Download PDF
Buyers Products Boosts Productivity and Service with Manhattan Scale™
Technology Category
- Functional Applications - Warehouse Management Systems (WMS)
- Functional Applications - Enterprise Resource Planning Systems (ERP)
Applicable Industries
- Automotive
- Equipment & Machinery
Applicable Functions
- Warehouse & Inventory Management
- Logistics & Transportation
Use Cases
- Warehouse Automation
- Inventory Management
- Supply Chain Visibility
Services
- System Integration
- Software Design & Engineering Services
The Challenge
Buyers Products faced significant challenges due to inefficient, labor-intensive processes and tremendous growth in their supply chain operations. The company had been using manual, paper-based systems which required keypunching all data, leading to inefficiencies. With the move to a new 150,000 square foot distribution center, nearly doubling their capacity, Buyers needed to significantly increase efficiency to manage their growing inventory and product flow. Additionally, customers were increasingly requesting more services and documentation, including EDI capability, compliance labeling, and advance ship notices (ASNs).
About The Customer
Established in 1946, Buyers Products Company started as a distributor of truck and trailer components and has grown to become a leading manufacturer in the mobile equipment industry. The company boasts vertically integrated manufacturing capabilities, including forging, stamping, laser cutting, CNC machining, robotic welding, powder coating, assembly, and retail-oriented packaging. With over 250,000 square feet of manufacturing facilities, Buyers is committed to listening to its customers and improving profitability and productivity while enhancing the quality of its products and services. The company recently moved into a new 150,000 square foot distribution center to address its tremendous growth, nearly doubling its capacity.
The Solution
To address the inefficiencies and support their growth, Buyers Products chose Manhattan SCALE for its functionality and .NET-based platform. The solution was implemented in their new distribution center along with a new ERP system. Manhattan Associates provided a team to assist with the implementation process, and Buyers also collaborated with True Fit Systems to develop the ERP interface. The ERP system feeds orders every eight minutes to Warehouse Management, and orders are waved every two hours throughout the day. A conveyor system carries orders to the picking area, where they are directed to one of two packing areas for either parcel carrier or less-than-truckload (LTL) or truckload (TL) shipping. Manhattan SCALE is used for all warehouse functions, including receiving, putaway, replenishment, picking, packing, creating shipping documentation, and cycle counting. In the evening, the system uploads all completed orders to ERP for invoicing.
Operational Impact
Quantitative Benefit
Related Case Studies.
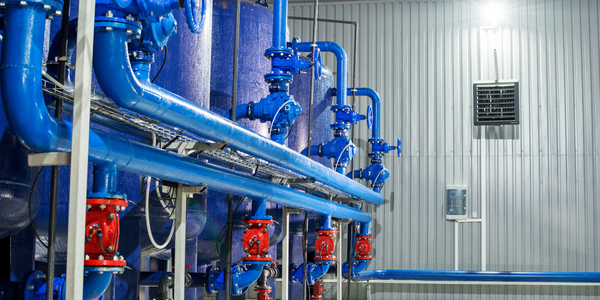
Case Study
Smart Water Filtration Systems
Before working with Ayla Networks, Ozner was already using cloud connectivity to identify and solve water-filtration system malfunctions as well as to monitor filter cartridges for replacements.But, in June 2015, Ozner executives talked with Ayla about how the company might further improve its water systems with IoT technology. They liked what they heard from Ayla, but the executives needed to be sure that Ayla’s Agile IoT Platform provided the security and reliability Ozner required.
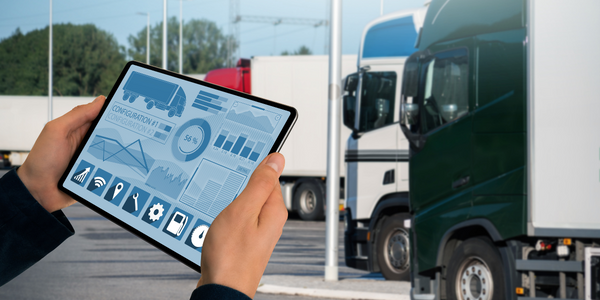
Case Study
IoT enabled Fleet Management with MindSphere
In view of growing competition, Gämmerler had a strong need to remain competitive via process optimization, reliability and gentle handling of printed products, even at highest press speeds. In addition, a digitalization initiative also included developing a key differentiation via data-driven services offers.
