Download PDF
Case Study: Surmotech
Technology Category
- Application Infrastructure & Middleware - Data Exchange & Integration
Applicable Industries
- Electronics
- Telecommunications
Applicable Functions
- Discrete Manufacturing
- Quality Assurance
Use Cases
- Manufacturing System Automation
- Predictive Maintenance
Services
- System Integration
- Software Design & Engineering Services
The Challenge
Late in 2010, a Surmotech customer with a highly complex, dense PCBA required complete product, materials, and process traceability. While it was possible to fulfill these requirements using the existing systems, it would have adversely impacted throughput. Surmotech began investigating an integrated solution. The challenge was to find a system to manage the setup of their machines, track the components and units, and finally compile data from each point on the manufacturing floor to meet the end customer requirements for traceability and historical genealogy. Surmotech explored several alternative systems but most of these lacked the depth and scope to integrate the multiple machines and data points of their process.
About The Customer
Surmotech Inc., headquartered in Victor, New York, is a full-service electronic contract manufacturer. Since 1991, they have provided a complete range of manufacturing, assembly, and test services to various industries. These industries include the military, medical, industrial, optical, and telecommunications industries, as well as consumer markets. Surmotech is known for its capacity and capability in manufacturing lines and embedded equipment, which has allowed them to meet complex customer requirements. They have been utilizing the AEGIS NPI platform over many years for process development.
The Solution
Surmotech decided to expand their existing AEGIS NPI platform into an AEGIS MOS system. The AEGIS MOS team proposed a modular and scalable upgrade path from their existing platform. The implementation was launched with the first pre-production runs that met the customer’s requirements for traceability. The AEGIS MOS software collects data and distributes it into reports, visualizations, and real-time dashboards, which are used to constantly improve quality and efficiency. Traceability of every product is achieved while failures and rejections can be identified and eliminated before they become an issue for the customer. After the successful launch of the AEGIS MOS with that initial customer, Surmotech began full implementation across their entire customer base. This exercise focused on integrating all machines across all lines, enabling full traceability of process, materials, and production.
Operational Impact
Quantitative Benefit
Related Case Studies.
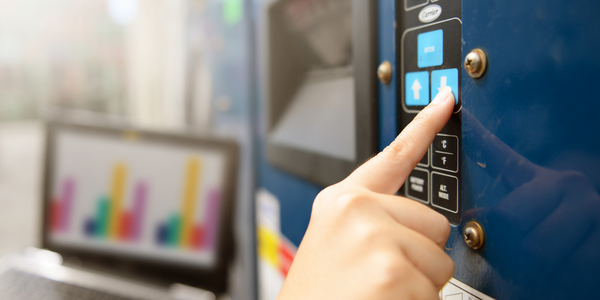
Case Study
Remote Temperature Monitoring of Perishable Goods Saves Money
RMONI was facing temperature monitoring challenges in a cold chain business. A cold chain must be established and maintained to ensure goods have been properly refrigerated during every step of the process, making temperature monitoring a critical business function. Manual registration practice can be very costly, labor intensive and prone to mistakes.
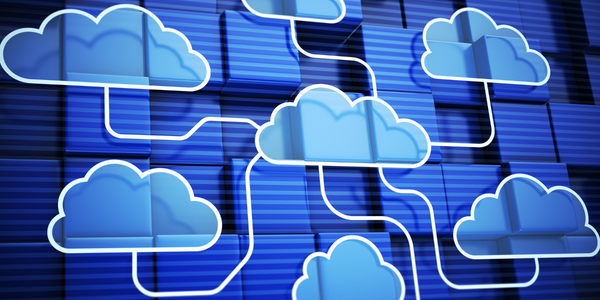
Case Study
Cloud Solution for Energy Management Platform-Schneider Electric
Schneider Electric required a cloud solution for its energy management platform to manage high computational operations, which were essential for catering to client requirements. As the business involves storage and analysis of huge amounts of data, the company also needed a convenient and scalable storage solution to facilitate operations efficiently.
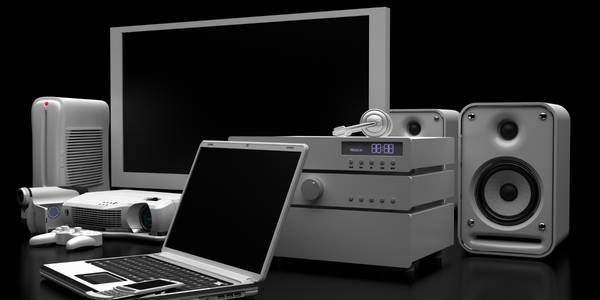
Case Study
Leveraging the IoT to Gain a Competitive Edge in International Competition
Many large manufacturers in and outside Japan are competing for larger market share in the same space, expecting a growing demand for projectors in the areas of entertainment, which requires glamor and strong visual performance as well as digital signage that can attract people’s attention. “It is becoming more and more difficult to differentiate ourselves with stand-alone hardware products,” says Kazuyuki Kitagawa, Director of Service & Support at Panasonic AVC Networks. “In order for Panasonic to grow market share and overall business, it is essential for us to develop solutions that deliver significant added value.” Panasonic believes projection failure and quality deterioration should never happen. This is what and has driven them to make their projectors IoT-enabled. More specifically, Panasonic has developed a system that collects data from projectors, visualizes detailed operational statuses, and predicts issues and address them before failure occurs. Their projectors are embedded with a variety of sensors that measure power supply, voltage, video input/ output signals, intake/exhaust air temperatures, cooling fan operations, and light bulb operating time. These sensors have been used to make the projector more intelligent, automatically suspending operation when the temperature rises excessively, and automatically switching light bulbs. Although this was a great first step, Panasonic projectors were still not equipped with any capability to send the data over a network.