Download PDF
ECA Moves Up the Leather Value Chain with Zero-Buffer Cutting
Technology Category
- Functional Applications - Manufacturing Execution Systems (MES)
- Functional Applications - Product Lifecycle Management Systems (PLM)
Applicable Industries
- Automotive
- Consumer Goods
Applicable Functions
- Process Manufacturing
- Quality Assurance
Use Cases
- Predictive Maintenance
- Manufacturing System Automation
- Factory Operations Visibility & Intelligence
Services
- System Integration
- Training
- Software Design & Engineering Services
The Challenge
ECA, a Belgian automotive supplier, faced the challenge of increasing their yield of leather cut parts while reducing labor. The surge in demand for leather interiors in vehicles made it critical for ECA to meet changing consumer preferences quickly. The traditional die cutting process was labor-intensive and inflexible, requiring different cutting knives for each car model. This process also incurred high OEM tooling costs and long start-up times, making it difficult for ECA to remain competitive in a rapidly evolving supply chain.
About The Customer
Founded in 1981, ECA NV is a family-run firm located in Assenede, Belgium. The company specializes in aftermarket vehicle upholstery, particularly leather, and the manufacturing of car mats for OEMs. ECA employs 130 people and is part of the ECA Group, which includes Berco, I M Kelly, and Tiscotex NV. Over the years, ECA has built a reputation for quality and innovation in the automotive aftermarket industry. The company has been a customer of Lectra since 2006, leveraging their expertise to transition from manual to automated leather cutting processes.
The Solution
To address these challenges, ECA turned to Lectra's Versalis® leather cutting solution. This automated system significantly optimized material usage and reduced manpower requirements. The Versalis system enabled ECA to implement automatic nesting, allowing for zero-buffer cutting and improving hide efficiency. The switch from die cutting to automation reduced start-up times and eliminated OEM tooling costs. Over five years, ECA continued to upgrade its installed base with Lectra's leather- and textile-cutting solutions and prototyping software. Benchmark tests at Lectra's R&D center in Bordeaux convinced ECA of the exceptional performance of VersalisAuto, leading to material savings of 10% compared to their previous solution.
Operational Impact
Quantitative Benefit
Related Case Studies.
.png)
Case Study
Improving Vending Machine Profitability with the Internet of Things (IoT)
The vending industry is undergoing a sea change, taking advantage of new technologies to go beyond just delivering snacks to creating a new retail location. Intelligent vending machines can be found in many public locations as well as company facilities, selling different types of goods and services, including even computer accessories, gold bars, tickets, and office supplies. With increasing sophistication, they may also provide time- and location-based data pertaining to sales, inventory, and customer preferences. But at the end of the day, vending machine operators know greater profitability is driven by higher sales and lower operating costs.
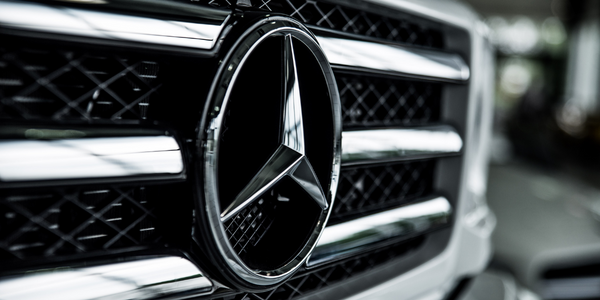
Case Study
Integral Plant Maintenance
Mercedes-Benz and his partner GAZ chose Siemens to be its maintenance partner at a new engine plant in Yaroslavl, Russia. The new plant offers a capacity to manufacture diesel engines for the Russian market, for locally produced Sprinter Classic. In addition to engines for the local market, the Yaroslavl plant will also produce spare parts. Mercedes-Benz Russia and his partner needed a service partner in order to ensure the operation of these lines in a maintenance partnership arrangement. The challenges included coordinating the entire maintenance management operation, in particular inspections, corrective and predictive maintenance activities, and the optimizing spare parts management. Siemens developed a customized maintenance solution that includes all electronic and mechanical maintenance activities (Integral Plant Maintenance).