Download PDF
Cifarma Earns Client Trust in Document Management and Maintenance with SoftExpert
Technology Category
- Application Infrastructure & Middleware - Data Exchange & Integration
- Functional Applications - Computerized Maintenance Management Systems (CMMS)
- Functional Applications - Enterprise Resource Planning Systems (ERP)
Applicable Industries
- Pharmaceuticals
Applicable Functions
- Maintenance
- Quality Assurance
Use Cases
- Regulatory Compliance Monitoring
Services
- Software Design & Engineering Services
- System Integration
The Challenge
The accelerated growth of the company and search for competitiveness prompted Cifarma to seek an efficient online document management system with cutting-edge resources. They needed to save time and boost efficiency in document control while also managing equipment maintenance effectively. The company faced challenges in unifying processes across its units, ensuring document security, and complying with regulatory norms.
About The Customer
Founded in 1999, Cifarma is a pharmaceutical company that produces a wide range of medications, including liquid medications like syrups and oral solutions, semi-solid medications like creams and ointments, and an entire line of hormones. The company operates from a 100,000 m2 industrial facility and has a portfolio of 91 products divided into three commercial lines: Pharma, MIP & Consumer, and Mabra. Cifarma also outsources production to other laboratories and serves more than 30 therapeutic classes through 50 exclusive and semi-exclusive distributors.
The Solution
Cifarma adopted SoftExpert solutions, specifically SE Document and SE Maintenance, to address their challenges. These solutions provided the tools needed to improve the unification process at their units, allowing for the sharing of common documents while protecting private files. The solutions enhanced the security and efficiency of Cifarma's Quality System document management, enabling control over the creation, revision, and cancellation of documents. The user-friendly search function improved document visibility among employees from different sectors. Additionally, the solutions automated document indexation, storage, publication, and distribution processes, ensuring immediate access to the latest document versions across the company.
Operational Impact
Quantitative Benefit
Related Case Studies.
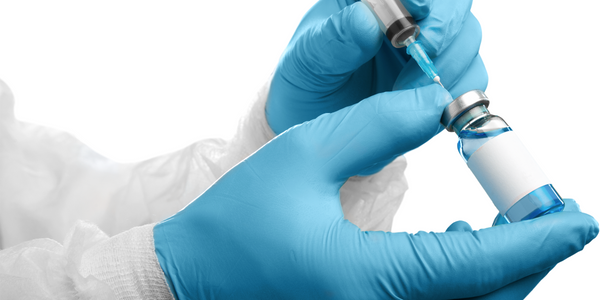
Case Study
Case Study: Pfizer
Pfizer’s high-performance computing software and systems for worldwide research and development support large-scale data analysis, research projects, clinical analytics, and modeling. Pfizer’s computing services are used across the spectrum of research and development efforts, from the deep biological understanding of disease to the design of safe, efficacious therapeutic agents.
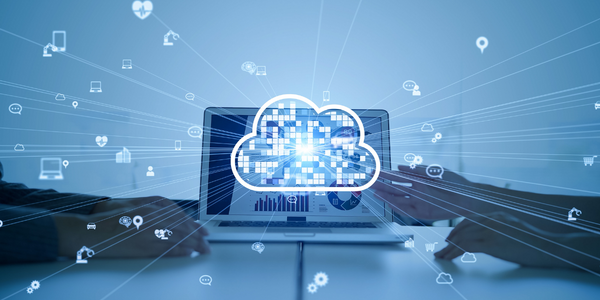
Case Study
Fusion Middleware Integration on Cloud for Pharma Major
Customer wanted a real-time, seamless, cloud based integration between the existing on premise and cloud based application using SOA technology on Oracle Fusion Middleware Platform, a Contingent Worker Solution to collect, track, manage and report information for on-boarding, maintenance and off-boarding of contingent workers using a streamlined and Integrated business process, and streamlining of integration to the back-end systems and multiple SaaS applications.
