is any formula with a plus or minus 10% content for critical ingredients.
Operational Impact
Related Case Studies.
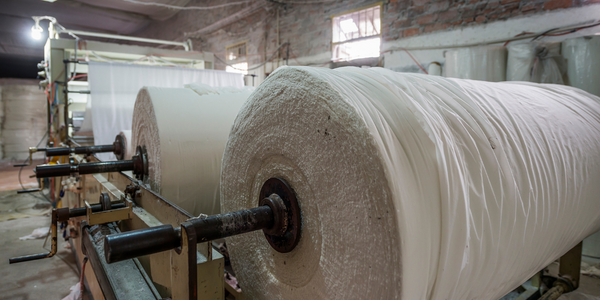
Case Study
Wireless Improves Efficiency in Compressed Air Systems
Hollingsworth and Vose wanted to improve the efficiency of their compressed air system, lower the electricity expense component of manufacturing cost in their commodity industry, and conserve energy leading to lowered greenhouse gas emissions. Compressed air systems degrade over time and become leaky and inefficient. Hollingsworth and Vose wanted to increase the frequency of system inspections without paying the high cost of manual labor.
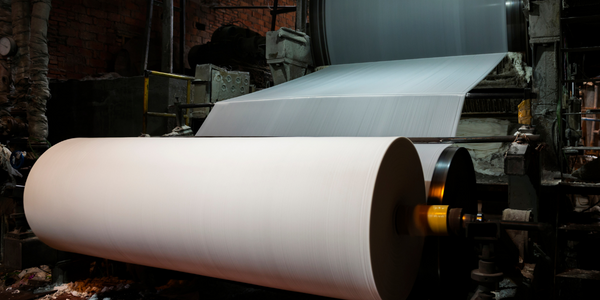
Case Study
Process Predictive Analysis in Pulp and Paper Mill
Common paper breaks consequently lead up to 60 minutes of downtime, delaying a potential $10K per hour of production value process. Thus, defective products cause financial and damage company's reputation. Improving quality and reducing defect rates can generate millions of dollars of revenue per year for your company.
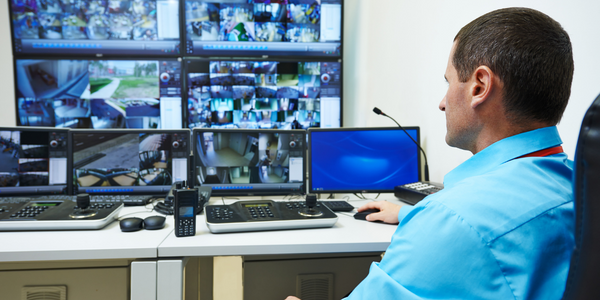
Case Study
Industrial Video Monitoring for Security and Regulatory Compliance
Because of the Stevenson mill’s proximity to the Tennessee River, WestRock was required by the USCG to comply with the Maritime Security 33CFR (MARSEC) regulations. WestRock needed a video security system but wanted to add other applications not required by the government, such as video process monitoring, condition monitoring, and wireless network management. WestRock needed a reliable video solution to avoid the compliance fines and possible security risks – but the solution needed to be implemented in the most cost-effective manner possible.
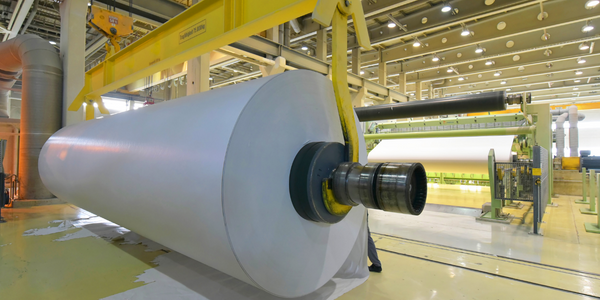
Case Study
ECOsine Active Increased Reliability in the Paper Industry
The paper and pulp industry is interlinking intelligent hi-tech machines to highly efficient production lines. Higher power DC and AC motor drives perform the automation tasks. Every kind of interference that negatively affects the reliability and safety of the installation may lead to production downtime and consequently to significant financial losses. AC and DC motor drives are so-called non-linear loads as they draw a nonsinusoidal current from the grid. Resulting harmonics of current and voltage can interfere with the operation of nearby consumers and overload the electrical infrastructure. In this particular application, the load cycles of the drives often caused interruptions in the production process because of disturbances coupling into the fieldbus system.