Download PDF
Emhart Glass Enhances Bottle Creation Process with ANSYS SpaceClaim
Technology Category
- Analytics & Modeling - Digital Twin / Simulation
- Sensors - Environmental Sensors
Applicable Industries
- Equipment & Machinery
- Glass
Applicable Functions
- Product Research & Development
Use Cases
- Digital Twin
- Virtual Reality
Services
- System Integration
- Testing & Certification
The Challenge
Emhart Glass Research Center, a leading international supplier of equipment, controls, and parts to the glass container industry, was facing challenges in their bottle creation process. The Center, which focuses on developing enhanced glassforming methods, increasing automation and improving yields, was struggling with the complexities of heat, fluid, and air issues in their modeling process. Senior Mechanical Engineer, Pierre Ngankeu, was tasked with performing multi-physics analysis on design concepts, with a focus on fluid dynamics and heat transfer during the molding process. However, the modeling and pre-processing were time-consuming, often taking days for each simulation. Pierre had to work with foreign CAD data, deal with meshing and density issues, and create the flow domain before analysis. Additionally, there was usually not a lot of data available for many of the processes, adding to the complexity of preparing models for simulation.
About The Customer
Emhart Glass Research Center is a part of Emhart Glass, a Bucher company, and is a leading international supplier of equipment, controls, and parts to the glass container industry. The Center focuses on developing enhanced glassforming methods, increasing automation, and improving yields. It includes a complete production line, enabling Emhart engineers and researchers to test new ideas in an industrial environment. The successful concepts can then be translated to the Equipment Innovations team to address challenges such as furnace variations, glass property changes, and cooling-wind fluctuations.
The Solution
To address these challenges, Emhart Glass implemented ANSYS SpaceClaim, a 3D modeling software solution. ANSYS SpaceClaim's integration with ANSYS enabled the changes that Pierre made in ANSYS SpaceClaim to populate ANSYS automatically. This eliminated the need for Pierre to extract information from Pro/ENGINEER and convert that data into a STEP or ACIS file before starting to prepare the model for analysis. ANSYS SpaceClaim also simplified the process of creating and editing cross-sectional designs, which was particularly beneficial as many of the designs were rotationally symmetric. Once optimized, Pierre could send the solids back to the design team using Pro/ENGINEER. This streamlined process significantly reduced the time and complexity involved in preparing models for simulation, enabling Pierre to focus more on analyzing new product concepts and addressing customer challenges.
Operational Impact
Related Case Studies.
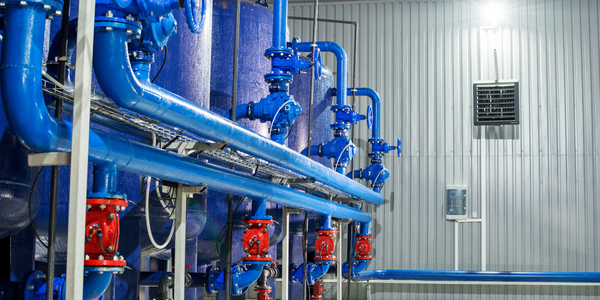
Case Study
Smart Water Filtration Systems
Before working with Ayla Networks, Ozner was already using cloud connectivity to identify and solve water-filtration system malfunctions as well as to monitor filter cartridges for replacements.But, in June 2015, Ozner executives talked with Ayla about how the company might further improve its water systems with IoT technology. They liked what they heard from Ayla, but the executives needed to be sure that Ayla’s Agile IoT Platform provided the security and reliability Ozner required.
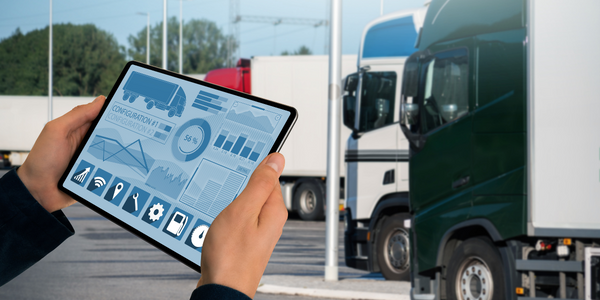
Case Study
IoT enabled Fleet Management with MindSphere
In view of growing competition, Gämmerler had a strong need to remain competitive via process optimization, reliability and gentle handling of printed products, even at highest press speeds. In addition, a digitalization initiative also included developing a key differentiation via data-driven services offers.
