Download PDF
Consolidated Container Obtains a Dramatic Decrease in Cost of Goods Sold Within Three Months of Deploying GainSeeker Suite
Technology Category
- Functional Applications - Manufacturing Execution Systems (MES)
- Analytics & Modeling - Predictive Analytics
Applicable Industries
- Packaging
- Consumer Goods
Applicable Functions
- Quality Assurance
- Business Operation
Use Cases
- Predictive Maintenance
- Factory Operations Visibility & Intelligence
- Process Control & Optimization
Services
- System Integration
- Software Design & Engineering Services
The Challenge
Consolidated Container Company (CCC) faced significant challenges due to outdated legacy information systems and a lack of standardized quality data systems across its 59 manufacturing facilities. This inconsistency led to difficulties in obtaining accurate, actionable quality information, with some plants relying on archaic technology and paper-based workflows. The lack of a shared data platform made it hard for leaders to gain visibility into plant operations, resulting in quality issues that impacted customer satisfaction. The urgency to address these challenges increased when new ownership and senior leadership, experienced in industries with real-time Statistical Process Control data, took over in 2012. They demanded corporate-wide visibility into quality data, necessitating an evolution in CCC's quality data systems.
About The Customer
Consolidated Container Company (CCC) is a leading supplier of rigid plastic packaging in North America, operating 59 manufacturing facilities and employing 2,300 people. The company produces a wide range of plastic packaging solutions for various industries, including consumer goods and packaging. Despite its extensive operations, CCC faced challenges with outdated legacy systems and a lack of standardized quality data systems across its facilities. This inconsistency in technology and data management hindered the company's ability to maintain high-quality standards and meet customer expectations. The company's new leadership, with a background in industries that prioritize real-time data visibility, recognized the need for a comprehensive solution to improve quality control and operational efficiency.
The Solution
Matt Simpson, Corporate Quality Systems Manager at CCC, was tasked with finding a single system to deploy across the company to improve quality control and operational efficiency. After developing a list of prioritized features and functionalities, Simpson identified ease of use for operators, data analysis capabilities, and system flexibility as top priorities. He surveyed the plants to determine the software being used for Statistical Process Control and identified three potential solutions, including GainSeeker Suite. GainSeeker Suite emerged as the clear front runner due to its superior ease of use, data analysis capabilities, and flexibility. The system allowed operators to easily collect and analyze data, and its customization options enabled it to adapt to various workflows. Simpson and his team piloted the solution in one plant, using live data from CCC's production lines, and found that GainSeeker Suite met their needs effectively.
Operational Impact
Quantitative Benefit
Related Case Studies.
.png)
Case Study
Improving Vending Machine Profitability with the Internet of Things (IoT)
The vending industry is undergoing a sea change, taking advantage of new technologies to go beyond just delivering snacks to creating a new retail location. Intelligent vending machines can be found in many public locations as well as company facilities, selling different types of goods and services, including even computer accessories, gold bars, tickets, and office supplies. With increasing sophistication, they may also provide time- and location-based data pertaining to sales, inventory, and customer preferences. But at the end of the day, vending machine operators know greater profitability is driven by higher sales and lower operating costs.
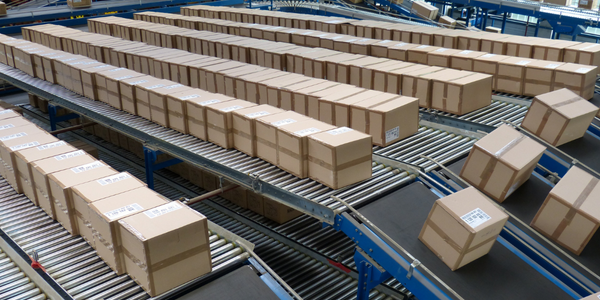
Case Study
IoT Data Analytics Case Study - Packaging Films Manufacturer
The company manufactures packaging films on made to order or configure to order basis. Every order has a different set of requirements from the product characteristics perspective and hence requires machine’s settings to be adjusted accordingly. If the film quality does not meet the required standards, the degraded quality impacts customer delivery causes customer dissatisfaction and results in lower margins. The biggest challenge was to identify the real root cause and devise a remedy for that.
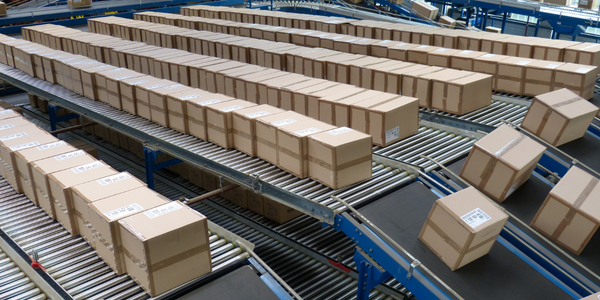
Case Study
Zenon the Ideal Basis for An Ergonomic HMI
KHS develops and produces machines and equipment for filling and packaging in the drinks industry. Because drinks manufacturing, filling and packaging consist of a number of highly complex processes, the user-friendly and intuitive operation of equipment is increasingly gaining in significance. In order to design these processes as simple as possible for the user, KHS decided to introduce a uniform, transparent and standardized solution to the company. The HMI interface should meet the requirement for people with different qualifications and enable them to work on a standard platform.
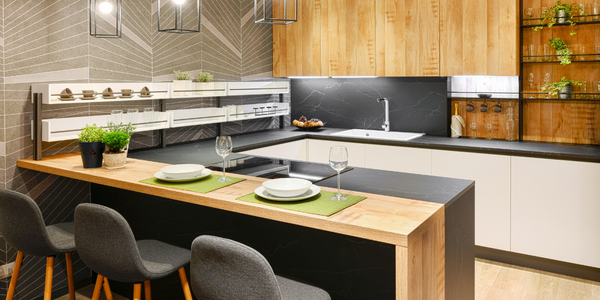
Case Study
Series Production with Lot-size-1 Flexibility
Nobilia manufactures customized fitted kitchens with a lot size of 1. They require maximum transparency of tracking design data and individual processing steps so that they can locate a particular piece of kitchen furniture in the sequence of processes.