Download PDF
East Branch Engineering Uses Shoptech Customer Community to Connect With Other Shop Owners
Technology Category
- Platform as a Service (PaaS) - Data Management Platforms
Applicable Functions
- Discrete Manufacturing
Use Cases
- Manufacturing System Automation
Services
- Software Design & Engineering Services
The Challenge
In 2006, East Branch Engineering was growing rapidly. The shop had more customers, more jobs, and more administrative tasks than they had ever had before. For years East Branch had used a software platform to manage scheduling, estimating, and other important functions. However, with the increasing volume of business, the shop found that the software’s limitations were too much to handle. Data wouldn’t transfer between modules so there was a lot of data entry and time-wasting administrative work. They decided pretty quickly that they needed a new solution.
About The Customer
In 1989, Paul Guidotti launched his own small lot, complex part job shop in his family’s basement. Twenty-seven years later, that one-man home business has evolved into East Branch Engineering, a Connecticut-based shop with 14 employees. East Branch still specializes in small lots and complex jobs, but today the shop serves customers in a wide range of industries, including healthcare, consumer, and even high-voltage power.
The Solution
Their search quickly led them to Shoptech and E2. According to Chris, it was clear that E2 was the software that East Branch was looking for. He said, “The automation in E2 is so convenient. You input data once and it’s immediately available everywhere. I can generate a quote and then we have that information in the system to schedule the job, order the materials, and for anything else we need to do.” Today, East Branch uses E2 for nearly every function in the shop. They use it for estimating, scheduling, material management, quality control, and more. Chris said that the only function they don’t use E2 for is customer relationship management.
Operational Impact
Related Case Studies.
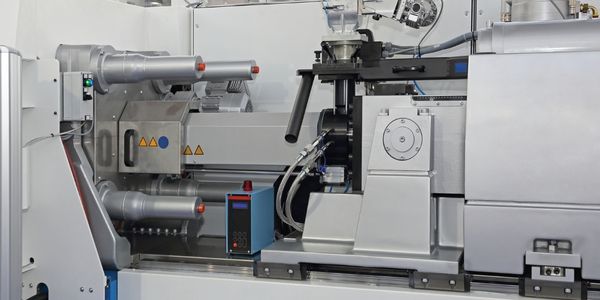
Case Study
Plastic Spoons Case study: Injection Moulding
In order to meet customer expectations by supplying a wide variety of packaging units, from 36 to 1000 spoons per package, a new production and packaging line needed to be built. DeSter wanted to achieve higher production capacity, lower cycle time and a high degree of operator friendliness with this new production line.
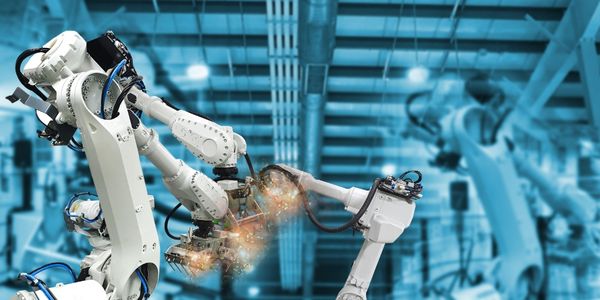
Case Study
Robot Saves Money and Time for US Custom Molding Company
Injection Technology (Itech) is a custom molder for a variety of clients that require precision plastic parts for such products as electric meter covers, dental appliance cases and spools. With 95 employees operating 23 molding machines in a 30,000 square foot plant, Itech wanted to reduce man hours and increase efficiency.
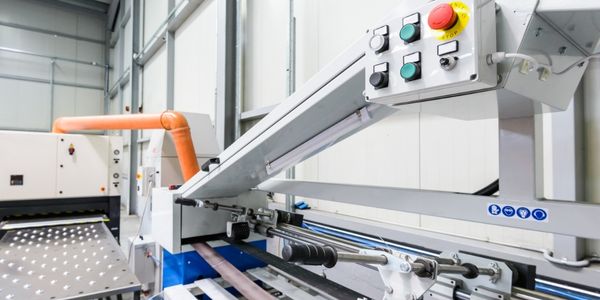
Case Study
Fully Automated Visual Inspection System
Tofflon has developed a fully automatic machine that uses light to inspect vials, medicine bottles, or infusion containers for glass fragments, aluminum particles, rubber grains, hairs, fibers, or other contaminants. It also detects damaged containers with cracks or inclusions (microscopic imperfections), automatically removing faulty or contaminated products. In order to cover all production processes for freeze-dried pharmaceuticals, Tofflon needed to create an open, consistent, and module-based automation concept.
