Download PDF
DECKED: Revolutionizing Storage Solutions for Pickup Trucks
Technology Category
- Application Infrastructure & Middleware - Database Management & Storage
- Infrastructure as a Service (IaaS) - Cloud Storage Services
Applicable Industries
- Automotive
- Retail
Applicable Functions
- Product Research & Development
Use Cases
- Manufacturing Process Simulation
- Virtual Prototyping & Product Testing
The Challenge
The challenge faced by DECKED, a company founded by entrepreneurs Lance Meller and Jake Peters, was to create an innovative, robust, and useful storage solution for pickup trucks. The storage system needed to be able to withstand a load of 2,000 lbs, fit into a wide range of pickup models including those from Ford, GM, Chrysler, Toyota, and Nissan, and be manufactured for a compelling retail target price. The main issue was that the large capacity of a pickup truck often came at the expense of storage. The loading area was typically a simple box with no ability to store smaller items safely or secure them from theft. This presented an opportunity in the marketplace for a well-built alternative.
About The Customer
DECKED is a company founded by entrepreneurs Lance Meller and Jake Peters. They identified a gap in the market for a robust and useful storage solution for pickup trucks. The company's target customers are both commercial users and private owners of pickup trucks. The storage solution needed to be versatile enough to fit into a wide range of pickup models from various manufacturers including Ford, GM, Chrysler, Toyota, and Nissan. The company aimed to create a product that could withstand heavy loads, provide secure storage for smaller items, and be available at a compelling retail price.
The Solution
DECKED selected Altair ProductDesign as its partner to deliver conceptual design work along with advanced engineering and prototyping services. Altair ProductDesign’s industrial design group, Thinklabs, was invited to participate in the process of developing design themes encapsulating product branding, form, function, and aesthetics for the storage solution. Altair’s virtual simulation suite, HyperWorks, was used to investigate the structural performance of the product to see how it would perform in real conditions. Based on the results of these studies, Altair ProductDesign was able to suggest design changes to improve the performance of the product such as its load capacity. Altair ProductDesign also worked on simplifying the design and tooling, enabling DECKED to manufacture several variants of the product with the same tooling, thus keeping manufacturing costs low.
Operational Impact
Quantitative Benefit
Related Case Studies.
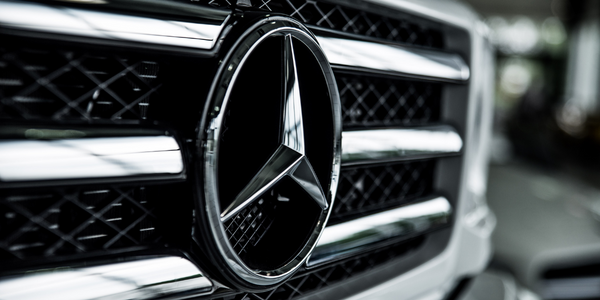
Case Study
Integral Plant Maintenance
Mercedes-Benz and his partner GAZ chose Siemens to be its maintenance partner at a new engine plant in Yaroslavl, Russia. The new plant offers a capacity to manufacture diesel engines for the Russian market, for locally produced Sprinter Classic. In addition to engines for the local market, the Yaroslavl plant will also produce spare parts. Mercedes-Benz Russia and his partner needed a service partner in order to ensure the operation of these lines in a maintenance partnership arrangement. The challenges included coordinating the entire maintenance management operation, in particular inspections, corrective and predictive maintenance activities, and the optimizing spare parts management. Siemens developed a customized maintenance solution that includes all electronic and mechanical maintenance activities (Integral Plant Maintenance).
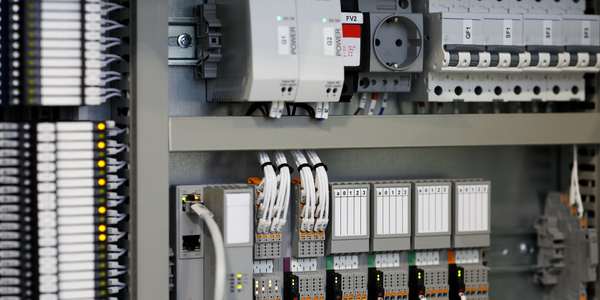
Case Study
Improving Production Line Efficiency with Ethernet Micro RTU Controller
Moxa was asked to provide a connectivity solution for one of the world's leading cosmetics companies. This multinational corporation, with retail presence in 130 countries, 23 global braches, and over 66,000 employees, sought to improve the efficiency of their production process by migrating from manual monitoring to an automatic productivity monitoring system. The production line was being monitored by ABB Real-TPI, a factory information system that offers data collection and analysis to improve plant efficiency. Due to software limitations, the customer needed an OPC server and a corresponding I/O solution to collect data from additional sensor devices for the Real-TPI system. The goal is to enable the factory information system to more thoroughly collect data from every corner of the production line. This will improve its ability to measure Overall Equipment Effectiveness (OEE) and translate into increased production efficiencies. System Requirements • Instant status updates while still consuming minimal bandwidth to relieve strain on limited factory networks • Interoperable with ABB Real-TPI • Small form factor appropriate for deployment where space is scarce • Remote software management and configuration to simplify operations