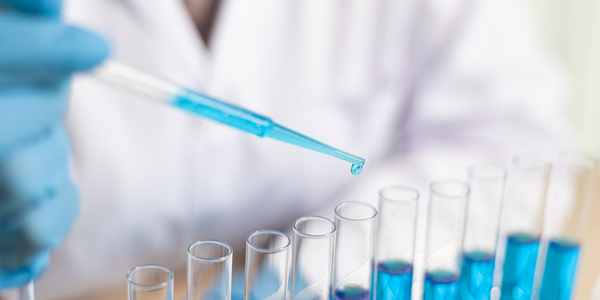
Case Study
Process Control System Support
In many automated production facilities, changes are made to SIMATIC PCS 7 projects on a daily basis, with individual processes often optimised by multiple workers due to shift changes. Documentation is key here, as this keeps workers informed about why a change was made. Furthermore, SIMATIC PCS 7 installations are generally used in locations where documentation is required for audits and certification. The ability to track changes between two software projects is not only an invaluable aid during shift changes, but also when searching for errors or optimising a PCS 7 installation. Every change made to the system is labour-intensive and time-consuming. Moreover, there is also the risk that errors may occur. If a change is saved in the project, then the old version is lost unless a backup copy was created in advance. If no backup was created, it will no longer be possible to return to the previous state if and when programming errors occur. Each backup denotes a version used by the SIMATIC PCS 7 system to operate an installation. To correctly interpret a version, information is required on WHO changed WHAT, WHERE, WHEN and WHY: - Who created the version/who is responsible for the version? - Who released the version? - What was changed in the version i.e. in which block or module of the SIMATIC PCS 7 installation were the changes made? - When was the version created? Is this the latest version or is there a more recent version? - Why were the changes made to the version? If they are part of a regular maintenance cycle, then is the aim to fix an error or to improve production processes? - Is this particular version also the version currently being used in production? The fact that SIMATIC PCS 7 projects use extremely large quantities of data complicates the situation even further, and it can take a long time to load and save information as a result. Without a sustainable strategy for operating a SIMATIC PCS 7 installation, searching for the right software version can become extremely time-consuming and the installation may run inefficiently as a result.
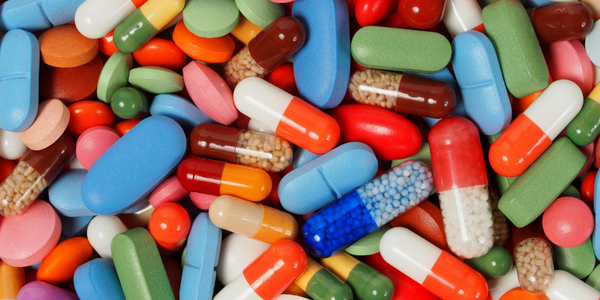
Case Study
Drug Maker Takes the Right Prescription
China Pharm decided to build a cloud-based platform to support the requirements of IT planning for the next five to ten years which includes a dynamic and scalable mail resource pool platform. The platform needed to have the following functions: all nodes support redundancy, ensuring service continuity and good user experience, simple and easy-to-use user interfaces for end users and administrators and good compatibility and supports smooth capacity expansion.
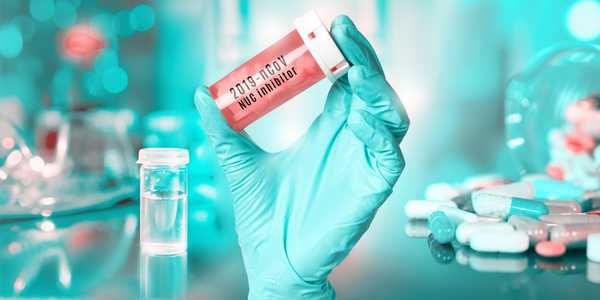
Case Study
ELI LILLY ADOPTS MICROMEDIA’S ALERT NOTIFICATION SYSTEM
Pharmaceutical production is subject to a strict set of enforced rules that must be adhered to and compliance to these standards is critically necessary. Due to the efforts of WIN 911’s strategic partner Micromedia, Lilly was able to adopt an alarm notification infrastructure that integrated smoothly with their existing workflows and emergency hardware and protocols. These raw energy sources enable the industrial process to function: electricity, WIN-911 Software | 4020 South Industrial Drive, Suite 120 | Austin, TX 78744 USA industrial steam, iced water, air mixtures of varying quality. Refrigeration towers, boilers and wastewater are monitored by ALERT. Eli Lilly identified 15000 potential variables, but limitations compelled them to chisel the variable list down to 300. This allowed all major alarms to be covered including pressure, discharge, quantity of waste water discharged,temperature, carbon dioxide content, oxygen & sulphur content, and the water’s pH.