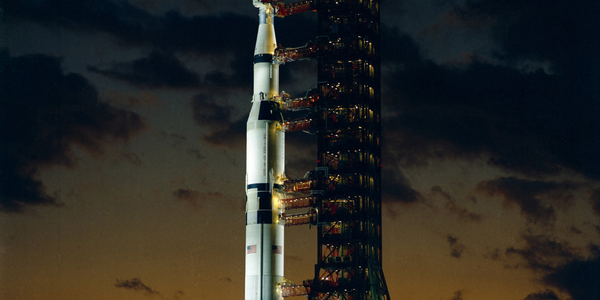
Case Study
SAP Leonardo Enabling Rocket Science
At times, ULA has as many as 15 different operating systems dedicated to overlapping processes, such as rocket design, testing, and launch. Multiple systems created unnecessary costs and unwanted confusion among workers at offices, factories, and launch sites in different location. In order to improve collaboration and transparency during vital activities that directly influence mission success, ULA wanted to improve data sharing and streamline manufacturing processes.
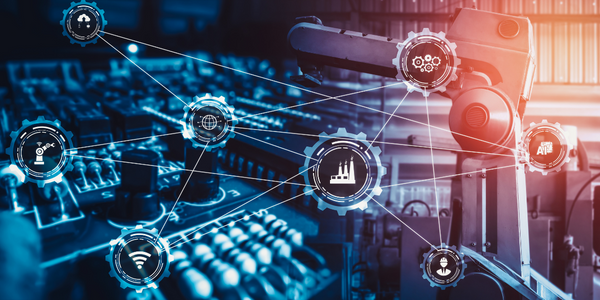
Case Study
IIC Smart Manufacturing Connectivity for Brown-field Sensors
The discrete manufacturing domain is characterized by a strictly hierarchical structure of the automation systems, commonly referred to as the automation pyramid. Data acquired by a sensor typically flows through an IO-module into a Programmable Logic Controller (PLC) which manages the local real-time control system. As all process data are concentrated in the PLC, re-programming the PLC and thus, implementing interfaces to access these data appear to be the natural choice to transfer them to the IT system. However, for brownfield installations this choice has proven impracticable for the following two reasons:In brownfield facilities, PLC usually operate within a once-specified environment and are rarely re-programmed. That is why the active staff is often not familiar with the code and lacks of the competence to modify the existing implementation in a reasonable amount of time.Furthermore, for cost reasons, any PLC was selected to exactly match the requirements of the environment within which it was intended to operate. That is why it cannot be assumed that a PLC will be able to support additional tasks such as communicating data through additional interfaces.
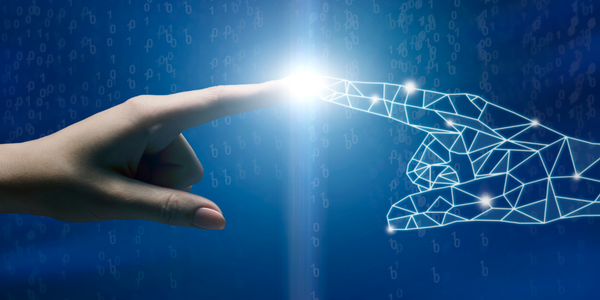
Case Study
Human–Robot Control
Industry 4.0 is changing the way manufacturing industry operates. Increasingly more manufacturers are leveraging advanced technologies such as robotics and automation systems to improve productivity and efficiency. As a result, human–machine interfaces (HMIs) are becoming more important in their role in the digital connectedness of humans and machines. However, using the wrong HMI can lengthen development times and increase implementation costs.