FMCG Case Study – CPG Line Monitoring
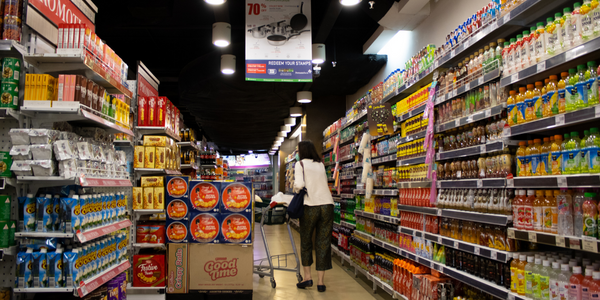
- Analytics & Modeling - Edge Analytics
- Analytics & Modeling - Real Time Analytics
- Application Infrastructure & Middleware - Data Visualization
- Automation & Control - Distributed Control Systems
- Automation & Control - Supervisory Control & Data Acquisition (SCADA)
- Functional Applications - Remote Monitoring & Control Systems
- Infrastructure as a Service (IaaS)
- Networks & Connectivity - Gateways
- Networks & Connectivity - Wireless Local Area Network
- Platform as a Service (PaaS) - Application Development Platforms
- Platform as a Service (PaaS) - Data Management Platforms
- Consumer Goods
- Discrete Manufacturing
- Machine Condition Monitoring
- Root Cause Analysis & Diagnosis
The leading CPG company operates several warehouses, mostly closer to the last distribution point (Large retailers). Products in various categories are packaged in specific delivery or display cartons at these facilities. As most CPG businesses consist of high volume with low margins, optimizing every operation and effective utilization of resources add up to profit margins. The key problem at these warehouses is the lack of visibility into reasons for machine breakdowns or idle time, thereby delay in delivery. The sunrise meetings lead to post-mortem of delivery issues like delay or quality. The customer wanted to implement real-time line monitoring and alert system to gain control over downtime issues and implement improvement measures.
As packaging lines carry variety of old and new machines, many aren’t designed to share data. The solution demanded retrofitting of hardware and custom dashboards to visualize multiple lines and machines. Altizon, along with the hardware partner, designed an integrated IoT solution. It deployed high quality wireless object detection sensors on case sealers, wrapping machines, and box printers to capture real-time operating pulse. The 24/7 real-time machine data at
Datonis Edge helped analyze equipment failure & generate alerts. The aggregated data was processed at Datonis IoT cloud to analyze production line throughput and offer tailored visualization and BI reports. The business intelligence reports with machine idle time, breakdown reason codes, and overall productivity/OEE data helped management in better planning and addressing issues.
Related Case Studies.
.png)
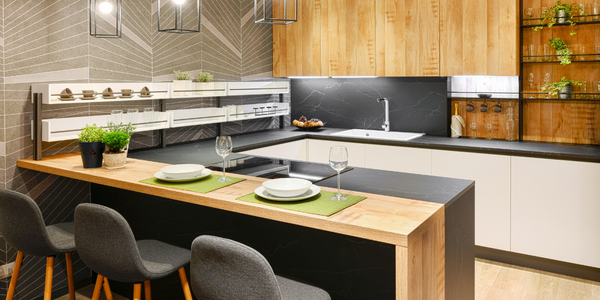
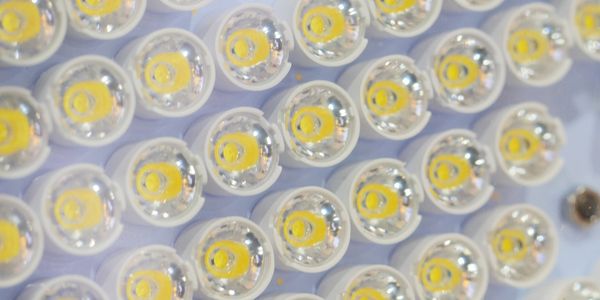
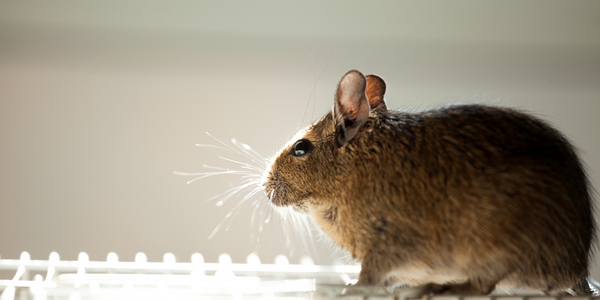