Download PDF
Digital Transformation in Orthotic and Prosthetic Design and Manufacturing
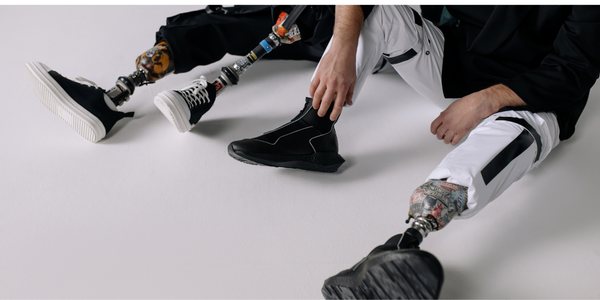
Technology Category
- Functional Applications - Manufacturing Execution Systems (MES)
- Sensors - Haptic Sensors
Applicable Industries
- Education
- Equipment & Machinery
Applicable Functions
- Product Research & Development
- Quality Assurance
Use Cases
- Additive Manufacturing
- Virtual Prototyping & Product Testing
Services
- Testing & Certification
- Training
The Challenge
The orthotics and prosthetics (O&P) industry has been largely dominated by manual craftsmanship. The challenge was to introduce digital technologies to orthotic and prosthetic design and manufacturing to support manual processes with digital workflows and tools. The two main challenges for orthotists and prosthetists were the production of the correct function and the suitability to the patient’s size and strength ratio, and developing an interface to the human body that can transfer and absorb force without causing chafing or similar irritations. The traditional workflow to produce a prosthetic begins with molding the body part with plaster, which maintains a few advantages over direct 3D scanning of the patient's limb. However, due to the high degree of manual work and experience orthotists and prosthetists bring to their work, it is nearly impossible to exactly replicate a good outcome.
The Customer
Häussler
About The Customer
Häussler is a well-known medical supply store in southern Germany. It was founded in 1916 by Thomas Oesterle as a specialized workshop for the main military hospital of the Ulm fortress. From the beginning, Oesterle valued collaboration with the medical sciences and worked in the hospital workshop. In 1984, Häussler opened a clinical workshop at the University and Rehabilitation Clinics of Ulm (RKU) to strengthen the connection between medical sciences and research. Häussler orthotists and prosthetists work closely with the Ulm University of Applied Sciences where medical engineering and biomechatronics expert Professor Dr. Felix Capanni works and conducts research. Steffen Matyssek, a former research assistant for Prof. Dr. Capanni, manages the Häussler research and development department.
The Solution
The Häussler medical supply store collaborated with the Biomechanics Research Group at the Ulm University of Applied Sciences in Ulm, Germany, and 3D expert and reseller Antonius Koester to define new digital processes. Their tools of choice are Geomagic Freeform organic 3D design software and Touch haptic devices by 3D Systems. The Dynabot automation tools in Geomagic Freeform help them simplify and accelerate the modeling process, allowing them to precisely reproduce well-fitting orthotics and prosthetics. The preferred tool for this design is Geomagic Freeform with the Touch haptic device. The Dynabot macro functionality in Geomagic Freeform allows them to automate recurring tasks and provides the user with the right tool for each step of the process. Such defined workflows automatically lead to standardization.
Operational Impact
Quantitative Benefit
Related Case Studies.
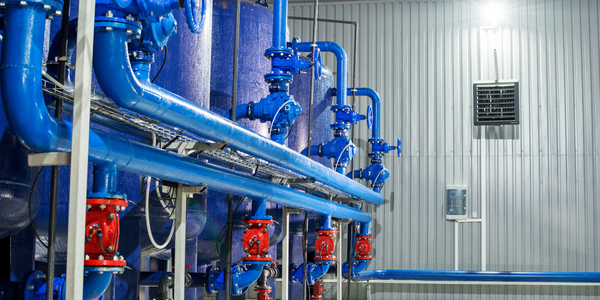
Case Study
Smart Water Filtration Systems
Before working with Ayla Networks, Ozner was already using cloud connectivity to identify and solve water-filtration system malfunctions as well as to monitor filter cartridges for replacements.But, in June 2015, Ozner executives talked with Ayla about how the company might further improve its water systems with IoT technology. They liked what they heard from Ayla, but the executives needed to be sure that Ayla’s Agile IoT Platform provided the security and reliability Ozner required.