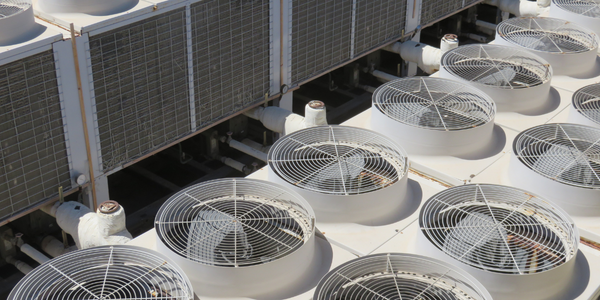
Case Study
Predictive Maintenance for Industrial Chillers
For global leaders in the industrial chiller manufacturing, reliability of the entire production process is of the utmost importance. Chillers are refrigeration systems that produce ice water to provide cooling for a process or industrial application. One of those leaders sought a way to respond to asset performance issues, even before they occur. The intelligence to guarantee maximum reliability of cooling devices is embedded (pre-alarming). A pre-alarming phase means that the cooling device still works, but symptoms may appear, telling manufacturers that a failure is likely to occur in the near future. Chillers who are not internet connected at that moment, provide little insight in this pre-alarming phase.
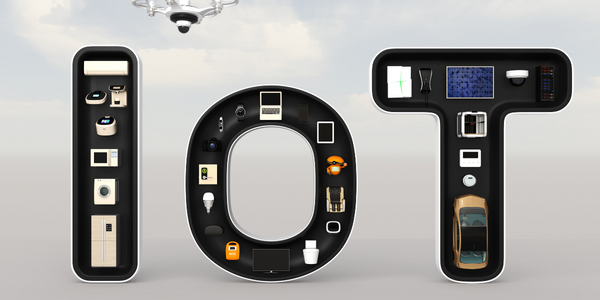
Case Study
Premium Appliance Producer Innovates with Internet of Everything
Sub-Zero faced the largest product launch in the company’s history:It wanted to launch 60 new products as scheduled while simultaneously opening a new “greenfield” production facility, yet still adhering to stringent quality requirements and manage issues from new supply-chain partners. A the same time, it wanted to increase staff productivity time and collaboration while reducing travel and costs.
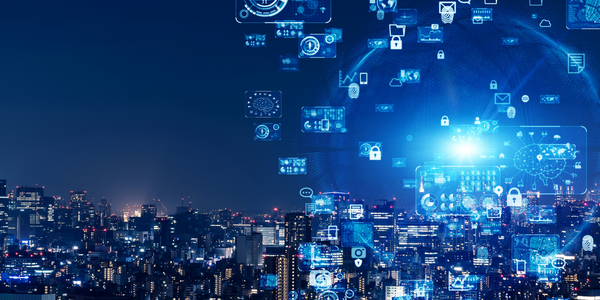
Case Study
Integration of PLC with IoT for Bosch Rexroth
The application arises from the need to monitor and anticipate the problems of one or more machines managed by a PLC. These problems, often resulting from the accumulation over time of small discrepancies, require, when they occur, ex post technical operations maintenance.
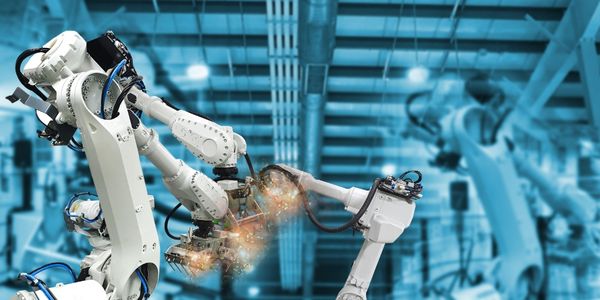
Case Study
Robot Saves Money and Time for US Custom Molding Company
Injection Technology (Itech) is a custom molder for a variety of clients that require precision plastic parts for such products as electric meter covers, dental appliance cases and spools. With 95 employees operating 23 molding machines in a 30,000 square foot plant, Itech wanted to reduce man hours and increase efficiency.