Download PDF
Getting the Most Out of Enterprise Resource Planning with DELMIAWorks ERP
Technology Category
- Functional Applications - Enterprise Resource Planning Systems (ERP)
Applicable Industries
- Automotive
- Electronics
- Healthcare & Hospitals
Applicable Functions
- Discrete Manufacturing
- Procurement
Use Cases
- Manufacturing System Automation
- Inventory Management
Services
- System Integration
- Training
The Challenge
Thogus Products Company, a custom plastic injection-molder and contract manufacturer, was facing a changing business environment. The company's focus was shifting from automotive parts to a diverse product mix from various industries. This shift required improved access to and availability of critical business and production operational data, increased productivity, reduced data storage costs, and support for growth. The company's previous data system was not used properly, leading to bloated data storage costs and unreliable information. The company needed a system that would eliminate waste, simplify processes, and provide real-time insights into all manufacturing operations.
About The Customer
Thogus Products Company is a family-owned, custom plastic injection-molder and contract manufacturer based in Avon Lake, Ohio. Founded in 1950, the company operates 24/7 and offers just-in-time deliveries. Thogus is known for its injection-molding expertise, helping clients choose the right types of plastic for their products, make tooling and mold transfer decisions, and even manufacture custom fittings when necessary. The company also produces its own proprietary line of plastic tube and hose fittings for low-pressure applications. Thogus serves customers in a variety of industries and is committed to creating lasting partnerships with clients and supply chain partners.
The Solution
To address its challenges, Thogus implemented the DELMIAWorks enterprise resource planning (ERP) system from Dassault Systèmes in 2021. The system includes modules for ERP, Quality Management, Document Control, Forecasting, Tooling Management, Preventive Maintenance (MRO– Maintenance, Repair, Overhaul), RealTime Production Monitoring, and Warehouse Management. The DELMIAWorks ERP system was chosen because it is specifically designed for injection molding, machining, production, and manufacturing-services-based enterprises. It provides accurate information on inventories and production operations as well as business and financial information. The implementation of the system was made mandatory for all employees and they were trained on how to use it.
Operational Impact
Quantitative Benefit
Related Case Studies.
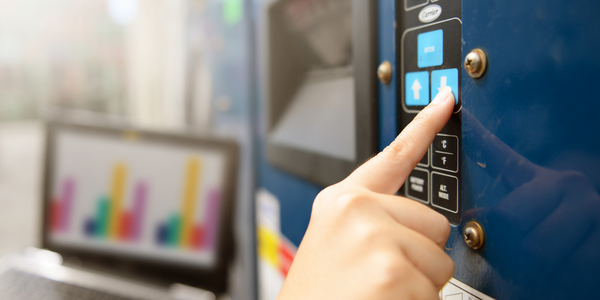
Case Study
Remote Temperature Monitoring of Perishable Goods Saves Money
RMONI was facing temperature monitoring challenges in a cold chain business. A cold chain must be established and maintained to ensure goods have been properly refrigerated during every step of the process, making temperature monitoring a critical business function. Manual registration practice can be very costly, labor intensive and prone to mistakes.
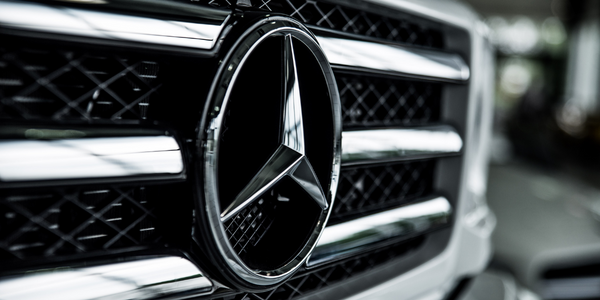
Case Study
Integral Plant Maintenance
Mercedes-Benz and his partner GAZ chose Siemens to be its maintenance partner at a new engine plant in Yaroslavl, Russia. The new plant offers a capacity to manufacture diesel engines for the Russian market, for locally produced Sprinter Classic. In addition to engines for the local market, the Yaroslavl plant will also produce spare parts. Mercedes-Benz Russia and his partner needed a service partner in order to ensure the operation of these lines in a maintenance partnership arrangement. The challenges included coordinating the entire maintenance management operation, in particular inspections, corrective and predictive maintenance activities, and the optimizing spare parts management. Siemens developed a customized maintenance solution that includes all electronic and mechanical maintenance activities (Integral Plant Maintenance).
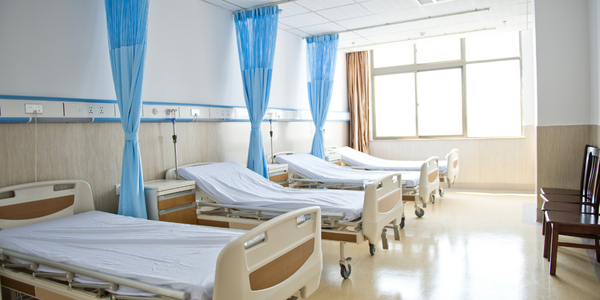
Case Study
Hospital Inventory Management
The hospital supply chain team is responsible for ensuring that the right medical supplies are readily available to clinicians when and where needed, and to do so in the most efficient manner possible. However, many of the systems and processes in use at the cancer center for supply chain management were not best suited to support these goals. Barcoding technology, a commonly used method for inventory management of medical supplies, is labor intensive, time consuming, does not provide real-time visibility into inventory levels and can be prone to error. Consequently, the lack of accurate and real-time visibility into inventory levels across multiple supply rooms in multiple hospital facilities creates additional inefficiency in the system causing over-ordering, hoarding, and wasted supplies. Other sources of waste and cost were also identified as candidates for improvement. Existing systems and processes did not provide adequate security for high-cost inventory within the hospital, which was another driver of cost. A lack of visibility into expiration dates for supplies resulted in supplies being wasted due to past expiry dates. Storage of supplies was also a key consideration given the location of the cancer center’s facilities in a dense urban setting, where space is always at a premium. In order to address the challenges outlined above, the hospital sought a solution that would provide real-time inventory information with high levels of accuracy, reduce the level of manual effort required and enable data driven decision making to ensure that the right supplies were readily available to clinicians in the right location at the right time.