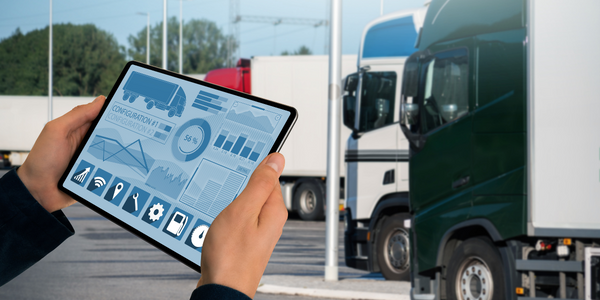
Case Study
IoT enabled Fleet Management with MindSphere
In view of growing competition, Gämmerler had a strong need to remain competitive via process optimization, reliability and gentle handling of printed products, even at highest press speeds. In addition, a digitalization initiative also included developing a key differentiation via data-driven services offers.
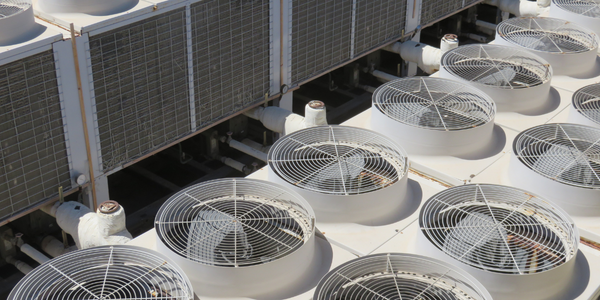
Case Study
Predictive Maintenance for Industrial Chillers
For global leaders in the industrial chiller manufacturing, reliability of the entire production process is of the utmost importance. Chillers are refrigeration systems that produce ice water to provide cooling for a process or industrial application. One of those leaders sought a way to respond to asset performance issues, even before they occur. The intelligence to guarantee maximum reliability of cooling devices is embedded (pre-alarming). A pre-alarming phase means that the cooling device still works, but symptoms may appear, telling manufacturers that a failure is likely to occur in the near future. Chillers who are not internet connected at that moment, provide little insight in this pre-alarming phase.
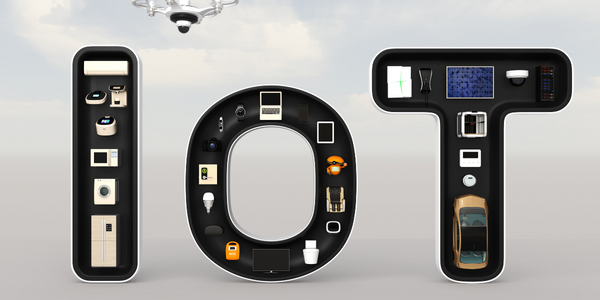
Case Study
Premium Appliance Producer Innovates with Internet of Everything
Sub-Zero faced the largest product launch in the company’s history:It wanted to launch 60 new products as scheduled while simultaneously opening a new “greenfield” production facility, yet still adhering to stringent quality requirements and manage issues from new supply-chain partners. A the same time, it wanted to increase staff productivity time and collaboration while reducing travel and costs.
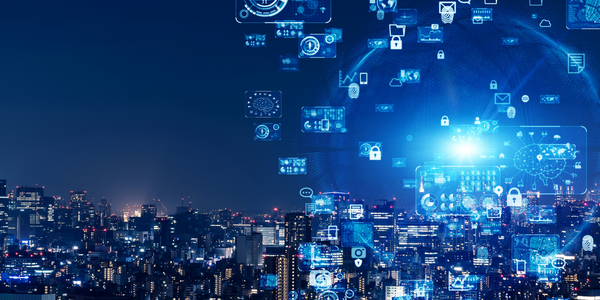
Case Study
Integration of PLC with IoT for Bosch Rexroth
The application arises from the need to monitor and anticipate the problems of one or more machines managed by a PLC. These problems, often resulting from the accumulation over time of small discrepancies, require, when they occur, ex post technical operations maintenance.
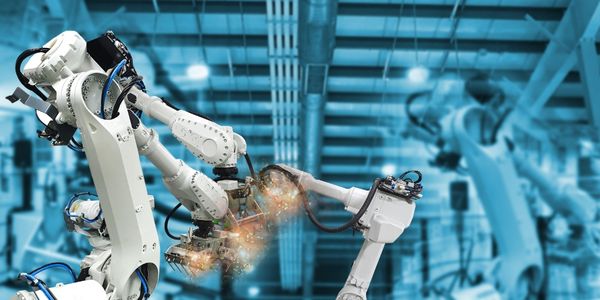
Case Study
Robot Saves Money and Time for US Custom Molding Company
Injection Technology (Itech) is a custom molder for a variety of clients that require precision plastic parts for such products as electric meter covers, dental appliance cases and spools. With 95 employees operating 23 molding machines in a 30,000 square foot plant, Itech wanted to reduce man hours and increase efficiency.