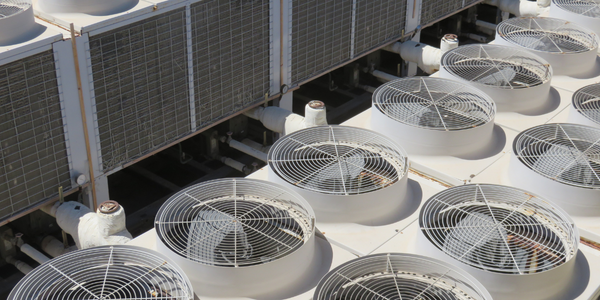
Case Study
Predictive Maintenance for Industrial Chillers
For global leaders in the industrial chiller manufacturing, reliability of the entire production process is of the utmost importance. Chillers are refrigeration systems that produce ice water to provide cooling for a process or industrial application. One of those leaders sought a way to respond to asset performance issues, even before they occur. The intelligence to guarantee maximum reliability of cooling devices is embedded (pre-alarming). A pre-alarming phase means that the cooling device still works, but symptoms may appear, telling manufacturers that a failure is likely to occur in the near future. Chillers who are not internet connected at that moment, provide little insight in this pre-alarming phase.
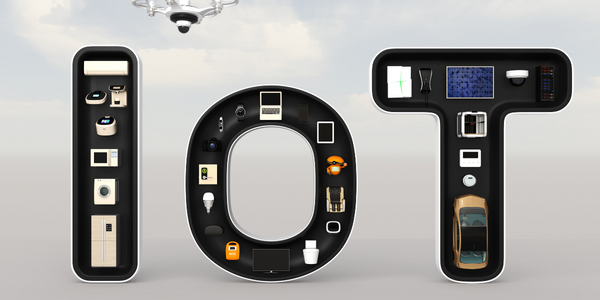
Case Study
Premium Appliance Producer Innovates with Internet of Everything
Sub-Zero faced the largest product launch in the company’s history:It wanted to launch 60 new products as scheduled while simultaneously opening a new “greenfield” production facility, yet still adhering to stringent quality requirements and manage issues from new supply-chain partners. A the same time, it wanted to increase staff productivity time and collaboration while reducing travel and costs.
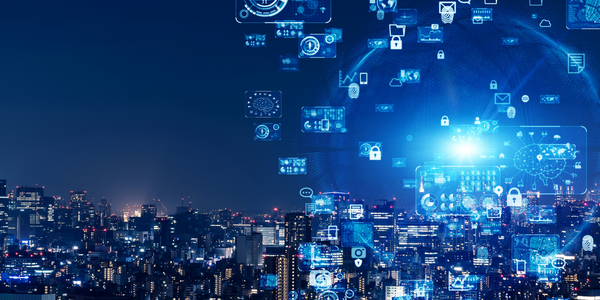
Case Study
Integration of PLC with IoT for Bosch Rexroth
The application arises from the need to monitor and anticipate the problems of one or more machines managed by a PLC. These problems, often resulting from the accumulation over time of small discrepancies, require, when they occur, ex post technical operations maintenance.
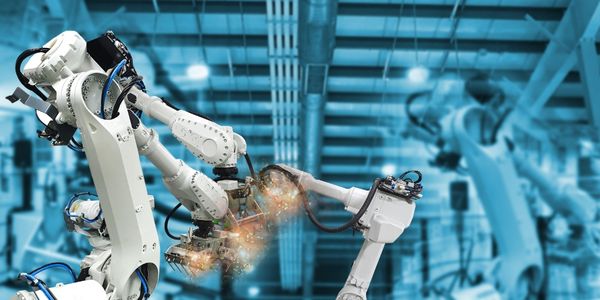
Case Study
Robot Saves Money and Time for US Custom Molding Company
Injection Technology (Itech) is a custom molder for a variety of clients that require precision plastic parts for such products as electric meter covers, dental appliance cases and spools. With 95 employees operating 23 molding machines in a 30,000 square foot plant, Itech wanted to reduce man hours and increase efficiency.