Download PDF
Container Centralen AS Counterfeit solving RFID solution improves supply chain efficiency
Technology Category
- Sensors - RFID Readers
- Application Infrastructure & Middleware - Data Exchange & Integration
Applicable Functions
- Logistics & Transportation
Use Cases
- Track & Trace of Assets
- Supply Chain Visibility
Services
- System Integration
- Software Design & Engineering Services
The Challenge
Container Centralen, a provider of reusable plant and flower shipping containers in Europe, maintains over 3.5 million containers in its inventory, which circulates through 60 depots spread across Europe. For years, the company has faced a significant challenge: counterfeiting. Up to 20 percent of the container pool is counterfeit, creating a twofold challenge to CC. First, because the reusable containers belong to CC, it is responsible for their cleaning, maintenance, repair and replacement. Second, since customers are using more containers than they are paying for, CC is losing lease revenue while being responsible for containers it does not own.
About The Customer
Container Centralen is a company that owns and manages a system of returnable containers in the European Green Sector supply chain infrastructure. The system is used by several stakeholders in the sector including growers, auction houses, transporters, exporters etc. and is operated across 22 countries. The company provides reusable plant and flower shipping containers in Europe and maintains over 3.5 million containers in its inventory. These containers circulate through 60 depots spread across Europe.
The Solution
By implementing a custom RFID control system, Container Centralen has created a way for the supply chain to transform itself, without having to take on the cost of creating it. The solution — the first of its kind in the industry — aims to eliminate the problem of counterfeit containers once and for all. An elegant aspect of CC’s approach is that it does not matter whether a tag is attached to a counterfeit container or a genuine one, what matters is the total number of tagged containers in circulation. Implementing the solution also benefits CC’s customers, since information associated with each tag can also provide unprecedented insight into the supply chain. For example, the ability to tell exactly what is in each container without physically inspecting it enables customers to proactively manage their product shipments to maximize efficiency. To facilitate this industry transformation, CC is providing the necessary application interfaces free to any customer who wishes to develop the capability.
Operational Impact
Quantitative Benefit
Related Case Studies.
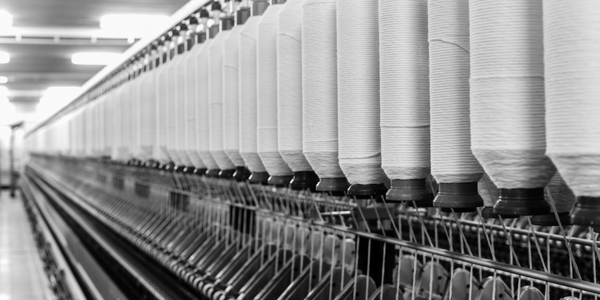
Case Study
IoT Applications and Upgrades in Textile Plant
At any given time, the textile company’s manufacturing facility has up to 2,000 textile carts in use. These carts are pushed from room to room, carrying materials or semi-finished products. Previously, a paper with a hand-written description was attached to each cart. This traditional method of processing made product tracking extremely difficult. Additionally, making sure that every cart of materials or semi-finished products went to its correct processing work station was also a problem. Therefore, the company desired an intelligent solution for tracking assets at their factories. They also wanted a solution that would help them collect process data so they could improve their manufacturing efficiency.
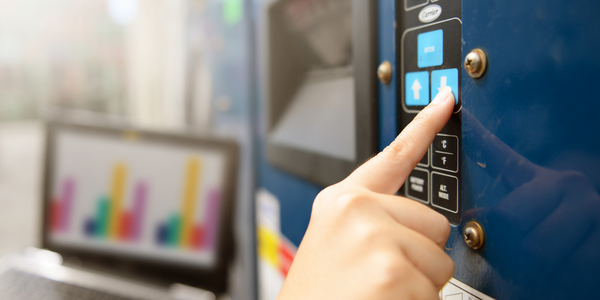
Case Study
Remote Temperature Monitoring of Perishable Goods Saves Money
RMONI was facing temperature monitoring challenges in a cold chain business. A cold chain must be established and maintained to ensure goods have been properly refrigerated during every step of the process, making temperature monitoring a critical business function. Manual registration practice can be very costly, labor intensive and prone to mistakes.
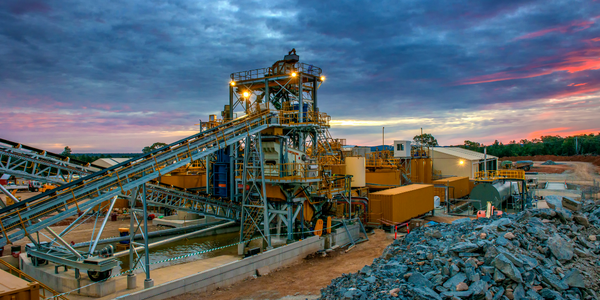
Case Study
Goldcorp: Internet of Things Enables the Mine of the Future
Goldcorp is committed to responsible mining practices and maintaining maximum safety for its workers. At the same time, the firm is constantly exploring ways to improve the efficiency of its operations, extend the life of its assets, and control costs. Goldcorp needed technology that can maximize production efficiency by tracking all mining operations, keep employees safe with remote operations and monitoring of hazardous work areas and control production costs through better asset and site management.
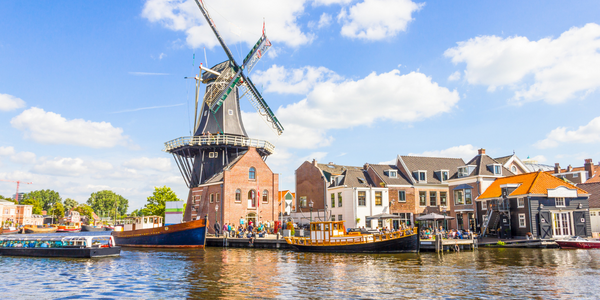
Case Study
Buoy Status Monitoring with LoRa
The Netherlands are well-known for their inland waterways, canals, sluices and of course port activities. The Dutch Ministry of Infrastructure indicates that there are thousands of buoys and fixed items in and near water environments that would profit from IoT monitoring. One of the problems with buoys for example, is that they get hit by ships and the anchor cable breaks. Without connectivity, it takes quite some time to find out that something has happened with that buoy. Not to mention the costs of renting a boat to go to the buoy to fix it. Another important issue, is that there is no real-time monitoring of the buoys at this moment. Only by physically visiting the object on the water, one gains insight in its status.
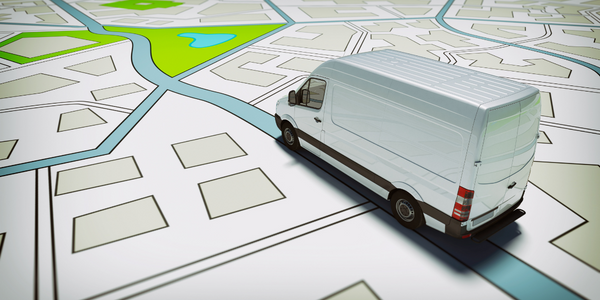
Case Study
IoT Based Asset Tracking System
The existing system used by the customer could only track a few thousand assets and was able to generate only a few standard set of reports. As the number of assets tracked grew exponentially, the system started to break at the seams. The Tracking devices were from different manufacturers following different protocols. There was no proper integration among the devices to send instant alerts. There are thousands of tracking devices spread across multiple geographies, that are moving. The configuration and troubleshooting of these devices incurred heavy costs, which was a logistics challenge. The existing system did not provide sophisticated Analytics, Business Intelligence and Insights from the data