Download PDF
Genrocket Automotive Parts Retailer Case Study
Technology Category
- Functional Applications - Inventory Management Systems
- Application Infrastructure & Middleware - Data Exchange & Integration
- Functional Applications - Remote Monitoring & Control Systems
Applicable Industries
- Automotive
- Retail
Applicable Functions
- Quality Assurance
- Warehouse & Inventory Management
Use Cases
- Inventory Management
- Predictive Maintenance
- Remote Asset Management
Services
- Software Design & Engineering Services
- System Integration
The Challenge
The automotive parts retailer faced significant challenges in maintaining efficient inventory management and provisioning new store environments. The retailer needed to ensure that inventory levels were accurately updated in real-time to meet customer demands and provide suggestions for nearby stores when stock was low. Additionally, creating a new store environment for testing purposes was a complex and time-consuming process, requiring data for multiple local databases and integration with various systems. The existing automated process took several hours to create a new store and generate the necessary test data, hindering the retailer's ability to quickly adapt to market demands.
About The Customer
The customer is a major automotive parts retailer operating in the highly competitive $130 billion-dollar automotive aftermarket industry. This industry is characterized by a mix of local brick-and-mortar retailers and online suppliers catering to both DIY consumers and commercial mechanics. The retailer has established a strong presence through superior customer service, expansion of retail locations, and the addition of regional distribution hubs. These hubs stock tens of thousands of items, enabling rapid resupply of surrounding stores and providing customers with more buying options and faster delivery. The retailer relies heavily on its information systems to manage inventory levels efficiently and support the provisioning of new store locations. To maintain its competitive edge against e-commerce giants like Amazon, the retailer sought to enhance its software testing capabilities with the help of GenRocket's Enterprise Test Data Automation solution.
The Solution
GenRocket provided a comprehensive solution to address the retailer's software testing challenges. For the first use case, which involved store inventory adjustment, GenRocket implemented a workflow that integrated with the existing test case. This workflow included using GroovyScriptReceiver to convert binary data to a fixed file format, running a GenRocket Scenario for synthetic data replacement, and converting the fixed file back to binary format. Additionally, GenRocket performed SQL updates on store quantities within a database and used the GenRocket API to dynamically update scenarios with store numbers, ensuring real-time updates for testing purposes. For the second use case, which involved provisioning a new store environment, GenRocket broke down the test data requirements into different epics and phases. The solution included generating test data for various databases and integrating it with the customer's existing automation framework. The phased approach allowed for incremental implementation, starting with basic test data integration and progressing to more advanced integration. By leveraging GenRocket's capabilities, the retailer was able to streamline the creation of new store environments and ensure accurate and efficient inventory management.
Operational Impact
Quantitative Benefit
Related Case Studies.
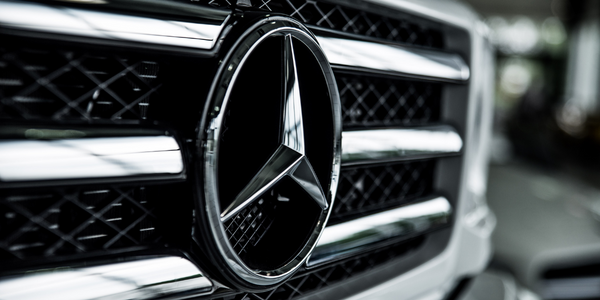
Case Study
Integral Plant Maintenance
Mercedes-Benz and his partner GAZ chose Siemens to be its maintenance partner at a new engine plant in Yaroslavl, Russia. The new plant offers a capacity to manufacture diesel engines for the Russian market, for locally produced Sprinter Classic. In addition to engines for the local market, the Yaroslavl plant will also produce spare parts. Mercedes-Benz Russia and his partner needed a service partner in order to ensure the operation of these lines in a maintenance partnership arrangement. The challenges included coordinating the entire maintenance management operation, in particular inspections, corrective and predictive maintenance activities, and the optimizing spare parts management. Siemens developed a customized maintenance solution that includes all electronic and mechanical maintenance activities (Integral Plant Maintenance).
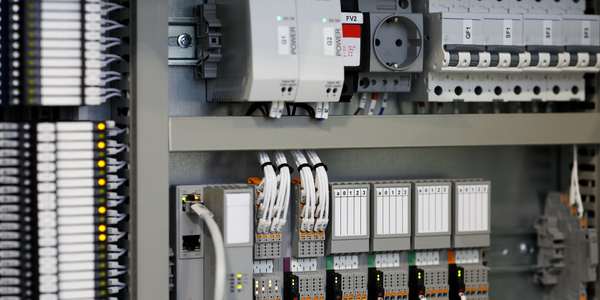
Case Study
Improving Production Line Efficiency with Ethernet Micro RTU Controller
Moxa was asked to provide a connectivity solution for one of the world's leading cosmetics companies. This multinational corporation, with retail presence in 130 countries, 23 global braches, and over 66,000 employees, sought to improve the efficiency of their production process by migrating from manual monitoring to an automatic productivity monitoring system. The production line was being monitored by ABB Real-TPI, a factory information system that offers data collection and analysis to improve plant efficiency. Due to software limitations, the customer needed an OPC server and a corresponding I/O solution to collect data from additional sensor devices for the Real-TPI system. The goal is to enable the factory information system to more thoroughly collect data from every corner of the production line. This will improve its ability to measure Overall Equipment Effectiveness (OEE) and translate into increased production efficiencies. System Requirements • Instant status updates while still consuming minimal bandwidth to relieve strain on limited factory networks • Interoperable with ABB Real-TPI • Small form factor appropriate for deployment where space is scarce • Remote software management and configuration to simplify operations